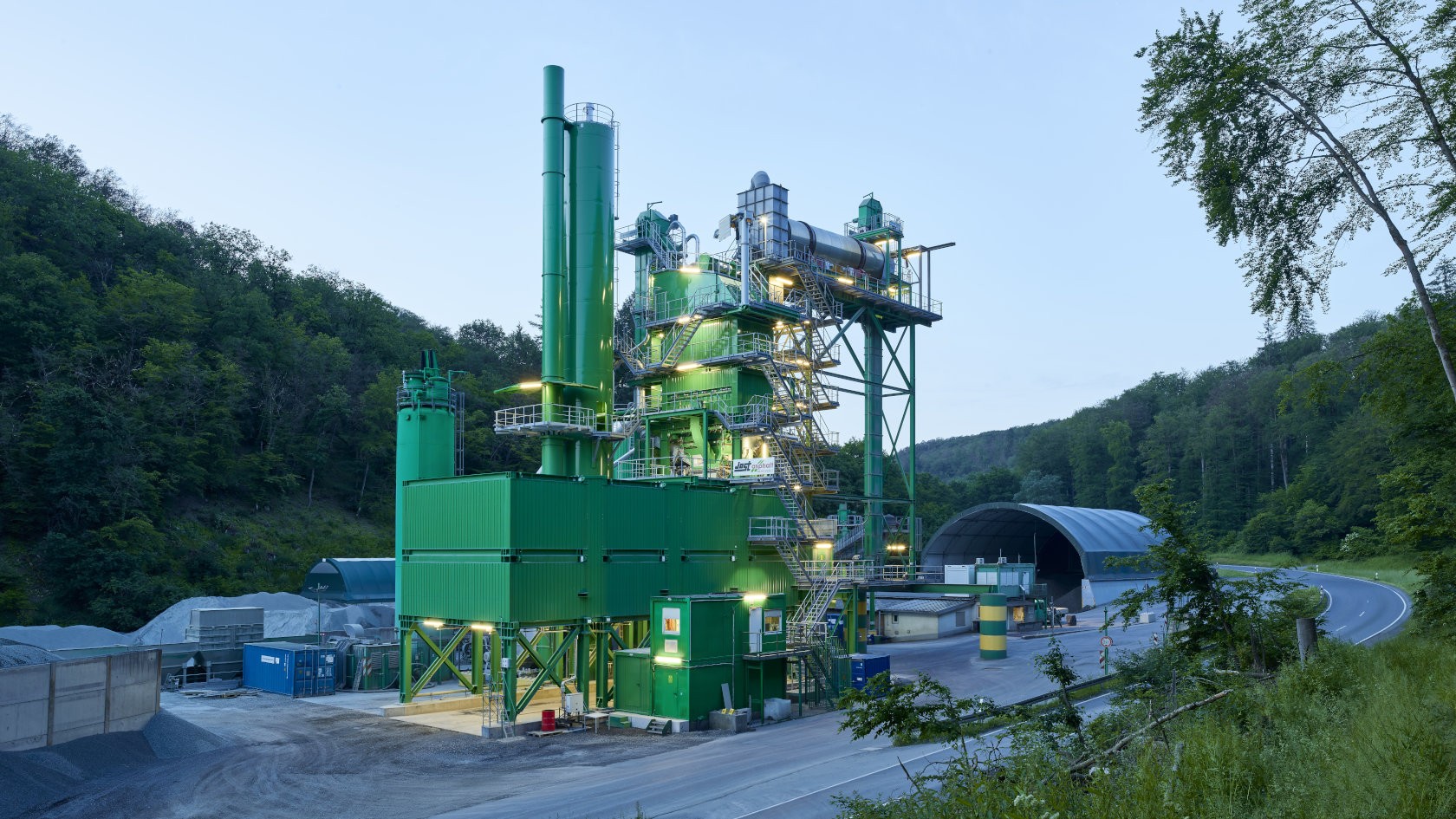
Braunfels (Taunus) | Germany
Retrofit solutions from Benninghoven can meet a variety of different requirements. A project in the German Taunus region demonstrated this very effectively: Two central sections of the plant had to be completely replaced in a small space and taking into consideration several fixed points. Specifically, these sections were the mixing tower and the drying section. The recycling plant and other components, on the other hand, had to be retained. This “open heart surgery” was a great challenge with respect to planning, logistics and installation, which an experienced team at Benninghoven rose to – in close coordination with the customer.
The demand for a higher production capacity of then 200 t/h was the starting situation with which the customer Wilhelm Jost GmbH & Co. KG approached Benninghoven. The existing mixing tower in particular had increasingly turned into a bottleneck. The road construction company from the Taunus region in Germany has undergone a successful development during the past 20 years. The in-house installation fleet lays 80 percent of the asphaltic mixture from the plant in Braunfels itself, while only a fifth is sold on.
