In stationary recycling operations, the preconditions for the use of an E-DRIVE drive are often very favorable. An adequate power supply is often available, occasionally even from an in-company photovoltaic system.
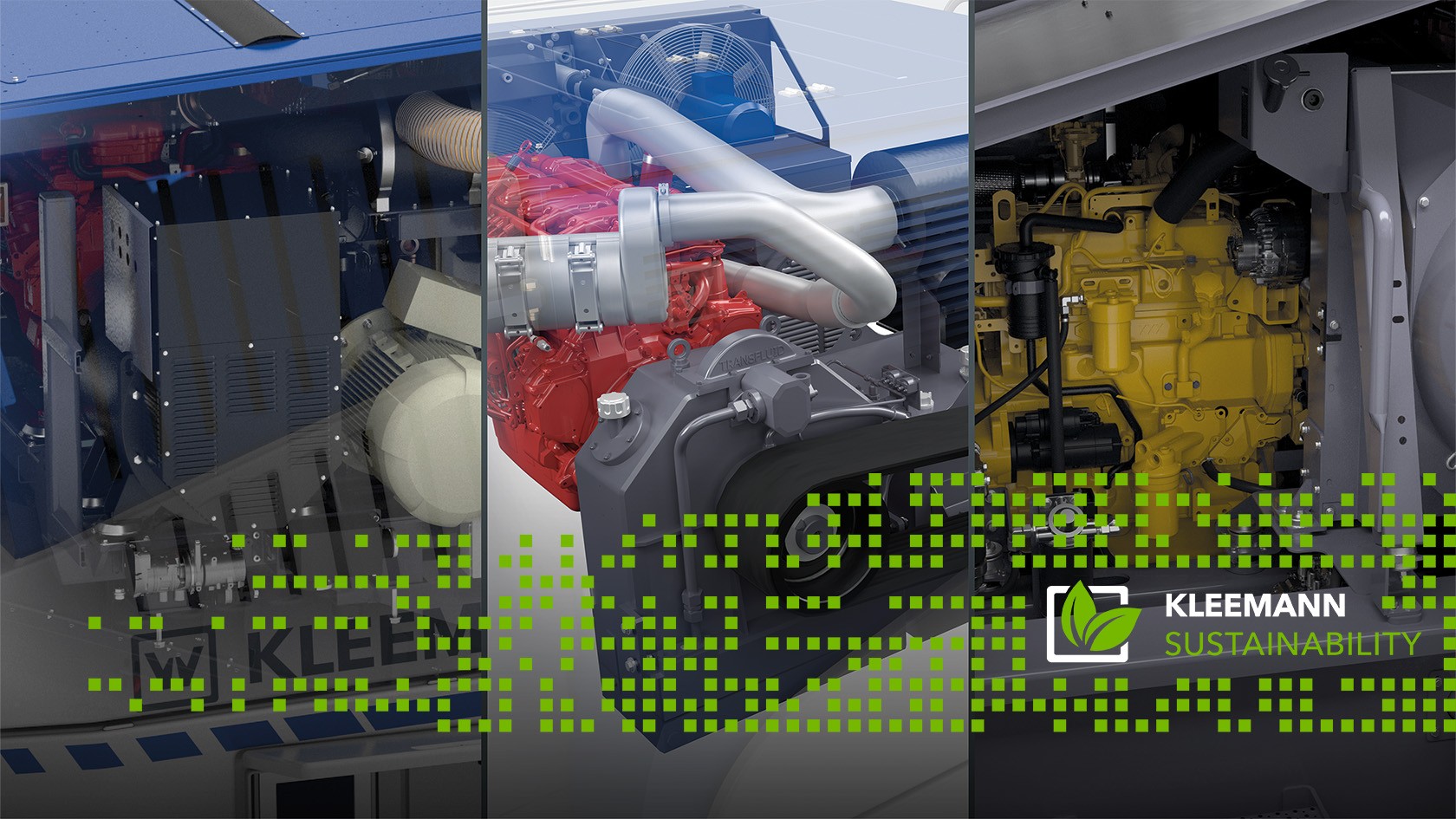
Three solutions and their application options
E-DRIVE, D-DRIVE and H-DRIVE – three drive concepts for different requirements and application options. The question as to which variant is the best possible solution where, when and for which tasks, always means weighing up efficiency, ecology and the on-site conditions. Kleemann demonstrates: The ecological footprint of a drive is ultimately always a question of the overall concept.
