All roads lead to ECO.
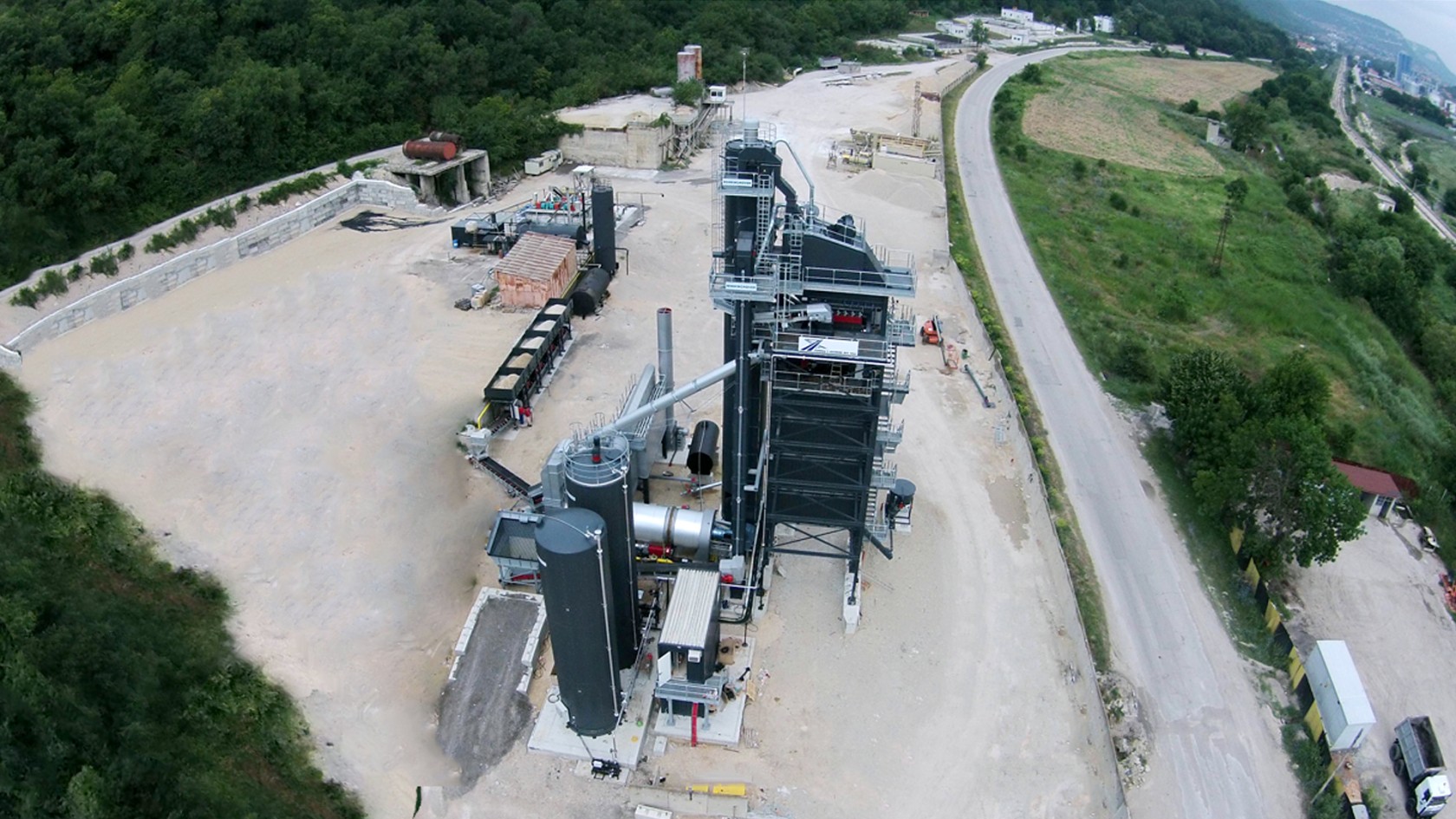
PIM PRO’s BENNINGHOVEN ECO 3000 is the very first plant in Bulgaria to produce low-temperature asphalt with foamed bitumen and mastic asphalt.
