PRO plant train impresses in granite
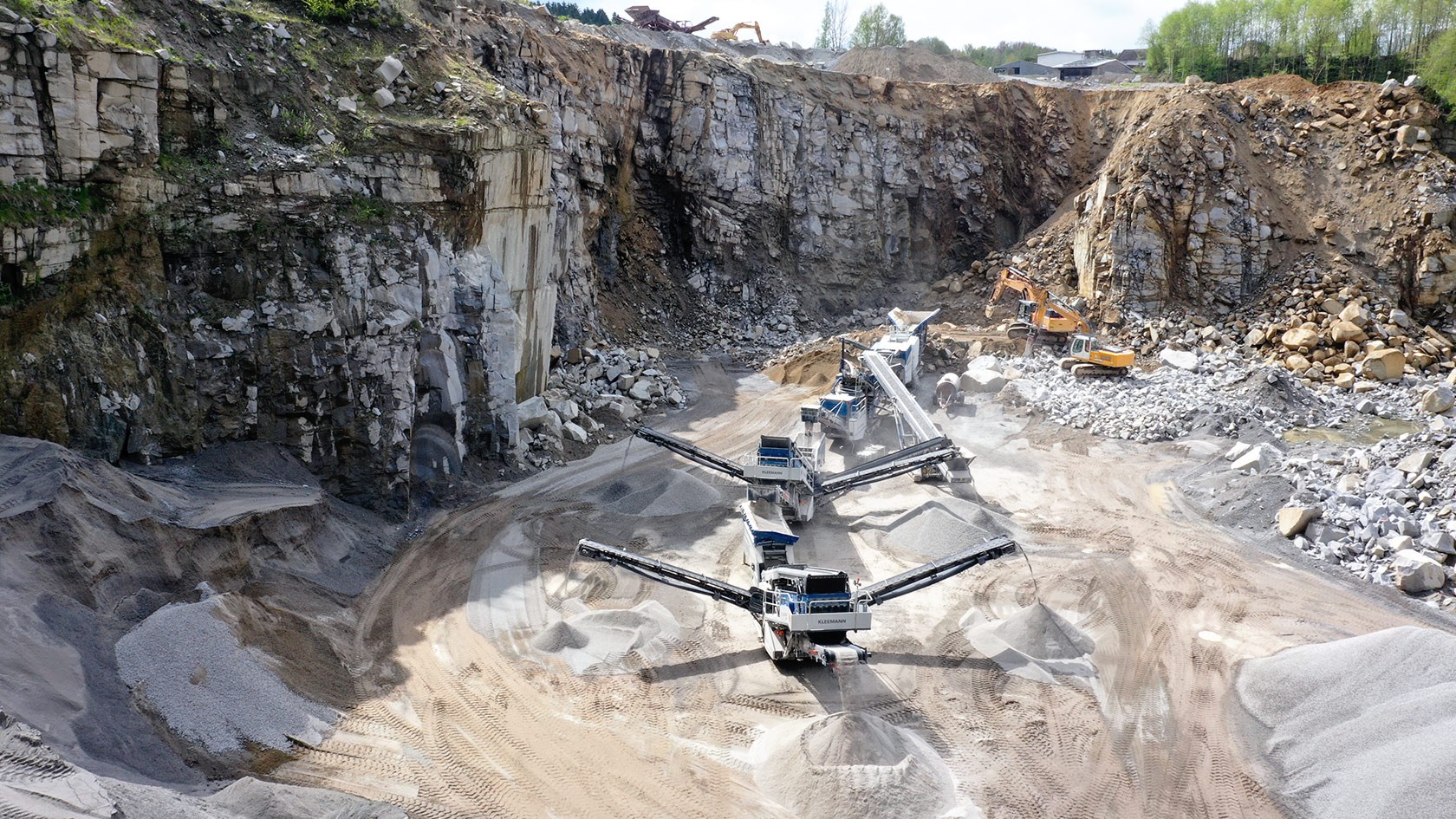
In Schlag, in the middle of the Bavarian Forest, Berger Rohstoffe GmbH took over a quarry in 2020. Since August 2020, a PRO plant train from Kleemann has been working there. The core of the plant comprises two PRO plants: The mobile jaw crusher MOBICAT MC 120 Zi PRO and the mobile cone crusher MOBICONE MCO 11i PRO. The mobile screening plants MOBISCREEN MS 952i and MS 953i EVO as well as the stacker MOBIBELT MBT 20 round off the plant train. Since then, the plant train has impressed with high productivity and economy and produces grit for high-quality concrete as well as mixed aggregates for anti-frost layers.
