Hot Recycling
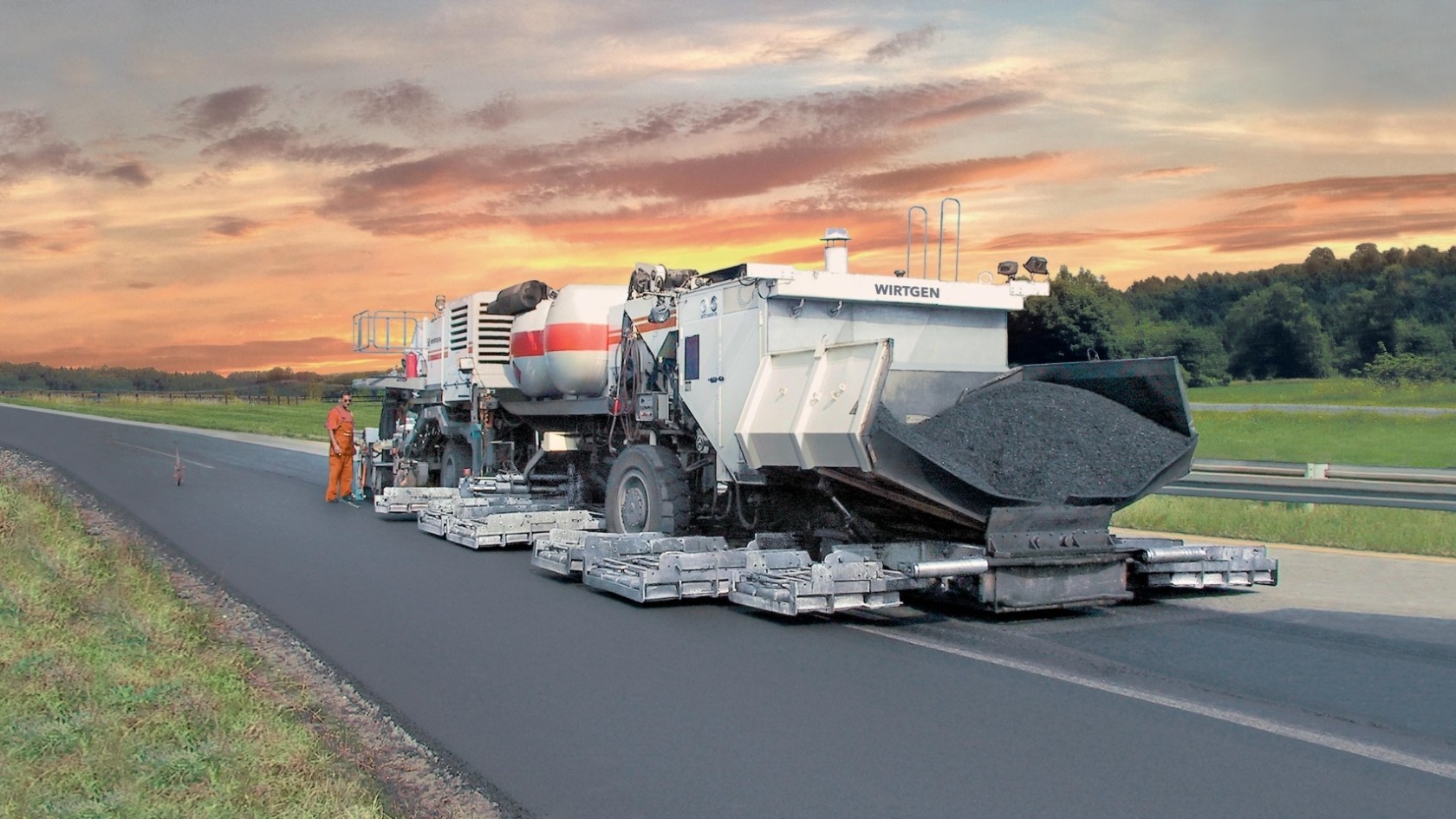
The hot recycling method is used solely for the rehabilitation of damaged asphalt surface layers, which is why an intact layer structure is extremely important. The pavement structure below the surface layer must fully meet all the requirements in terms of bearing capacity and frost resistance.
The hot recycler prepares the existing road pavement, including adding fresh mix, if necessary. After completing the process, the new surface layer will once again fully meet all of the requirements.
Hot recycling improves all relevant properties of both the surface and the pavement profile, as well as the composition of the aggregate fractions in the surface layer. It can restore a lack of grip, ensure that water drains properly, and remove ruts. Hot recycling offers tremendous savings potential. Compared to replacing the pavement with a milling machine and road paver, the hot recycling process can eliminate around 85% of all truck trips and around 70% of the new mix that would be required.
Variable paving of surface layer up to 4.5 m working width
The surface course is heated up to 150 °C / 302 °F by a panel heating machine with gas-fired infrared heating panels so that the hot recycler can then scarify, remove, process and repave the softened asphalt. In this way, the road's non-skid properties can be restored, water can run off again and ruts are eliminated. The potential savings are enormous.
A lane five meters wide needs to be repaired over a length of about 5 km. This corresponds to an area of around 25,000 m². With a surface layer weight of 100 kg per m², the “conventional” method of replacing the surface layer requires around 200 truck trips – 100 to remove the milled material and 100 to transport new asphalt mix to the site. If the standard is adhered to in the hot recycling process, 30 kg of new mix is added per m². This means that only 30 truckloads of 25 tons each are required – 170 less than the conventional method.