Plant train consisting of the jaw crushers MOBICAT MC 120i PRO and MC 110i EVO2, the cone crusher MOBICONE MCO 90i EVO2 and the screening plant MOBISCREEN MSC 953i EVO in the limited space available in the quarry.
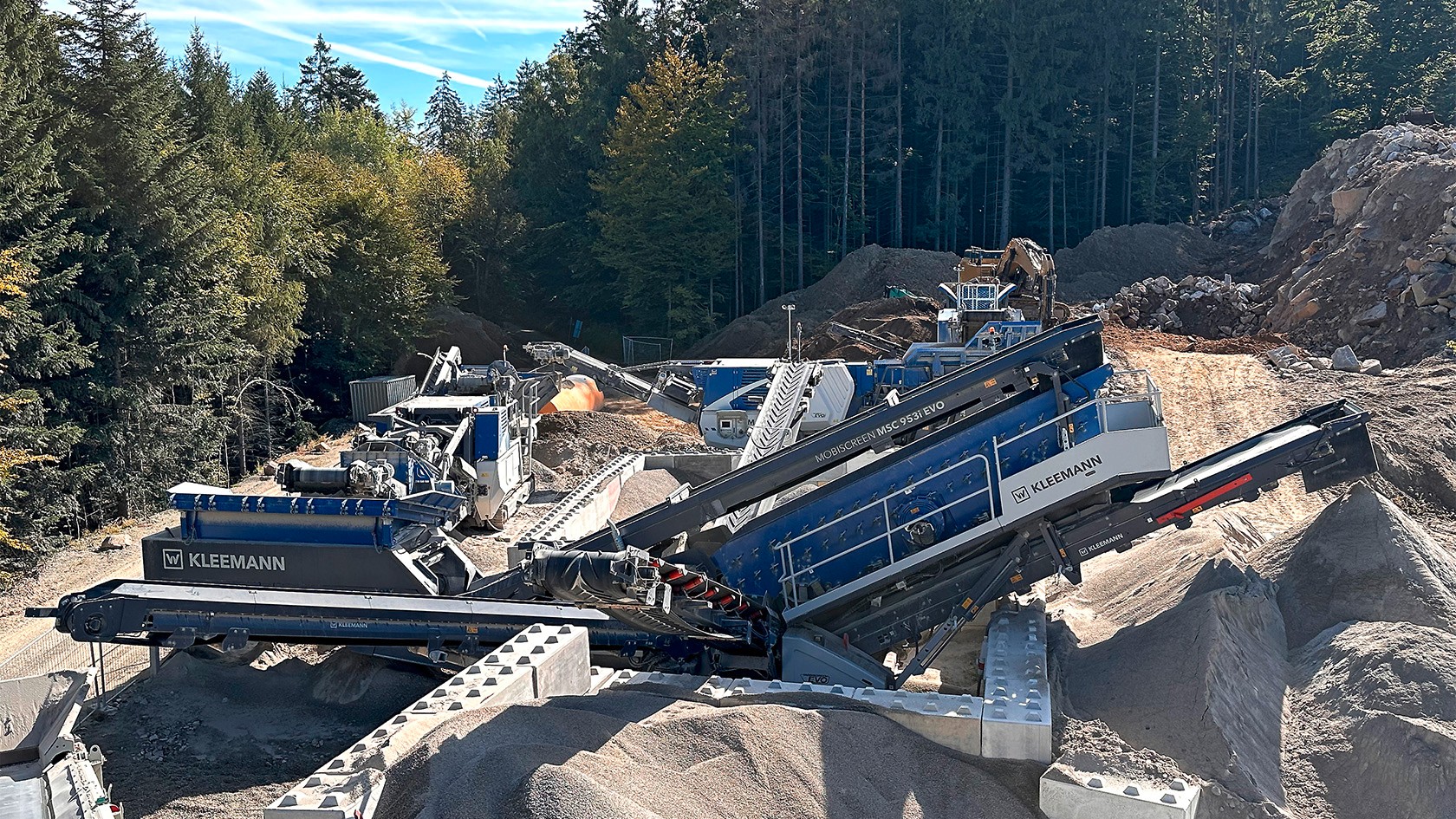
A perfectly tuned plant combination now utilizes large volumes of excavated material in the Bavarian Forest
In a quarry near Winklarn in the Bavarian Forest, the paving stone specialist Godelmann crushes granite into fine grit. The material at the site is extremely hard and abrasive. The end result of a series of tests was a slightly unusual compilation of plants: Two jaw crushers, one cone crusher plus a screening plant.
Godelmann, with its head office in Fensterbach, Bavaria, is a big player in the production of paving stones. The subject of sustainability is a central concern of the company throughout the production process, which was also underscored when they received the German Sustainability Award in 2023. It is self-evident that the company has placed a special focus for a long time on the implementation of transparent and sustainable delivery chains, starting with their own regional production of the raw materials.
Plant train consisting of the jaw crushers MOBICAT MC 120i PRO and MC 110i EVO2, the cone crusher MOBICONE MCO 90i EVO2 and the screening plant MOBISCREEN MSC 953i EVO in the limited space available in the quarry.
When the opportunity arose in the Bavarian Forest to process excavated material that had accumulated over many years in a granite plant quarry owned by the Bavarian State Forest Enterprise, company management and Bernd Godelmann, together with the Technical Manager Josef Regler, grasped the opportunity. Up to that point, a stonemason from the region had been removing freestone to produce large granite products such as countertops or gravestones. This type of extraction produced huge residual amounts that could no longer be used for his purposes – extremely hard and extremely abrasive. “Up to now, no company has really dared to process this material”, explains Andreas Wagner, Kleemann expert from Wirtgen Germany, “particularly when you consider that the location of the quarry is anything but ideal.” The site is in the middle of a forest. Access is a challenge for large machines and space conditions at the site are very restricted.
Kleemann Expert from Wirtgen Germany Andreas Wagner (left) and the Technical Manager at Godelmann Josef Regler (right) in front of the Kleemann plant train.
“We needed a lot of tests to arrive at the present-day result. The Kleemann technicians worked really intensively with us on the complete process as it was honed and optimized. And now we have found a solution that may be unconventional but which works perfectly.”
Josef Regler, Technical Manager at Godelmann
Godelmann recognized that the quarry offered an opportunity to further expand the regional raw material supply. The idea here of utilizing previously unused excavated material fits into the sustainability strategy of the company. And the flexible, mobile Kleemann plants could be the solution for this extraordinary task!
After making contact with the Kleemann process technicians, an elaborate series of tests was started. Now there is a Kleemann plant train in the quarry that crushes the hard material to the desired 0-16 grit – the invested effort achieved the goal in the end. “In this regard, the Kleemann process technicians really did a great job”, says Josef Regler. “We needed a lot of tests to arrive at the present-day result. The Kleemann technicians worked really intensively with us on the complete process as it was honed and optimized. And now we have found a solution that may be unconventional but which works perfectly.”