Concrete paving at BBI Airport
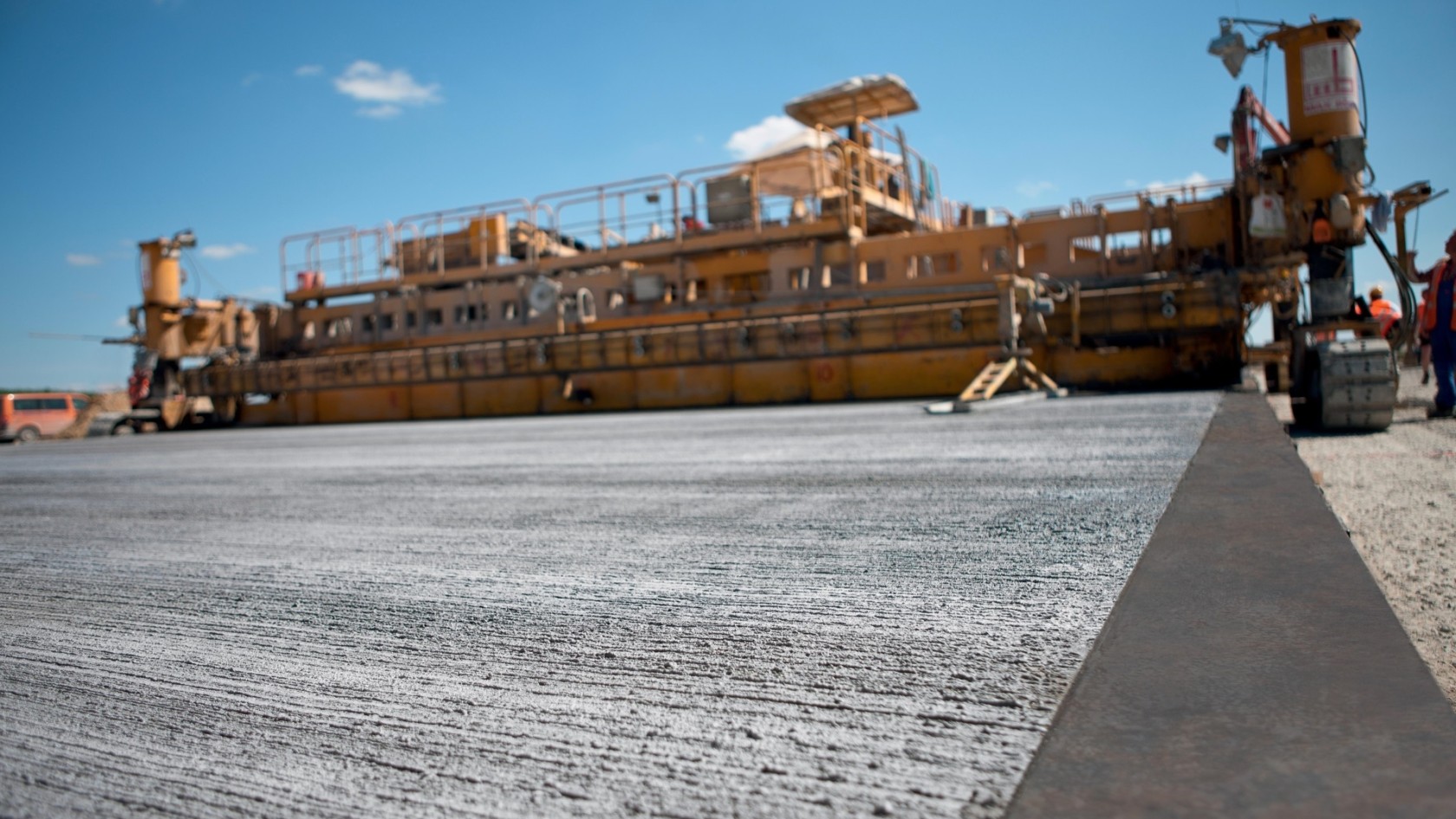
Berlin is Germany’s largest city and home to 3.5 million people. For historical reasons, the capital has long been served by several airports. Soon after the German reunification, Berlin’s airport operators began drawing initial plans for the construction of a new, central airport in the capital city that would offer sufficient capacities for decades to come. Implementation of these plans began in the summer of 2006: the existing Berlin Schönefeld Airport is expanded to become the new Berlin-Brandenburg International Airport, or simply “BBI”. A whole fleet of Wirtgen slipform pavers are playing a major part in the construction work. They are building the “airside” traffic infrastructure, which includes taxiways, aprons and ramps as well as the southern runway and covers an impressive total area of some 1.5 million square metres.
