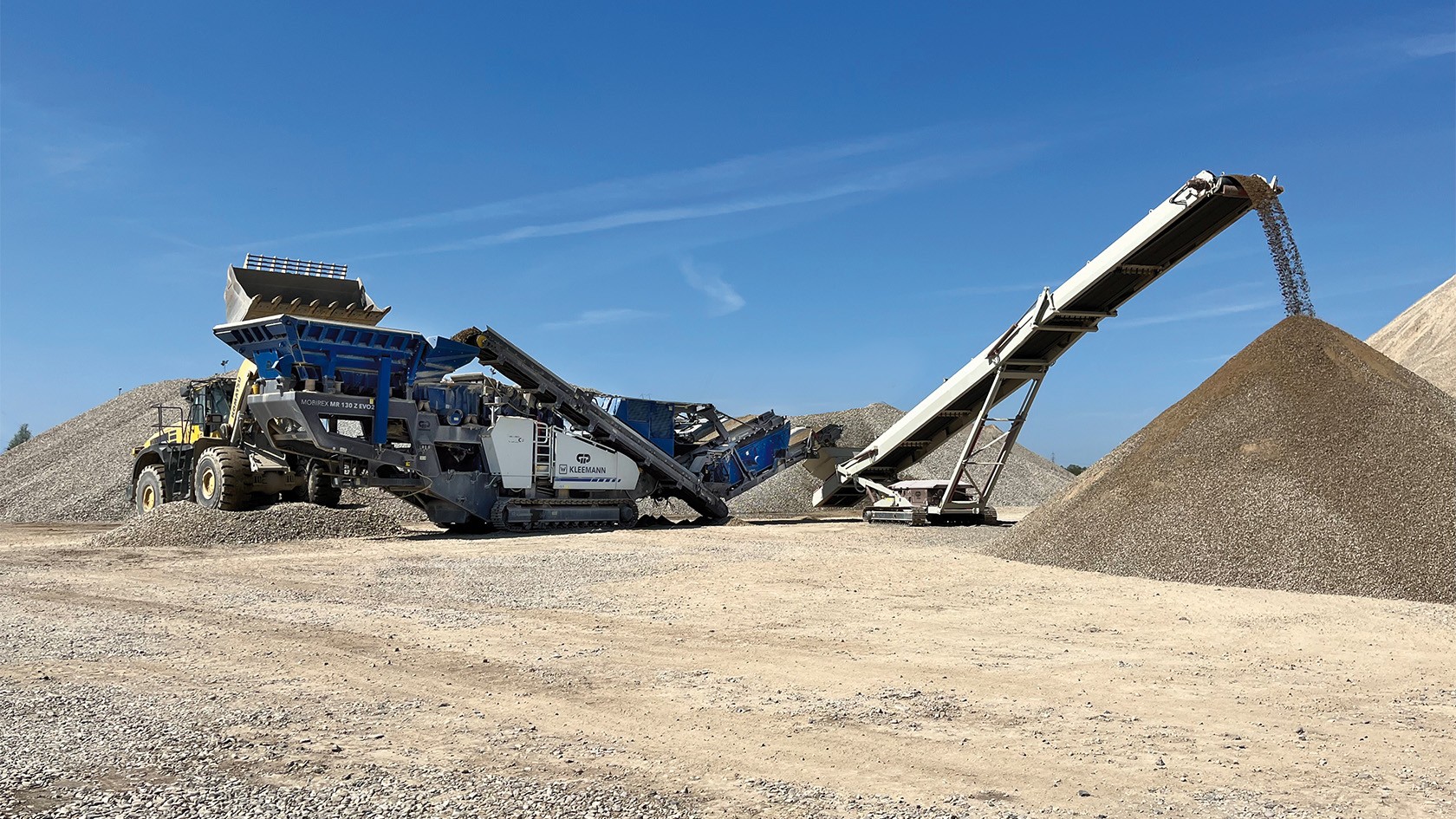
GP Günter Papenburg AG places its trust in Kleemann impact crushers in combination with the ZIP CLIP conveyor belts
High quality of the final product and high productivity of the processes has priority at GP Günter Papenburg AG. The wide range of natural stone, gravel, sand, earth and on to recycling products and dumping make particularly flexible and reliable machines necessary. In many areas, therefore, Papenburg places its trust in products from the Wirtgen Group. Six impact crushers from Kleemann are also in operation here – equipped with efficient ZIP CLIP conveyor belts.
