Tool changing made easy
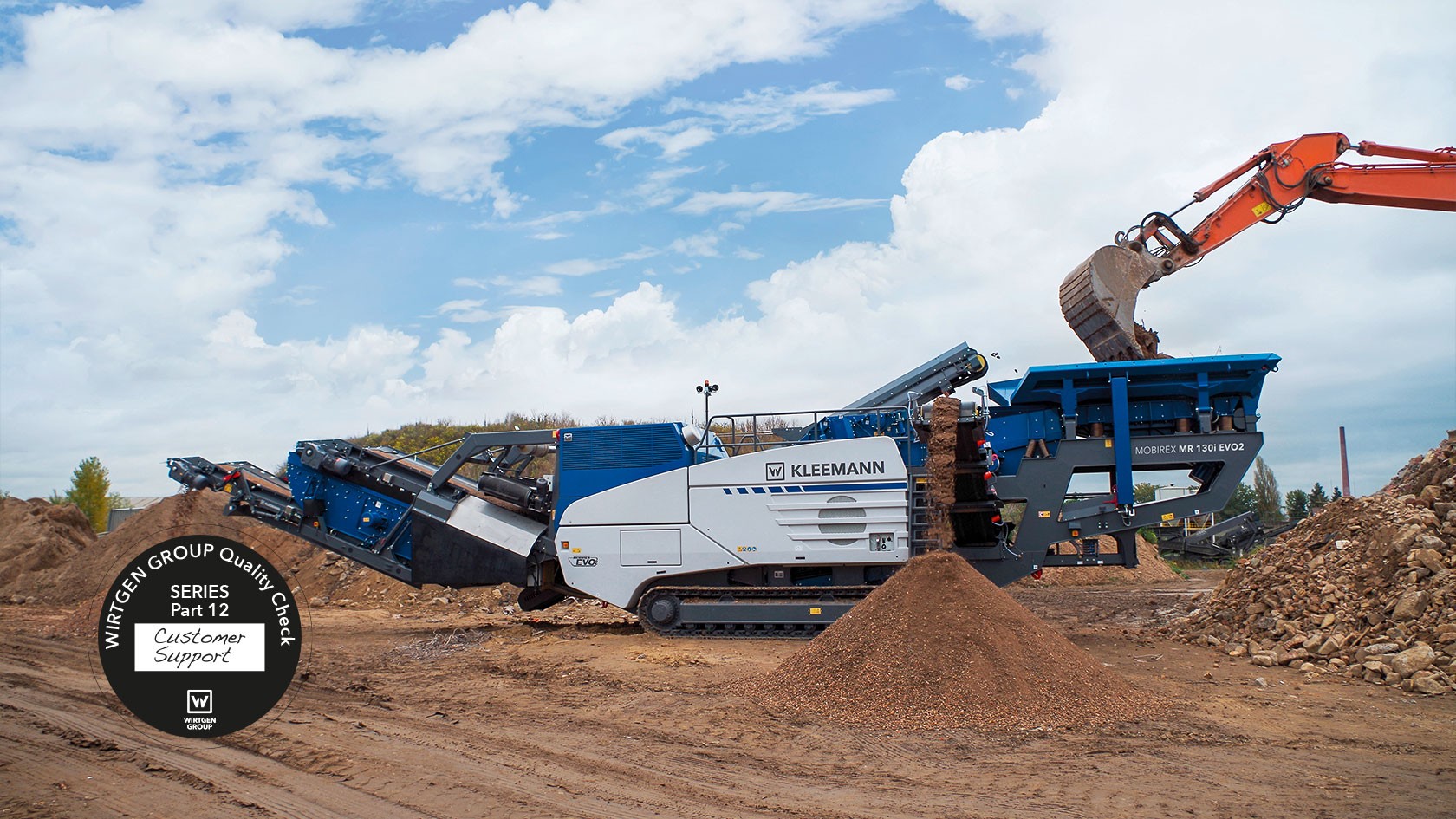
Kleemann Impact crushers: Convenient and safe replacement of rotor ledges and impact toggles.
The replacement of rotor ledges and impact toggles on the impact crushers in the MOBIREX EVO2 and PRO series is simple and safe. The uncomplicated handling shortens machine downtimes – which lowers the production costs and also significantly improves safety for users.
Rotor ledges and impact toggles are wear parts. They have to be replaced at regular intervals – depending on the feed material and machine operation time. Work with the solid components can be time-consuming, physically strenuous and quite dangerous. To organize these regularly recurring maintenance tasks more effectively and safely, in the last few years Kleemann has invested a lot in development work and the simplification of the tool change. The MOBIREX series today is characterized by clever safety features and easy and safe access to all components. Accessibility to the crushing chamber is facilitated via a clearly arranged digital support that raises the robust crushing chamber cover easily and safely.
Kleemann Impact crushers accomplish hard work in hard rock. Wear parts such as rotor ledges and impact toggles therefore have to be replaced regularly. The MOBIREX series scores in this regard with clever safety features.
Detailed video instructions on the tool change of a MR EVO2 can be found in our Web Special.
To the Web SpecialUse the wheel loader to pull on the sides of the stuck rotor ledge until it detaches or the rotor ledges ‘burn out’ – this used to be a common, but dangerous and damage-prone undertaking. Thanks to a special clamping system, rotor ledge replacement on the MOBIREX plants is considerably less complicated and faster: Release the wedges and remove the rotor ledges upward via the trailer cross member using the power of the excavator or a wheel loader Users stand safely on wide platforms. Further huge safety benefit: Per Lock &Turn, the rotor is firmly locked – serious accidents due to unintended movement of the rotor are thus a thing of the past.
Depending on the plant type, rotors with three or four rotor ledges are used. Rotors with four rotor ledges are mainly operated with two high and two low rotor ledges. Usually only the two high rotor ledges have to be changed. The low rotor ledge is then changed shortly before it reaches the height of the rotor. This work on the MOBIREX plants only takes one and a half to two hours - a real cost and time advantage.