Technology: Slipform paving
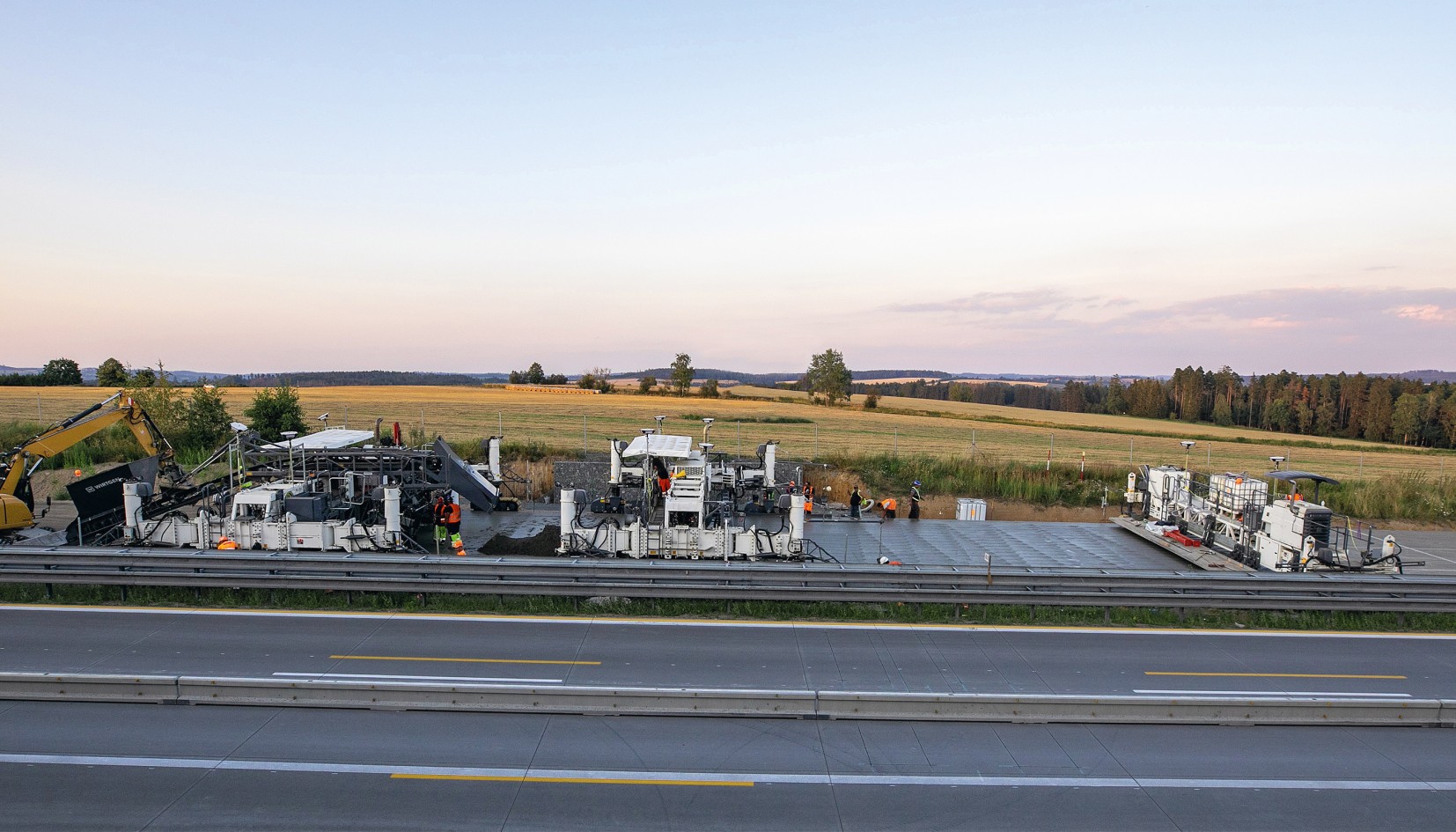
We offer mature processes for facilitating the construction of heavy-duty motorways or airport runways an the production of poured-in-place concrete profiles. Make use of our broad offer of machines for high precision in concrete paving.
Become acquainted with the operating principle and technical components of concrete paving. Get to know the inset and offset paving methods, and learn more about our standard and special applications.
In offset application, mixer trucks deliver the concrete into the receiving hopper of the slipform paver. Transport to the mould is effected via a slewable belt or auger conveyor. Depending on the paver model, the belt conveyor is available in different lengths and in folding design. The auger conveyor is also available in different designs. And whether belt or auger conveyor: all settings, such as conveying speed, angle of incline or position can be made at the mere push of a button. A separate cross-feeding auger offers numerous advantages. The mixer truck can drive right in front of the slipform paver, thus eliminating the need to close off additional traffic lanes. The cross-feeding auger is the ideal solution also whenever larger volumes of concrete are required as a material buffer, for example, when paving in narrow bends where it is not possible for the mixer truck to continue the uninterrupted delivery of concrete to the slipform paver.
In inset application, the concrete is either deposited right in front of the slipform paver or is fed in front of the machine from the side via a belt conveyor or side feeder. In the next step, the concrete is distributed evenly across the full paving width by a spreading auger or spreading plough. Homogeneous compaction of the concrete is effected by means of integrated electric or hydraulic vibrators. The inset mould forms the concrete slab to the specified thickness and width while the slipform paver advances. In addition, a dowel bar inserter can be integrated which inserts the dowel bars into the concrete as specified parallel to the paver’s direction of travel. Central tie bars or side tie bars can be inserted transverse to the concrete pavement. The surface is levelled off transverse to the paver’s direction of travel by the oscillating beam. The “grinding movement” produces a small concrete roll in front of the beam which adds to the high quality of the concrete surface. In the next step, a super smoother is used to finish the concrete slab.
Flexibility for concrete paving
The innovative system for extending the working width enables fast and convenient on-site reconfiguration of the paving mould. The result is shorter reconfiguration times and maximum machine utilisation rates while maintaining the usual high quality.
The WPS 62(i) placer speader is normally used in combination with a slipform paver and a texture curing machine. While trucks and semitrailers successively dump concrete into the conveyor belt unit’s large receiving hopper, the conveyor belt guides the conveyed material to the center of the road. The WPS 62(i) placer speader uses a spreading auger to spread the laid concrete and paves it uncompacted with a narrower width and greater thickness than the following slipform paver. Finally, the paver paves the pre-poured concrete in the required width and thickness together with the pre-laid reinforcement. To complete the process, the texture curing machine produces a defined surface structure and sprays evaporation protection onto the fresh concrete road surface.