They combine outstanding plant quality with productivity and take frequent relocations in their stride: little wonder that ECO asphalt mixing plants from BENNINGHOVEN are in successful operation worldwide. Apart from their ease of transport, another key contributor to their success is their high flexibility, which enables customers and users to produce a variety of asphalt formulations – at mixing outputs of up to 320t/h.
Every investment a company makes is geared to specific objectives. PIM PRO, a construction company specializing in asphalt production and paving that operates its own quarry, asphalt mixing plants, polymer-modified bitumen plant as well as milling machines, pavers and rollers, had a highly ambitious objective in mind: the company wanted a new asphalt mixing plant at its Provadia site in Bulgaria that is capable of working more energy-efficiently while producing advanced, high-quality asphalt mixes. BENNINGHOVEN took on the challenge and, based on an ECO 3000 equipped with a number of innovative technologies, delivered a solution that even exceeded PIM PRO’s demands.
Rosen Koleliev, Managing Director PIM PRO
Sustainable resource management and energy-efficiency are issues that are gaining importance all over the world, as well as in Bulgaria. To meet these demands and additionally offer diverse and high-quality mixes, PIM PRO rely on groundbreaking technology from BENNINGHOVEN. With one and the same asphalt mixing plant, the company can supply and pave an extremely wide range of asphalt types, from cold or low-temperature asphalt and premium roller-compacted asphalt, to stone mastic and mastic asphalt. This also means the plant has to operate in a temperature range from 100 to 220°C (relative to the end product) and produce sophisticated formulations with precision. When it comes to BENNINGHOVEN plants, even the standard versions can handle this extreme range. In other words, customers need not pay extra for optional heat-resistant components, because the screen media can withstand temperatures in the region of 400°C, such as are required to produce mastic asphalt. This clearly demonstrates the extreme robustness and high fabrication quality of BENNINGHOVEN equipment. PIM PRO’s BENNINGHOVEN ECO 3000 is the very first plant in Bulgaria to produce low-temperature asphalt with foamed bitumen and mastic asphalt.
As an all-rounder in road construction, PIM PRO also do a lot of road rehabilitation. The granulated RAP produced by WIRTGEN milling machines when removing asphalt pavements in need of rehabilitation serves as an input for new mix. Thanks to the BENNINGHOVEN cold recycling system for dosing into the mixer, this process is cost-effective and resource-conserving, because it enables 30% RAP to be fed directly into the mixer.
PIM PRO have gained a real competitive edge with a foamed bitumen module likewise integrated in the ECO 3000. With this innovative technology, which BENNINGHOVEN can easily retrofit in existing plants thanks to preinstalled interfaces, the temperature required to produce low-temperature asphalt can be reduced by about 50°C to 110°C, as opposed to the 160°C required for conventional asphalt. This reduces energy consumption for asphalt production by around 9kWh/t, which equates to 0.9l of heating oil. CO2 emissions are also reduced.
An optimum fill level in the mixer, together with thorough mixing as a result of the generous geometry of BENNINGHOVEN’s new weighing and mixing section, ensures premium mix quality. Starting with the ECO 2000 plant size, all weighing and mixing sections have the following preinstalled interfaces as standard for recycling feed, foamed bitumen feed, granulate feed, powder feed, fibrous material feed, adhesive feed or bag feed. With this feature, the ECO plants are ready for future retrofits. Further advantages of the new weighing and mixing section include, among other things, very good accessibility in all areas, plug & play connections for quick set-up, and optimum illumination with LED technology.
BENNINGHOVEN have always relied on loading skip technology as the link between mixer and mixed material storage silo. For their ECO asphalt mixing plants, BENNINGHOVEN have now developed a new, more cost-efficient alternative to the skip track and had it patented. The new diverter chute unit features a purely mechanical design that is not at all susceptible to malfunctions. The intelligent design means that no sensor systems, engines, brakes, etc. are required, thus ensuring functional reliability worldwide. Another key improvement is fast and load-free positioning for silo selection. Segregation effects in the end product are minimized by active cross-mixing in the material transfer system while the proven geometry of the BENNINGHOVEN mixed material storage silos counteracts segregation in the mix.