In the area of recycling, Papenburg currently deploys the impact crusher MOBIREX MR 130 Z EVO2 at several sites. Its task: Processing of the recycling material, milled material and concrete to form a hydraulically bound base layer for road construction.
The MOBIREX EVO2 in operation. Papenburg appreciates the high quality of the final product and the trouble-free work with the machine.
"We have a remarkable output of 150 to 200 tons an hour. Work with the MOBIREX EVO2 is absolutely reliable and it can be deployed flexibly."
Marco Offenhausen, general manager at Papenburg
Marco Offenhausen, general manager at Papenburg, is impressed with the efficiency of the Kleemann impact crusher: "We have a remarkable output of 150 to 200 tons an hour. Work with the MOBIREX EVO2 is absolutely reliable and it can be deployed flexibly." The quality of the processed material is also impressive and the machine works very efficiently with regard to fuel and power consumption. A further positive feature is its mobility. If the plant is moved, it is ready for operation again in a very short time. From overload protection through modern safety elements and on to the intuitive control concept SPECTIVE. "In a whole range of areas, it's obvious that Kleemann's development work was tuned very closely to work in practice", says the general manager, "and this applies to each individual part". Good example: The ZIP CLIP conveyor belts, which make a belt change very simple.
Conveyor belts are essential components of crushing and screening plants, but they are also wear parts. Their quality is reflected directly in efficiency and operating costs. Another positive feature: The time required for assembly and disassembly of new conveyor belts because, depending on the system, this is more or less extensive. Standard systems usually have endless conveyor belts installed, which can be fitted in closed state on the belt conveyor. Disadvantage: They can only be changed on the work site with high time expenditure because the belt conveyor has to be disassembled.
This is where the open conveyor belts have an advantage: In case of damage or tears, they can be fitted on the plant directly on site. However, the belts are closed by means of vulcanization – work that has to be completed by an external service provider. The vulcanized area also requires a curing time of several hours, which results in machine downtime.
Easy to close but still absolutely firmly connected: The ZIP CLIP system impresses during conveyor belt replacement.
Papenburg, in contrast, places its trust in ZIP CLIP conveyor belts from Kleemann. Their mechanical connection functions according to the zipper principle, which provides many advantages. Users can thus replace the belt quickly on site and without assistance. And: Work can continue directly after assembly. Time-consuming removal of the belt unit as well as an external service provider and curing time are no longer required.
Find out more here on the subject of ZIP CLIP.
"Of course it's important to us that downtimes are kept to a minimum during a belt change. This system here is ideal. We can change the belt ourselves or, in case of a repair, we can open the belt and then continue to use it".
Marco Offenhausen, general manager at Papenburg
Andreas Konopka, operator of the MOBIREX impact crusher at Papenburg, and Bastian Hutecker, service and spare parts expert for Kleemann at Wirtgen Germany.
Andreas Konopka knows the situation: Conventional belt replacements are very complex and the machine has to be at a standstill. The short set-up times of the CLIP ZIP conveyor belts have convinced the operator.
Marco Offenhausen is convinced of the value of the ZIP CLIP system: "Of course it's important to us that downtimes are kept to a minimum during a belt change. This system here is ideal. We can change the belt ourselves or, in case of a repair, we can open the belt and then continue to use it". His colleague Andreas Konopka, who operates the MOBIREX EVO2 at Papenburg, confirms: "Replacement is quick and easy, it's over in around three hours. With an open belt, on the other hand, the machine is stationary for up to seven hours. And then two people have to come from an external service provider. We don't need that any more." For big projects that sometimes require double-shifts, Papenburg always has a ZIP CLIP conveyor belt in reserve. This allows to them to react quickly and avoid long downtimes and the associated financial loss.
Papenburg AG: Long-established company for over half a century
GP Günter Papenburg AGwith head office in Hanover is a family enterprise that has developed tremendously in the half-century of its existence: It has around 4,000 employeesin Germany and an expertise network of 58 subsidiariesand company sections. With its own gravel quarries and business premises, Papenburg offers a wide range of gravel and sand products, including clays and hard stone, but also different types of earth and subsoil. The spectrum also includes recycling products and dumping. It has its own haulage company, which means that all materials can also be delivered free to the customer's site.