Mega project in the capital city
Berlin Tegel, Berlin Schönefeld and Berlin Tempelhof – whoever flew to Berlin used to arrive at one of these three airports. This situation led to the decision by Berlin’s airport operators to merge Berlin’s air traffic in a single location. In comparison with the fragmented airport system that developed due to the historical division of Berlin, this solution offers a positive overall ecological balance – both in terms of land use and in terms of noise and traffic pollution.
The decision to upgrade Schönefeld Airport to the capital city’s new, central airport was made in 1996. Tempelhof Airport was closed at the end of October 2008, and since the summer of 2006 construction operations have been in full swing right beyond the city limits. The southern runway of Schönefeld Airport will serve as the northern runway of the new airport. The scope of new construction includes an entirely new terminal building with direct rail connection as well as an additional, 4 km long runway to the south. State-of-the-art technology and an excellent infrastructure will soon offer both business travellers and tourists everything air passengers could wish for.
Aircraft still land and take off at the “old” Schönefeld Airport. Some 2 km to the south, the Wirtgen paving trains produce the concrete pavements of the southern taxiway A and B systems at working widths of up to 15 m.
Berlin among the world’s Top 50 airports
Opening of the new airport is scheduled for mid 2012. The “stepping stone to the east” will then commence operations with an initial capacity of up to 27 million passengers per year. Berlin-Brandenburg International will mainly serve destinations in Europe as well as selected long-haul connections for which Berlin offers the ideal strategic location: flight times to Eastern Europe and Asia are one hour less than from the established airport hubs in the west of the continent.
This will not only make Berlin number 3 among the German airports, surpassed only by Frankfurt and Munich, but one of the top 50 airports worldwide. The concepts of today include the possibility of future expansion: depending on development, the airport’s capacities can be expanded to up to 360,000 aircraft movements, or up to 45 million air passengers respectively, per year.
Fleet of Wirtgen slipform pavers in non-stop operation
For the purpose of implementing the large-scale project, contractors Gebrüder von der Wettern, Eurovia VBU and Eurovia Beton formed the “ARGE BBI GU II” joint venture, which in turn contracted the execution of the work to “ARGE BBI GU II – Luftseitige Flächenbauwerke” (ARGE BBI GU II – Airside Traffic Infrastructure), a joint venture comprised of Eurovia VBU, Max Bögl Bauunternehmung and Eurovia Beton. The companies already owned large Wirtgen slipform pavers type SP 1500, SP 1500 L and SP 1600. These machines have been in non-stop operation since May 2008, paving concrete on the extensive areas day after day and night after night. At the same time, two slipform pavers type SP 500 are in operation to complete smaller areas and are additionally working in those places where specifications require exceptionally steep slopes.
A strong team: in the “BBI GU II – Luftseitige Flächenbauwerke” joint venture, contractors Max Bögl and Eurovia Beton provided one paving gang each for each of the Wirtgen paving trains. Handover took place on the fly after each 12-hour shift.