E-DRIVE, D-DRIVE and H-DRIVE represent the variants diesel-electric, diesel-direct and diesel-hydraulic. As far as the carbon footprint is concerned, electric drives score very well; in some situations, however, a fuel-saving direct drive is definitely the better choice. The decision as to which drive offers the more efficient solution must therefore always be made depending on the situation. For example, whether there is a power supply option available on site, whether the machines are used in an urban environment or which local environmental regulations apply.
Three drive concepts:
E-DRIVE, D-DRIVE, H-DRIVE – Kleemann Overview of crushing and screening plants and their drive concepts.
The E-DRIVE drive concept offers two options: Diesel fuel or all-electric. The all-electric drive is environmentally friendly, has no local carbon footprint but requires a power supply. If this is not available, or to an insufficient extent, the low-consumption diesel engine can be cut in. The crusher and all conveyor belts are still driven electrically by a generator.
The machine can be driven completely electrically or, alternatively, by the diesel engine. The crusher and all conveyor belts are then still driven electrically by a generator.
A = drive via diesel engine
B = drive via external power source
The use of E-DRIVE depends heavily on the local situation. Quarries and large recycling yards often have a good power infrastructure – crusher production here can be all-electric and thus environmentally friendly and CO₂-free on site. In addition, recycling plants increasingly generate more green energy via photovoltaic systems – if this is used to supply the drive, this results in a particularly well-balanced and sustainable overall concept.
Nevertheless, there are still situations where a power supply is not possible – for example, if the complete plant is moved in the quarry along the rock face and routing of long cables is too complex. In this case, the low-consumption diesel engine can step in and ensure that unnecessary machine downtimes are avoided.
In stationary recycling operations, the preconditions for the use of an E-DRIVE drive are often very favorable. An adequate power supply is often available, occasionally even from an in-company photovoltaic system.
If continuous use of the all-electric drive is not possible, the efficient diesel-directdrive D-DRIVE is the better and more sustainable choice. Thanks to the optimization of consumption in the last few years – for example, with the load-dependent fan drive of the new EVO2 generation – the D-DRIVE drive concept nowadays has a lower fuel consumption combined with a high crushing capacity. With regard to the degree of efficiency, the diesel-directdrive has energetic advantages and fuel consumption is up to 20 percent lower.
Crusher direct drive D-DRIVE: The fluid coupling guarantees high operational reliability – for operators and machine. All secondary drives, such as prescreen, chutes or conveyor belts, are driven electrically.
Many different applications require flexibility. For example, demolition and processing work in inner-city areas, but also in quarries when short-term peaks have to be dealt with, or when small overall volumes have to be crushed. In this case, the diesel-direct driven machines are quickly ready for operation and, thanks to their compact size and well thought-out transport options, can be positioned in any place on the work site. This advantage also applies to road construction where sites are not restricted to one location, but rather shift according to construction progress. Because a power supply is usually not possible here, the D-DRIVE offers a fuel-saving and efficient solution with a good eco-balance.
Demolition work in inner city areas is always a challenge. In many cases, an adequate power infrastructure is not available.
On the screening plants from Kleemann, hydraulic pumps operate all machine parts such as screen, belts and drive system. As the power requirements for screening are significantly lower than with a crusher, fuel consumption during operation is more manageable and can also be further reduced via the optionally available Start-Stop system: If there is a gap in the feed material, the machine reduces the engine speed and thus the speed of the hydraulic drives. If the wheel loader is required for a long period for other tasks, for example, loading of trucks, the plant switches off automatically.
The configuration with Dual Power makes an all-electric supply of the screening plant possible – provided that a mains connection is available. In this case, the plant operates on site completely emission-free – a particularly attractive option in ecologically sensitive areas with strict regulations.
The Kleemann screening plants use an effective diesel-hydraulic drive. Furthermore, the configuration with Dual Power provides an option for an all-electric power supply. If a mains connection is available, the plant operates on site free of emissions.
A = drive via diesel engine
B = drive via external power source
An ecological drive is always a question of the overall concept
Energy required for production, transport, storage, sales and disposal are all incorporated in the ecological footprint of the production process. An all-electric plant scores thanks to its on-site emission-free operation, although it does not necessarily need to be the first choice. If supply via an external power supply line is associated with high equipment and material costs, it is more constructive at the end of the day to use technology with lower fuel consumption. After all, ecology also means placing your trust in low material usage and high durability.
Which solution is the best, most efficient and sustainable is ultimately based on the concrete individual case. One thing is sure: Whether you decide on E-DRIVE, H-DRIVE or D-DRIVE – all three Kleemann drive concepts permit sustainable and environmentally friendly operation of the plant.