The quarry in Schlag was operated up to 2019 as a factory quarry. Since 2020, granite from the Bavarian Forest is crushed to broken stones and grit. In the framework of the conversion to a mass-scale quarry, Berger looked around for new crushing and screening plants. "In the neighboring Czech Republic, we have a site with similar requirements. A Kleemann plant train has been running there since 2019 with a constellation that is perfect for us", explains Markus Penz, who provides technical supervision of the plant as an engineer.
The conversion to a mass-scale quarry necessitated clearing work in many places. To prevent transport routes from becoming too long as extraction proceeded and to guarantee profitability, the new plant would definitely have to be mobile. Berger prepared the site such that the plant can be moved without any problems.
Feed material: Granite
Feed size: 0–400 mm
Final product: Grit (0–2 mm | 2–5 mm | 5–8 mm | 8–16 mm | 16–22 mm); anti-frost layer (0–32 mm | 0–56 mm)
Usage: Aggregate for concrete production
When selecting the plant technology, a decision was made again for a PRO plant train from Kleemann because this team met all the requirements with regard to suitability and output. A central element was the robustness of the crushers: "We see this as an advantage of the Kleemann plants because these crushers have a stable and solid design", says Markus Penz. Added to this is the certainty "that, through Kleemann and the Wirtgen Group, we can expect excellent technical support and parts supply. From the plants in the Czech Republic, we know that the maintenance concept is perfectly arranged and the plants can be operated cost-effectively."
Because granite is very abrasive, good wear protection on the plant was very important to Berger. The jaw crusher MC 120 Zi PRO has an independent double-deck prescreen that levels the material flow and guides the content of fines via the crusher bypass directly onto the crusher discharge conveyor. This relieves the load on the crusher, thus reducing wear. The jaw crusher is also equipped with a crusher discharge chute that protects the crusher discharge conveyor. The two MOBISCREEN EVO screening plants are equipped at the belt discharge or the transfer to the screen casing with several impact plates that distribute the material evenly on the screening surface and thus protect against wear.
Wide opening flaps and an intelligent arrangement of the relevant components reduce the complexity of the daily checks, maintenance and changing worn parts.
The team is also highly satisfied because the desired grit can be created from the loaded granite in only two crushing stages. In the precrushing stage, the grain shape is only altered to a slight degree; the second stage consists of crushing to the specified size. "Normally, this is almost impossible. For test purposes, before starting work we had material from the quarries tested in Kleemann's own laboratory. After fine-tuning of the plant train, we produce continuously to this high quality level", explains Andreas Wagner, Kleemann special consultant from Wirtgen Germany. Markus Penz is extremely satisfied with the result. "Approximately half of the material is transferred to our concrete mixing plants. Their requirements are stricter than the applicable standards. However, this plant allows us to easily meet all our target specifications because it is even better than we thought."
The team from Berger Bau (from left to right: David Göttlich, Manager of the quarry in Schlag, Markus Penz, plant engineer and plant operator/machinist Josef Dankesreiter) during the handover of the PRO plant by Andreas Wagner, Kleemann special consultant from Wirtgen Germany (right).
The complete plant train consists of five machines and operates as a line coupling. This means that automatic control stabilizes the complete process. Each machine basically operates independently but forwards signals to the upstream and downstream machines in the event of malfunctions or overfilling. The feed control Continuous Feed System (CFS) also guarantees optimum utilization of the crusher.
Ultimately, all components are loaded evenly. This is not a matter of course for Markus Penz because "here, we turn a natural product into a standardized product. The stone crushes differently and there are fluctuations: In the structure, due to the weather and the type of feeding. Output fluctuations are therefore normal. It is precisely these fluctuations that are balanced out by the optimized process thanks to line coupling in combination with the machine control system, the correct selection of machines and not least through qualified personnel."
This automated tuning relieves the burden on the operator and harmonizes the process. The connection of all machines also guarantees safety: If an emergency-stop button is pressed anywhere on the plant train, all machines are safely stopped. This concept prevents damage or overload situations. All of this combined results in a high availability and output with low wear.
To reduce the dust load, the MOBISCREEN screening plants are equipped with a belt cover and a water system on the fine grain discharger conveyor.
