Use of a material feeder in Johannesburg
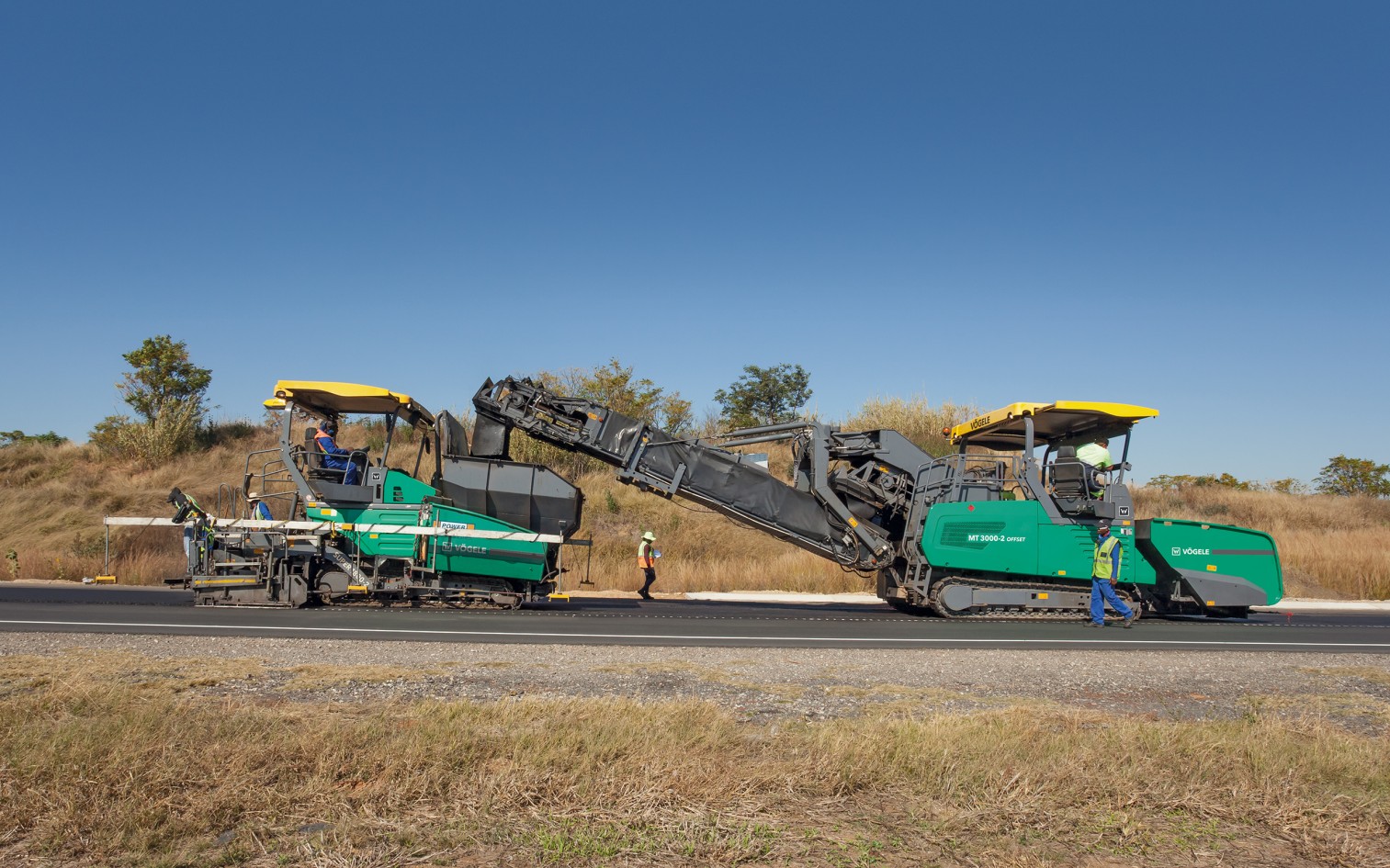
During a construction job in South Africa, it was scientifically proven by the University of Twente that the MT 3000-2 Offset PowerFeeder improves paving quality – among other things, using RoadScan, the innovative temperature measurement system from VÖGELE.
Johannesburg | South Africa
Organizing paving work so that it can proceed without interruption in order to enhance quality is one of the key reasons for using material feeders. And it‘s why in South Africa there is a strong focus on the decoupled transfer of mix from feed lorry to paver. Indeed, for major construction projects, SANRAL, the national roads agency, insists on the use of material feeders.
An advanced VÖGELE MT 3000-2 Offset PowerFeeder with a VÖGELE SUPER 1800-2 paver was used for the rehabilitation of a 4 km-long stretch of the N14 national route near Johannesburg by the South African construction company Power Construction (Pty) Ltd. On the job site, scientists from the University of Twente investigated whether the innovative VÖGELE material feeder improved the quality of the paved binder and surface courses.
One of the crucial factors was the temperature of the asphalt immediately after paving. The temperature was measured using two mutually independent systems, one of which was RoadScan, the non-contacting temperature-measurement system from VÖGELE. To provide a comparison, some sections were also completed without using a material feeder.
There are many different and compelling reasons for using material feeders – the first and foremost being quality and cost efficiency. It is hence in the interests of construction companies to opt for decoupled material transfer: while the road paver can focus entirely on paving, the material feeder handles the transfer of mix from the feed lorry, allowing both quality and productivity to be increased. The number of feed lorries and their waiting times can also be reduced, because material feeders buffer paving material, prolonging the window of time for continuous material supply. This, in a nutshell, is the theory. On the N14 job site, the aim was to see what impact the use of the VÖGELE material feeder had on pavement quality.
The MT 3000-2 Offset PowerFeeder features an intelligent material transport and storage concept with a total capacity of 43 t. Lorries carrying 25 t of mix can be unloaded within 60 seconds. That enabled paving on the job site located on the outskirts of Johannesburg to proceed without interruptions. This is of central importance to pavement quality, because interruptions cause a wide range of problems, the main one being the cooling of the mix and the associated reduction in compactability, not to mention the loss of time involved. Undesired side-effects such as these occurred on sections where the paving work was carried out without a material feeder for the purposes of comparison.
Dr Seirgei Miller,
University of Twente
The study by the University of Twente also revealed that the VÖGELE material feeder contributed to the homogeneity of the mix and hence improved pavement quality. In the VÖGELE MT 3000-2 Offset, conical augers in the receiving hopper ensure a uniform withdrawal of the mix from all areas of the receiving hopper and blending of the colder and warmer material. This reduces temperature fluctuations caused by transport. When combined with a trough-shaped conveyor, the VÖGELE design reliably prevents both mechanical and thermal segregation.
A homogeneous paving temperature is the foundation for uniform and even compaction. That is why the scientists from Twente recorded the temperature immediately after paving using two mutually independent measuring systems. One of these was attached directly to the hardtop of the SUPER 1800-2 paver, ensuring simple, convenient and reliable measurement: RoadScan from VÖGELE – an innovation first unveiled at Bauma 2016. A non-contacting temperature-measurement system, RoadScan allows paving teams to keep an eye on the temperature of the mix immediately after paving so that they can find appropriate solutions during the paving process, should the need for intervention arise. The thermoscan images are presented in real time on the colour display of the paver operator‘s ErgoPlus console. And, on completion of the construction project, contractors also have detailed evidence that the work was carried out within the correct temperature range – thanks to recorded GPS data including precise positioning.