BENNINGHOVEN TBA 4000
Rome, Italy
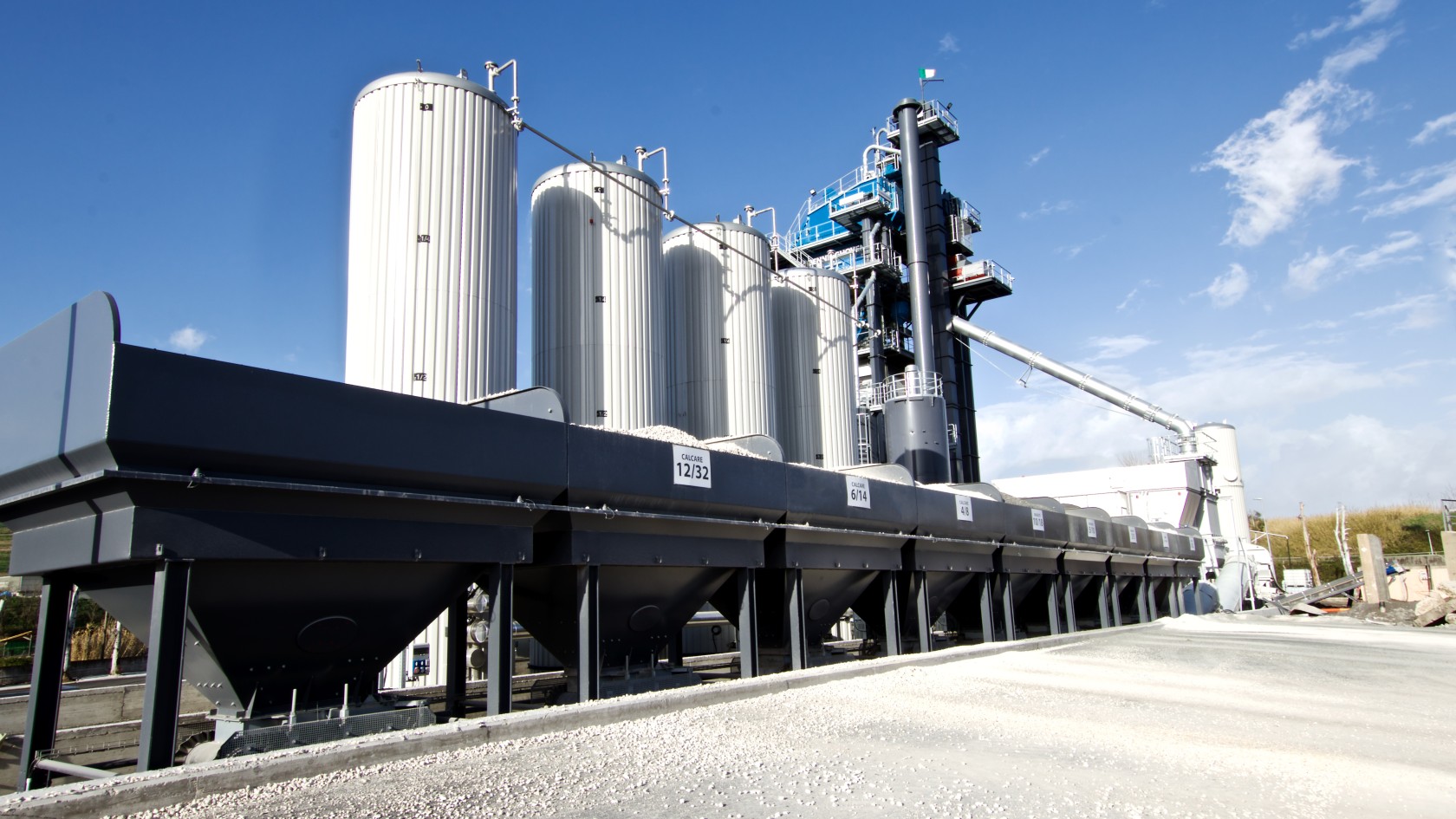
Quality and flexibility for the streets of Rome
Cicchetti has been an active supplier of asphalt products for the Rome region for many years. The continuously increasing requirements for the quality of the end product are and always have been an important factor that has to be achieved and explored.
It was the necessity to produce ever more innovative asphaltic mixtures using different additives while continuously increasing the quality of the end product that finally convinced the company owner to invest in a new asphalt mixing plant – one which can be a central sourcing point for road construction in Rome and is capable of meeting these high requirements and demands now and in the future.