Berger ordered all components equipped with the external power supply option. This means, for example, that the screening plants can be driven either electro-hydraulically or diesel-hydraulically. At present, only the electric drive is used, for example, to operate the mobile screening plant MOBISCREEN MS 953i EVO using the current from the jaw crusher MC 120 Zi PRO. This reduces fuel requirements, emissions are reduced and operation is quieter. This is a benefit not only to staff but also to residents in the surrounding area and flora and fauna.
Kleemann plants with Dual Power have a module well along the path to sustainable stone extraction and processing. "We want to produce in an environmentally friendly manner. Fossil fuels no longer meet contemporary standards in the long-term. This is why we want to convert the complete structure of the quarry to electric drives in the long run", says Markus Penz. Berger Rohstoffe GmbH thus operates photovoltaic systems in many quarries.
The use of the locally generated current in all consumers on the site makes sustainable production of the mineral materials possible. The current balance of the regeneratively produced total power requirement is approx. 40% but this share is set to increase. "This is why we are already investigating scientifically how the mobile plants can be connected in the optimum manner to photovoltaic systems, also when changing work sites. The Dual Power function is promising at the moment, above all from the perspective of climate protection, and only to a small extent from an economic perspective. But some time in the near future operation with electric drives will be the more cost-effective alternative." The engineer is convinced of this.
Kleemann plants with Dual Power have a module well along the path to sustainable stone extraction and processing. "We want to produce in an environmentally friendly manner. Fossil fuels no longer meet contemporary standards in the long-term. This is why we want to convert the complete structure of the quarry to electric drives in the long run", says Markus Penz. Berger Rohstoffe GmbH thus operates photovoltaic systems in many quarries.
The use of the locally generated current in all consumers on the site makes sustainable production of the mineral materials possible. The current balance of the regeneratively produced total power requirement is approx. 40% but this share is set to increase. "This is why we are already investigating scientifically how the mobile plants can be connected in the optimum manner to photovoltaic systems, also when changing work sites. The Dual Power function is promising at the moment, above all from the perspective of climate protection, and only to a small extent from an economic perspective. But some time in the near future operation with electric drives will be the more cost-effective alternative." The engineer is convinced of this.
After delivery of the plant, the three-man core crew in Schlag also had to familiarize themselves with operation of the mobile crushing and screening plants. They found this really easy because the crushing plants are equipped, for example, with SPECTIVE. "The structure of the SPECTIVE operating system allows everybody to find their way intuitively. Everything is depicted with visual images and entry to deeper levels is also possible. Plant operation is therefore really easy even for colleagues who operate it only very rarely", says Markus Penz. Furthermore, he believes the clear user guidance also contributes to safety: "There's not a lot you can do wrong during operation because the machine does not permit possible wrong settings. This protection also allows operators to try out things within a practical framework and within the technical specifications - and that's a good thing."
After delivery of the plant, the three-man core crew in Schlag also had to familiarize themselves with operation of the mobile crushing and screening plants. They found this really easy because the crushing plants are equipped, for example, with SPECTIVE. "The structure of the SPECTIVE operating system allows everybody to find their way intuitively. Everything is depicted with visual images and entry to deeper levels is also possible. Plant operation is therefore really easy even for colleagues who operate it only very rarely", says Markus Penz. Furthermore, he believes the clear user guidance also contributes to safety: "There's not a lot you can do wrong during operation because the machine does not permit possible wrong settings. This protection also allows operators to try out things within a practical framework and within the technical specifications - and that's a good thing."
The SPECTIVE operating system from Kleemann displays all data as values, and also graphically. This makes operation easier.
After the first few months and experience in the Czech Republic, the team in Schlag also agrees: "The crushing and screening plants are very easily accessible. In a mobile plant, everything must be more compact and tightly fitted than in a stationary plant to make mobility possible. In spite of this, we can reach all areas without noteworthy disassembly work. Another plus point is that the instructions are also compact, but precise. Furthermore, work beyond the scope of the daily check is easy to complete because the machines are designed such that we can do a lot on our own."
And if we ever need a Service technician, the specialists from Wirtgen Group are easy to reach. "We have competent contact partners on every level: In sales, service and spare parts supply. We also appreciate the readiness to find solutions. We are already familiar with this good cooperation because we have other devices and products from the other brands in the Wirtgen Group. Ownership of this plant train from Kleemann means that here in Germany we now have products in our fleet from all brands in the Wirtgen Group."
Only our genuine spare parts ensure the ongoing reliability of your Wirtgen Group machines, plants, and systems. You can quickly and easily find the spare parts you need on our Parts Website.
Visit Our Parts Website