6,000 cubic metres of concrete in a single day
“It’s a truly impressive experience to collaborate on such a large-scale project, and an opportunity you don’t get often in life,” says senior site engineer Christoph Hofmeister (Max Bögl). “We will be placing some 600,000 cubic metres of pavement concrete altogether over the entire project term. If everything goes smoothly, a large Wirtgen paver is capable of processing 6,000 cubic metres of concrete within 24 hours,” Hofmeister continues, illustrating the project’s huge dimensions. Such tremendous daily output rates require accurate planning and smooth, highly efficient teamwork. Not an easy task in a large-scale project, for up to 350 employees of the “BBI GU II – Luftseitige Flächenbauwerke“ joint venture are working on the construction site every day in peak periods. Some 90 of them are directly involved in the concrete paving operation: in addition to the paving gangs comprising some 15 workers per paving train, these also include staff, for example, for installing and removing the vertical formwork, cutting joints or supplying dowel bars, as well as the personnel in charge of planning and quality control.
The Wirtgen slipform pavers owned by the “BBI GU II – Luftseitige Flächenbauwerke” joint venture are in operation around the clock. Working at an advance speed of just over 1 m/min, they are placing the 40 cm thick, dual-layer pavement of extremely stiff concrete with utmost precision.
Pavement structure has an overall thickness of 130 cm
The new southern runway encompasses an area of 240,000 square metres, impressing with a length of 4,000 m and a width of 60 m. To enable even giant aircraft like the A 380 to land and take off at BBI Airport, a 130 cm thick pavement structure in concrete design was realized both on the southern runway and in all of the other movement areas. In a first step, the 50 cm thick bottom layer, which contained both non-cohesive and cohesive soil, was specifically improved and stabilized by means of cement. The next, 15 cm thick layer is composed of a stabilized mixture of hydrophobic cement and frost-proof sand. The contracting companies relied on Wirtgen technologies also for the completion of these operations: the job was carried out by several WR 2500 S soil stabilizers.
This is followed by a 25 cm thick hydraulically bound base layer. In a final step, the slipform pavers placed a 40 cm thick concrete layer between vertical formwork with sinusoidal cross-section. Planning and realization specified a non-reinforced concrete design with longitudinal and transverse joints. Dowel bars were inserted at regular intervals of 25 cm at the transverse contraction joints, while tie bars were inserted in the peripheral areas of the longitudinal contraction and longitudinal compression joints. In the vicinity of fixtures, such as manholes or foundations, the dowel bars and tie bars were placed on cages. In tapered junctions, in the vicinity of fixtures and in case of geometrically unfavourable slab dimensions, reinforcements were additionally inserted outside the predetermined breaking points to avoid cracking.
High-performance concrete for BBI Airport
Materials and processes needed to meet extremely high quality standards. “We use an air-entrained crushed aggregate concrete of compressive strength class C35/45 that is capable of taking extremely high loads. This material is able to withstand the tremendous mechanical loads imposed by the big aircraft just as easily as the high temperatures generated during landing or the application of de-icing agents in winter,” says graduate engineer Patrick Stryj from becker bau bornhöved (bbb), explaining the choice of material. He is in charge of Europe’s most modern concrete mixing plant in the immediate vicinity of the construction site. In up to six high-performance concrete plants, which are in operation around the clock, up to 11,000 cubic metres of concrete per day can be produced for both pavement and building construction. Cement, sand and aggregate are supplied by rail in order to ease the strain on both the road network and the environment.
Planning right down to the smallest detail
The large-scale project requires a significant degree of logistics and planning. The raw materials needed for concrete production are ordered on the basis of monthly and weekly requirements planning. The specified quality of concrete is then produced and supplied to the paver based on detailed day-to-day planning and current weather forecasts. Up to 50 trucks are available for the job. A quality assurance plan ensures the specified concrete quality by means of several accompanying material tests. These tests include, for example, temperature, water-cement ratio, degree of compaction and air content. Additional tests are performed once the concrete has been placed, such as flexural strength and compressive strength tests.
Logistics is one of the great challenges in the construction of the new BBI Airport: as many as 50 trucks are required for concrete transport from the nearby mixing plant to the paving site.
Five slipform pavers complete 1.5 million square metres
The paving gangs working at the slipform pavers are responsible for the paving quality. “We process fairly stiff concrete, and the paving operation is greatly facilitated by the high weight of the Wirtgen machines and their excellent compaction performance,” say paving managers Michael Lakotta and Hero Sauer.
