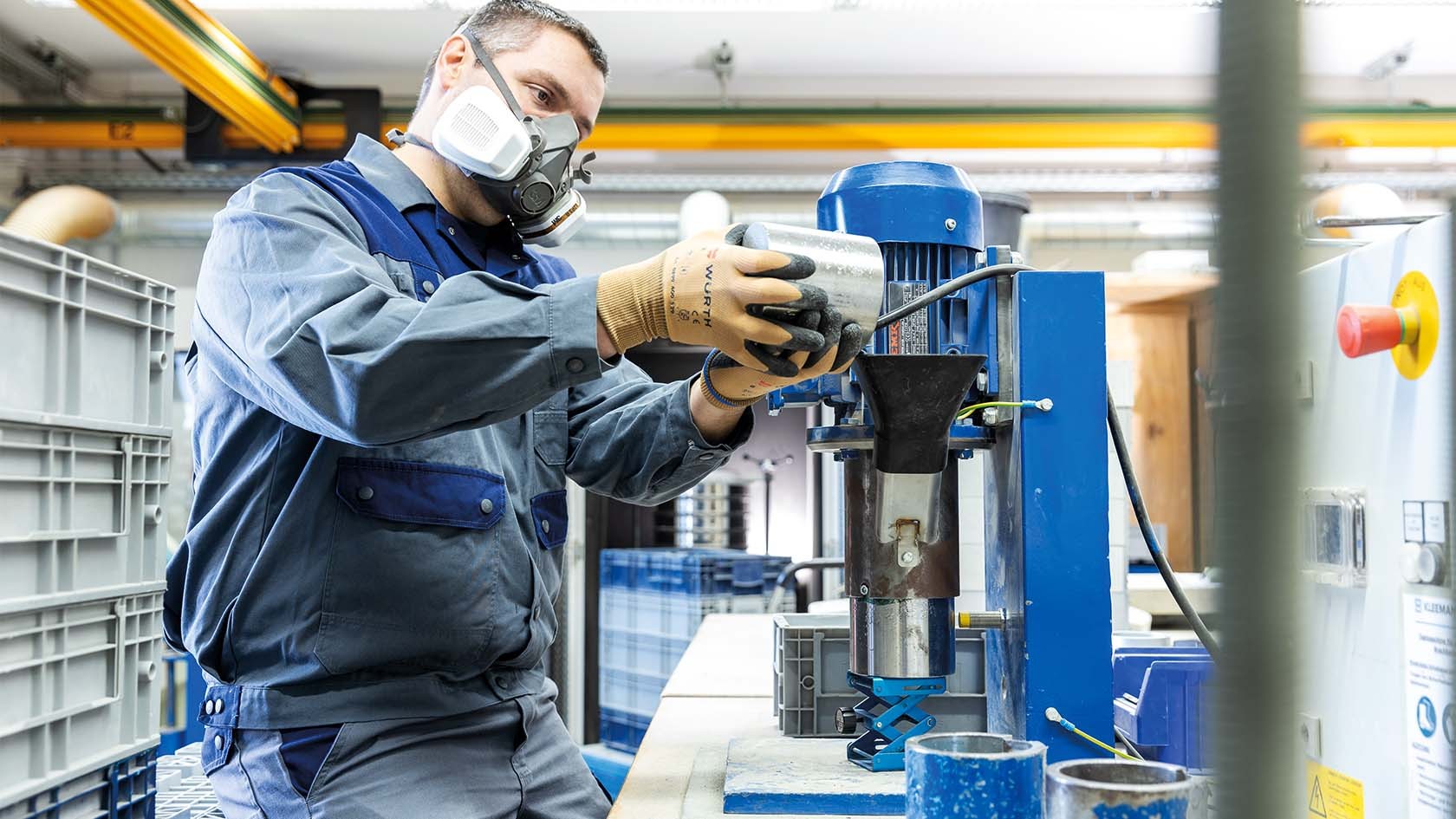
Stone on the test bench
No stone is like any other. Kleemann Application Technology knows this from many years of experience. To provide reliable valid values for plant planning, stones are subject to a stringent examination in the laboratory. Different test methods are used here.
Pipettes, test tubes and lab coats? You won't find any of this in the in-house Kleemann laboratory. The testing room contains a collection of large and small stones of all types, it is dusty and staff roll up their sleeves and get on with it. The laboratory employee Anatolij Schlegel routinely drops defined weights from a defined height onto defined pieces of rock, operates the screen machine, a small laboratory crusher or the drum of the LA test.
How does a stone behave?
What material properties does the stone demonstrate, does it react to pressure differently than to a shock load, how abrasive is it and what grain size distribution results? All these questions can be answered based on the laboratory test results.
For the team in Application and Process Engineering, this is decisive information for project planning: "For many of our customers, it is important that their product meets a particular specification. In most cases, standards have to be observed, for example, for different concrete qualities. This is why our aim is a detailed analysis with different test procedures."
Frank Lebender (left) and Anatolij Schlegel (right) examining different materials.
Different tests are often required in order to test all material properties. The ideal test allows meaningful statements to be made with low material usage.
A good example of this is the LCPC test: In a cylinder filled with stone, a solid metal plate rotates at a high speed. The result is revealing in two respects. On the one hand, it demonstrates how the stone breaks and, on the other hand, the testers analyze the rotating test metal: How much material is lost? How much abrasiveness can be expected? "This test is really our standard test", explains Frank Lebender.
"For many of our customers, it is important that their product meets a particular specification."
Frank Lebender, team member of Application and Process Engineering, Kleemann GmbH
However, other procedures are also available. For example, a resistance to impact test which provides information on the behavior of the material after a short-term, high load. How a stone reacts to slow but constant pressure is demonstrated by the pressure resistance test, which is carried out in cooperation with the University of Stuttgart.
All these tests allow inferences to be made about the machine that is later best suited for the processing of the stone. If the material is difficult to crush and abrasive, this supports the use of a combination of jaw and cone crusher. A wear forecast can also be made. This is an important parameter for customers because every change of the crushing tools costs time and money. Apart from the testing of material properties, the laboratory also offers the option of preparing a so-called grain size curve.
The term "grain size curve" already describes the objective of the test: Different screens are stacked, from coarse to fine, in a laboratory screening plant and the sample material is filled. After an exactly defined screening duration, the tester removes the screen decks one after the other and weighs the oversize product of each individual deck. In this manner, the composition of the individual grain sizes of a stone sample can be determined exactly. This analysis is also important for many customers – for example, if sand production is planned and an analysis of how much sand already exists in the feed material has to be carried out. The test is also often used at Kleemann for internal further development, for example, when testing the behavior of prototype plants.