Hot recycling
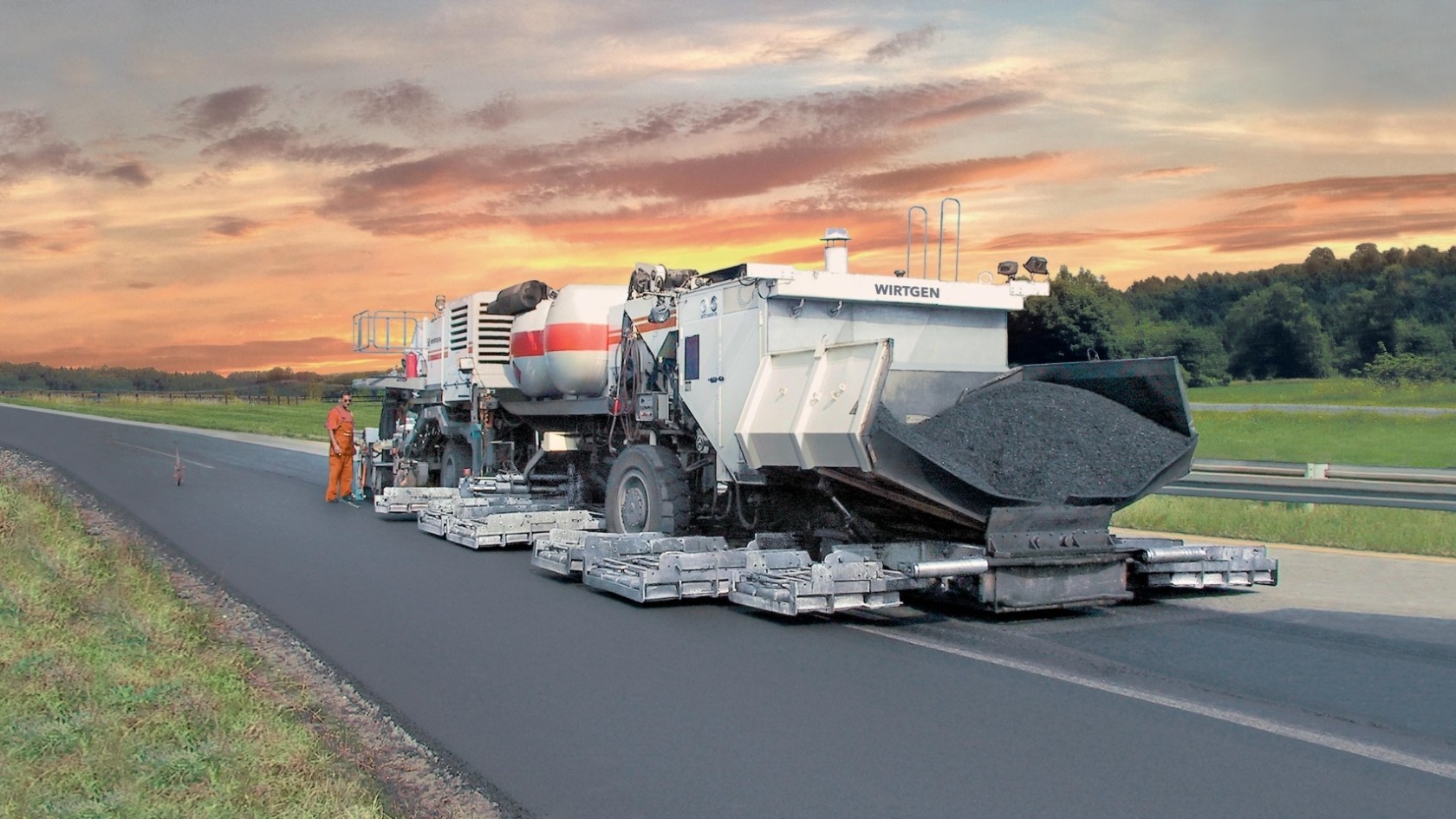
The hot recycling method is used solely for the rehabilitation of damaged asphalt surface courses, which is why an intact layer structure is of vital importance. The pavement structure underlying the surface course must fully comply with all requirements in terms of bearing capacity and frost resistance.
The hot recycler processes the existing road pavement, improving it with virgin mix, if necessary. After completion of the recycling operation, the new surface course will fully comply with all requirements once again.
Hot recycling improves all relevant properties of both the surface and the pavement profile, as well as the composition of the aggregate fractions in the surface course layer. It helps to restore lacking skid resistance, to ensure water drainage, and to eliminate wheel ruts. Hot recycling offers a tremendous saving potential. Around 85% of truck transports, and 70% of virgin mix can be saved in comparison to replacing the pavement using a milling machine and road paver.
Paving of the top layer, up to a working width of 4.5 m.
The surface course is heated up to 150°C by a panel heating machine with gas-fired infrared heating panels so that the hot recycler can then scarify, remove, process and repave the softened asphalt. In this way, the road's non-skid properties can be restored, water can run off again and ruts are eliminated. The potential savings are enormous.
An approximately 5 km long section of road is to be recycled across a width of 5 m, which equals a total area of some 25,000 m². Assuming a weight of 200 kg per m² of surface course, the “classical” method – replacing the pavement – would require around 200 truck transports: 100 for transporting the milled material from site, and 100 for supplying virgin asphalt mix. 30 kg of virgin mix per m² of surface course are added when adhering to the standards of hot recycling, which requires just 30 truck loads of 25 tons each – 170 less than with conventional rehabilitation methods.