At times as many as three large slipform pavers – an SP 1500 L, an SP 1500 and an SP 1600 – are in operation on the runways and taxiways at the same time. They are paving the concrete in a single-course, dual-layer operation, which means that one and the same type of concrete is used for both concrete layers (33 cm bottom layer and 7 cm top layer). Between the two layers, the dowel bars are positioned at evenly spaced intervals by the automatic dowel bar inserter (DBI). Evenness is ensured by a finishing beam and super smoother. Two texture curing machines type TCM 1800 follow behind the pavers, applying the broom finish as well as a liquid curing agent. Depending on weather conditions, these two operational steps are performed separately by two separate machines, enabling the optimal time to be chosen for each of the steps.
Applying the broom finish right after completion of the paving operation gives the concrete pavement a defined surface texture, thus ensuring the specified tyre adhesion levels.
Having a peak-to-valley depth of more than 1 mm, the concrete pavement offers good tyre adhesion. Premature drying of the concrete is prevented by applying a layer of approx. 220 g of curing agent per square metre. Constant wind and the high peak-to-valley depth require such a large amount of curing agent to be applied to reliably prevent the formation of cracks.
Flexible machine design
Repositioning and conversion of the pavers are major aspects having an influence on the efficiency of such a large-scale construction project. During repositioning manoeuvres, it was in particular the SP 1500 with its two-track design that impressed with easy handling. The concrete pavement in the different sections was laid down in courses of different widths. This required the machines to be converted several times to working widths ranging from 12.50 m to 15 m. The job was carried out by the site teams in order to save the time and costs otherwise incurred for machine transport. It is precisely at this point that the pavers’ modular design and different module widths offer maximum flexibility to the contractors.
Perfect surface evenness
The concrete was paved between vertical formwork with sinusoidal cross-section, which enabled full compliance with the extremely high demands placed on the longitudinal compression joints. To produce the correct level and slope, the experienced airport builders used transducers scanning a stringline or slab tracers scanning the previously paved concrete slab. This enabled them to comply with the evenness requirements specified in the ZTV Beton (Additional technical contract conditions and guidelines for the construction of roadways surfacings made of concrete), and to produce the specified cross slope of 0.7% to 1.5%, as was confirmed by repeated measurements with a rolling straight edge.
Reliability counts
Machine reliability is of the essence in view of 24-hour operation, firm orders for specific quantities of concrete and extremely tight deadlines. That is why the joint venture partners rely on Wirtgen machines. Fast expert service was yet another aspect that scored top marks in Berlin. “Cooperation with Wirtgen’s subsidiary in Windhagen is excellent. There is no doubt about that in view of up to 2,000 machine hours per paver per year,” says graduate engineer Hakon Schalk, head of the Mechanical Engineer’s Department at Eurovia VBU. Frank Zimmermann, senior site engineer at Eurovia Beton, adds: “We achieve such high daily output rates because the majority of checks as well as maintenance and repair work can be performed right here on the construction site. To complete these jobs, we use the time frame that is available when the machines are cleaned at the end of the night shift. Our well-trained staff handle many things themselves, and Wirtgen has always provided perfect support with any other work that needed to be performed at the machines.”
On-site service: highly qualified Wirtgen service technicians accompany the project and support the teams on site as required.
Expertise is the key efficiency driver
“Yet another building block that is vital in ensuring the successful completion of such a project is training staff in small groups,” says senior site engineer Frank Zimmermann, explaining the philosophy of his company. Martin Datzert, service technician and slipform paver expert at the Wirtgen Windhagen subsidiary, has trained the team in intensive courses during the long winter months: “The operators were familiar with their machines even before the training began. The training classes enabled us to deepen their knowledge further.” He places special emphasis on regular, independent machine checks and quick troubleshooting, which enables worn parts to be replaced in good time even before any extensive repair stoppages become necessary. This enables the teams to ensure high machine availability and rapid progress of the construction operation.