Pavement Replacement
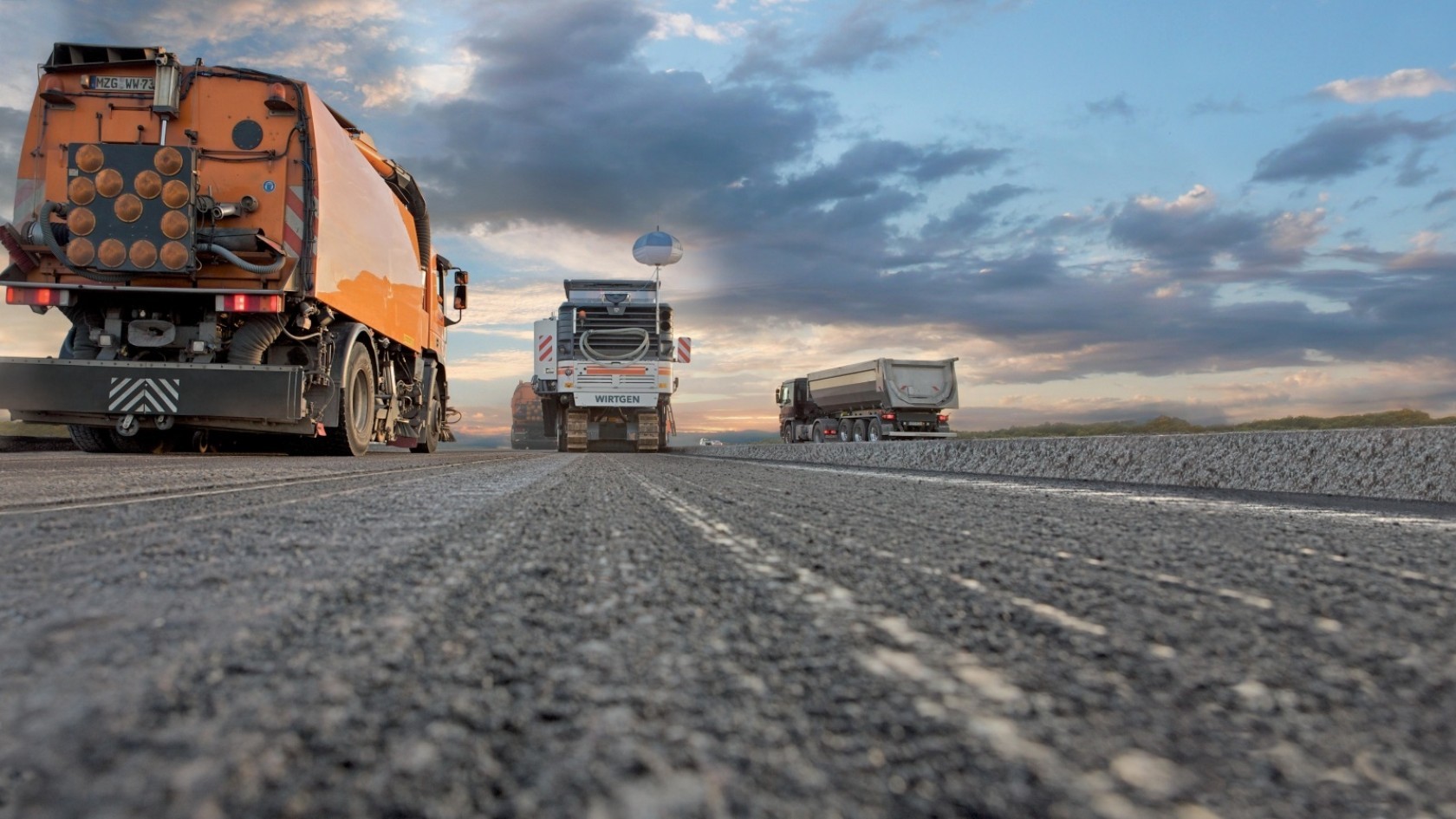
Pavement replacement is a standard road rehabilitation procedure. The challenge is to ensure that only the damaged layers of the road structure are removed – while simultaneously avoiding traffic disruptions. Under these conditions, cold milling is the only viable option for many construction projects.
The tools that cold milling machines use for removing road layers were originally developed for the mining industry. Point-attack cutting tools, also called picks, mounted to a rotating drum on the bottom of the machines drill their way into the road at exactly the required depth. No material is too hard for these picks – cold milling machines can even rehabilitate concrete roads. Regardless of whether asphalt or concrete, the material is milled and then directly loaded on trucks to be transported from the site, all in a single operation.
Because traffic often moves slowly through construction sites, many drivers mock the massive cold milling machines by saying they’re always the first vehicle in a traffic jam. However, few consider that in most cases, rehabilitation measures with cold milling machines are carried out as moving construction sites. The alternatives would be much more complex. Cold milling of roads is second to none in terms of both logistics and speed of construction.
Cold milling machines not only come in the size of an apartment, but can also be as small as a car. On many job sites, machines of different sizes work together as a team, leveraging their different strengths. The large milling machine removes the surface, while the “little guy” is responsible for milling off the pavement around “nuisances” like manhole covers and curbs.
Typical of rehabilitation projects using cold milling machines is that the removed layers are usually replaced with asphalt – irrespective of whether the damaged pavement was originally made of asphalt or concrete. This work is performed by road pavers. A road paver is capable of paving the new layers quickly and with outstanding quality. State-of-the-art automatic leveling systems make it possible to precisely adapt the height of the new surface layer to the existing pavement.
Rollers following directly behind the paver then carry out the final compaction of the new asphalt layer. When road pavers and rollers are busy at work on a job site, drivers also have reason to rejoice – this usually means that it won’t be long before traffic can flow freely once again.
HAMM following behind VÖGELE has proven to be a successful approach to surface layer rehabilitation and road construction in general.
In this interview, Bernd Holl, Product Manager Cold Milling Machines at WIRTGEN, explains why cold milling is so important when replacing the pavement.
To the Interview