Low-temperature asphalt
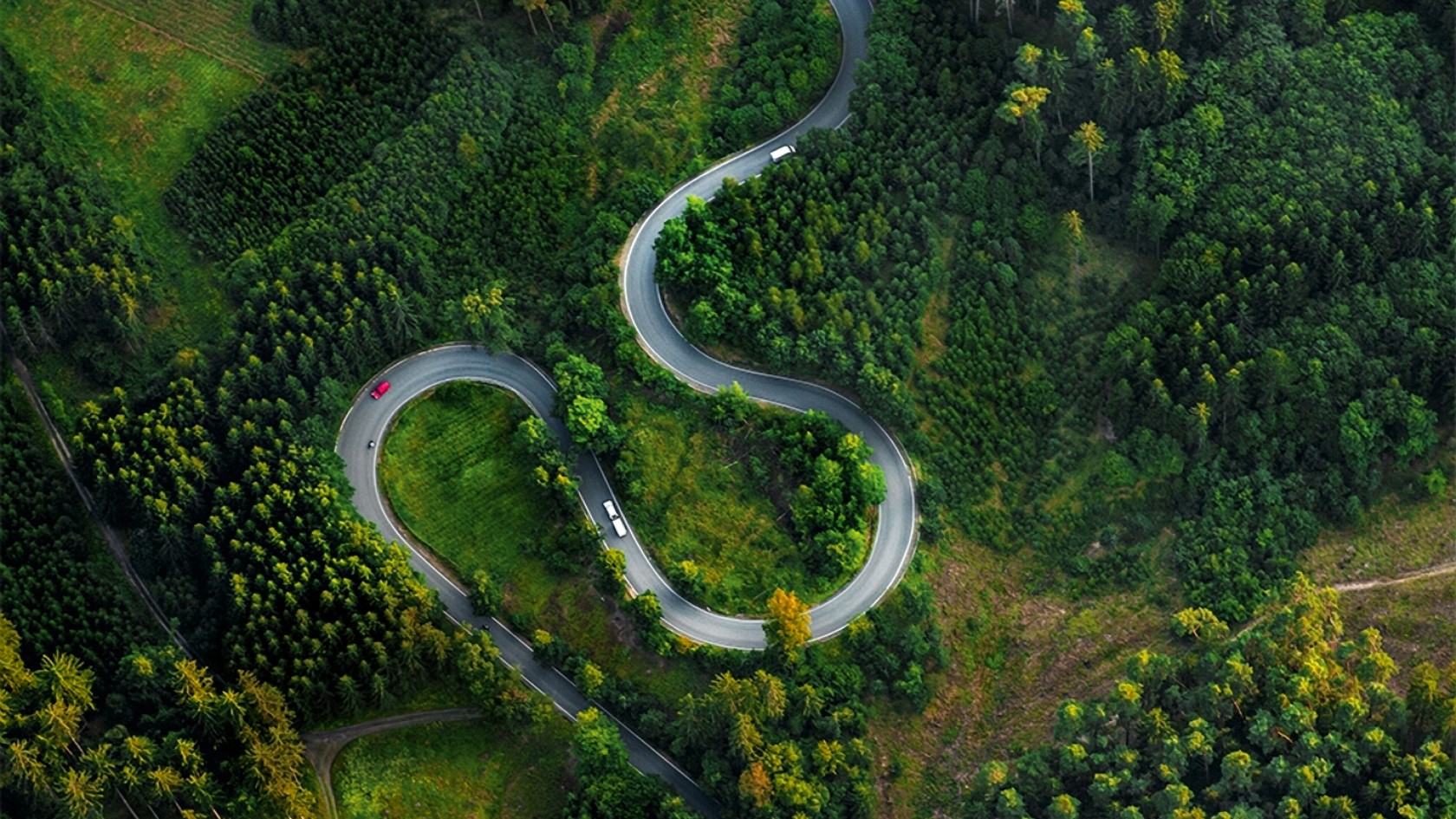
Low-temperature asphalt is asphalt that is produced and processed at a lower temperature without any negative impact.
The crucial difference compared to conventional hot asphalt is the processing and laying temperature. In figures, this is a temperature reduction of 20 – 40 °C. The accompanying effect in production and application include the improved energy balance and the reduced emissions during production as well as the lower workplace exposure during laying of the asphalt.
* Deutscher Asphaltverband e.V., asphalt Leitfaden, Temperaturabgesenkte Asphalte [Asphalt guide, low-temperature asphalts – published by the German Asphalt Association]
Low-temperature asphalt
The desired temperature reduction during asphalt production is achieved by temporarily reducing the bitumen viscosity, which can be obtained by adding water or additives.
A temperature of at least approx. 140 °C is required for the bitumen (binder) to wet/coat the mineral. At lower temperatures, its viscosity is too high. The flowability, i.e. the viscosity, also depends on the bitumen type and can therefore vary greatly between the different bitumen types. Viscosity depends on temperature and type, i.e. hard bitumen has a higher viscosity than soft bitumen at the same temperature. Common temperatures are between 140 °C and 180 °C and the typical temperature is around 150 °C to 160°C.
A sufficiently low binder viscosity requires good wetting and coating of the aggregates in the mixer. In addition, the elasticity of the asphaltic mixture play an important role for laying and compactability during laying of the asphalt.
Low viscosity of bitumen can be achieved by the technology on the one handFoam bitumenand by usingadditives on theother hand.
By mixing hot bitumen with water in the foam bitumen module, the bitumen is foamed to many times ofits original volume. This means that a large surface not only lowers the viscosity, but also improves the wettability of the aggregate material.
For the technical implementation, the weighing and mixing section simply has to be expanded with the FOAM BITUMEN MODULE which is additionally flanged onto the mixer cabinet and the bitumen weigh hopper.
Uncomplicated connection using PLUG & WORK ensures fast installation and commissioning.
In order to add smaller amounts of solid additives, BENNINGHOVEN offers the technical solution of the powder/granulate feed system. Depending on the material and added quantities, additives can be dosed into the mixer with a stream of air. The multi-variable feed is another option. This patented technology features precise dosing (exact weighing system) and allows larger additive quantities to be added to the mixer. The materials are fed with an elevator or inclined conveyor.
With the adhesive system, up to two liquid additives can be added to the process. The system is equipped with two conveying pumps which dose the liquid additives into the bitumen weigh hopper and/or into the mixer. The system has a very good resistance to chemicals and high temperatures.
BENNINGHOVEN is your reliable partner for this as well. Whether with the FOAM BITUMEN MODULE technology or by adding various additives with feed systems – we have the answer to your individual requirements. With Plug & Work, the system can be quickly retrofitted to any plant at any time.
Working more efficiently with sustainable and economical technologies is the challenge of today and tomorrow. Benninghoven offers a variety of innovative solutions for increasing sustainability in asphalt production.
Learn moreAsphalt production, recycling systems, combustion technology, control systems and bitumen technology – with BENNINGHOVEN technologies, every customer can find the right solution for their location, according to the specific requirements and conditions.
To the technologies