After viewing various plants abroad, this decision had already been made several years ago. Due to delays in the required permits, however, it had to be postponed numerous times. The owner’s main objective – to keep the in-house asphalt mixing plant state-of-the-art at all times – was finally achieved last year with the new BENNINGHOVEN TBA 4000 asphalt mixing plant with a 4 t mixer and a nominal mixing capacity of 320 t/h.
The Italian company Cicchetti Appalti e Costruzioni decided to buy a new asphalt mixing plant: The BENNINGHOVEN TBA 4000 was the first choice for supplying asphalt for the streets of Rome in the future.
Roberto Berardi, Product Manager BENNINGHOVEN
Before the plant was planned, a lot of time and detailed work were invested in the precise layout of the construction site. This meticulous preliminary work allowed the new asphalt mixing plant to be safely installed while the old plant was still running, continuing to product asphaltic mixture while the TBA 4000 was being assembled. Other parts of this concept included optimising the positioning of the storage locations for the minerals, the processing of the recycling material and the manoeuvring of lorries for loading.
As the central control unit for the asphalt mixing plant, the command station was updated with the BENNINGHOVEN BLS 3000 control system: Examining the recycling material to be reused and in particular the accurate rendering of the recipes and the quality of the asphaltic mixture delivered to the customer are crucial aspects for a plant which produces exclusively for third parties. Material samples are extracted daily in order to guarantee the correct composition of the product for road construction.
In the context of re-using recycling material, a new screen unit was also purchased for screening the delivered recycling material into different fractions. This is the best way to ensure that the material can be added to the mixing process with the correct grain size. The screened recycling material is stored in the covered internal area to minimise dust at the construction site and to protect the processed material against rain. Without this protection, the material could re-absorb moisture which would have to be removed again during the drying process, requiring additional energy and costs. This measure substantially reduces fuel consumption for drying the mineral and increases the hourly output of the plant.
A 1.2 m difference in altitude at the construction site was created between the storage area for aggregates/recycling material and the area where the plant was installed. This omits the need for a feed ramp on the site.
Even though the previously used plant was not completely outdated, some weak points had become evident over the years which had to be addressed: the hourly output was increased to offer customers shorter wait times; the market requirement for offering ever more progressive products; the readiness to use recycling material and the continuously increasing necessity for reducing the environmental impact (odours, emissions, etc.).
With respect to emissions, the burner is now run with liquid gas instead of heating oil. Another special feature of the new burner is the afterburner unit, i.e. extracted bituminous vapours generated during the internal asphalt transfer from the mixer into the skip or the loading silo are transferred to the burner and burnt there. This not only drastically reduces contamination of the plant, but also allows the odours generated during certain processes to be eliminated as much as possible.
A special focus was also placed on stocking the raw materials for the final asphalt: A total of 9 feed hoppers for virgin mineral allow easy processing of mineral containing lime as well as basalt. 4 bitumen tanks allow the use of different bitumen types, depending on the recipe and on which is more suitable for the mixture to be produced, as well as two tanks for storing emulsions.
In addition to this, an increased focus was on the type and quality of bitumen heating and storage and the protection of all important components. Bitumen pumps, for example, were specially encapsulated to reduce noise and to protect them against the weather.
The requirements for the technology for using recycled material was carefully evaluated and coordinated after several visits to sites in Italy and abroad. The “multivariable” system was the most convincing: It allows the production of asphaltic mixture from screened recycling material (mandatory on the Italian market today) which is added to the mixing process cold.
The BENNINGHOVEN control system allows the use of a high ratio of recycling material. At the same time, this concepts eliminates the risk of mistakes with respect to the grading curve of the recipe, any process oils (rejuvenators) to be used or the production temperature of the mixture.
To ensure production of a new high-quality asphalt, the system allows the user to adapt the quantities of the different aggregates, the rejuventator, filler and bitumen – which are required for the best possible grading curve – depending on the quality and ratio of the recycling material used.
To meet the customer’s requirements, a large-capacity loading silo (two chambers with 76 t each) was selected to keep waiting times during loading of lorries at the site as short as possible.
Other important features are the screen unit with 6-fold screening and a screen surface of over 46 m² and a hot bin section with a total capacity of 80 t for storing the hot screened material. This ensures an unparalleled flexibility when handling a variety of different recipes. In addition, it helps to minimise plant starts/stops not connected to planned production and to provide optimum service to customers arriving without registering beforehand.
Always with the objective of being a sourcing point for the Roman market for many years and to providing customers with the best possible service and maximum professionalism, Cicchetti was willing to make the investment for purchasing and installing this plant.