Jost decided to work with Benninghoven despite the fact that the plant was originally purchased from a competitor. “We have had a business relationship for 15 years, though. It started with the retrofitting of an EVO JET burner,” says Managing Director Bernd Jost. “This burner has been running perfectly ever since. The good reputation of Benninghoven has been confirmed in our case. The collaboration never disappointed.” The list of jointly completed projects also includes retrofitted bitumen tanks, the integration of the cold and hot recycling feed systems and the replacement of the plant control with a Benninghoven BLS 3000. “That is why we were very confident that our partner would meet our expectations for this project as well,” explains Bernd Jost.
“The good reputation of Benninghoven has been confirmed in our case. The collaboration has never disappointed.”
Bernd Jost, Managing Director of Wilhelm Jost GmbH & Co. KG
Old components, intelligently integrated: View of the refurbished mixing plant at Wilhelm Jost GmbH & Co. KG in Braunfels (Germany).
It became clear during the first meetings at Jost that the drying section would have to be replaced in addition to the mixing tower to ensure that the production capacity could be increased. The old hot bin section for storing heated virgin mineral only had a capacity of 80 t. With the new Benninghoven equipment based on the TBA 4000, this has now increased to 130 t in seven bins, while the screen has a capacity of 290 t/h. The capacity of the loading silo at Jost was doubled to 440 t. Up to eight different mixture types can be stored, with two of the chambers even suitable for extended storage periods. This increases the delivery flexibility.
The new mixing tower was also selected from the TBA 4000 plant type. Thanks to a 4-t mixer, Jost will be able to produce up to 320 t/h of asphaltic mixture in a variety of different recipes – typical for Benninghoven plants. Thanks to the existing and retained Benninghoven hot feed system with parallel drum, a recycling content of up to 70 % can be achieved. With the cold recycling system for dosing into the mixer, this figure is still up to 30 %.
Image: Precision work – one of the greatest challenges for the Benninghoven installation team was the very restricted available space. The plant is located in a valley and directly next to a public road.
Choosing the new components was easy for Jost. This was supported by a visit from the plant team and the responsible managers to the main Benninghoven factory in Wittlich, where the team was able to see everything and have any open questions answered. The planning experts from the Benninghoven technical office offered competent advice.
The planning process, on the other hand, was much more complicated. As some of the existing components and sections of the plant had to be retained, numerous fixed points had to be taken into account, so that the engineers had to plan the new mixing tower and drying section around these areas. For this highly restricted installation space, Benninghoven also took on the structural stability calculations for the steel structure of the mixing plant and loading silo – including determining the support loads for the on-site concrete foundations and the required steel profiles.
The greatest obstacle, naturally, was the recycling plant with its parallel drum at a height of 30 m. But the integration of the other components, i.e. the cold feed unit, EVO JET burner, coal dust silo and bitumen tanks with piping, was also very complex – during planning as well as during installation. Retaining the control station with the control cabinet container and integrating an additional container presented additional challenges. The new component control cabinets for the mixing tower, loading silo, dryer drum and dust collection system were installed there. The frequency converter for the exhaustor and the dryer drum were placed in an additional control cabinet container.
“The recipe for the success of our retrofit division is to offer an all inclusive package – everything from planning to commissioning from a single source.”
Achim Keller, Benninghoven Sales
With a large and complex retrofit project like this, there is no guarantee for a completely smooth process. Unexpected things can always happen. Sometimes, things look differently at the construction site to what was intended at the planning office. Those situations require a talent for improvising and solution-based thinking. Still: “When it comes to large investments, it is particularly important to have a completely reliable partner,” says Kai Philipps, project manager at Jost.
Given the great complexity, the Benninghoven team more than earned the trust placed in them: “During winter, we started to remove the old components. The objective was to commission the new components within six months. And we almost managed that, with only a few days delay,” Christian Bode, project manager at Benninghoven, is happy to report. “The recipe for the success of our retrofit division is to offer an all inclusive package – from planning and disassembly to installation and commissioning, customers receive everything from a single source. The project in Braunfels demonstrated impressively what a well-coordinated team we now are.
Frithjof Löhr, mixing foreman at Jost, agrees: “As with any other large project, there are moments where things get a bit sticky and you panic for a moment. But overall, the boys from Benninghoven team did a great job.” When all commissioning tests were completed, the moment had finally arrived: The first asphalt trucks from Wilhelm Jost GmbH & Co. KG set out to the construction site.
Image: Transfer of the asphaltic mixture – the commissioning of the refurbished asphalt mixing plant has been successfully completed.
“When it comes to large investments, it is particularly important to have a completely reliable partner.”
Bernd Jost, Managing Director of Wilhelm Jost GmbH & Co. KG