- Material for dam construction:
- 260,000 m³
- Of which is slate:
- 180,000 m³
- Removal:
- Up to 14 m
- Structure:
- In layers up to 15 m
HAMM VC compactors
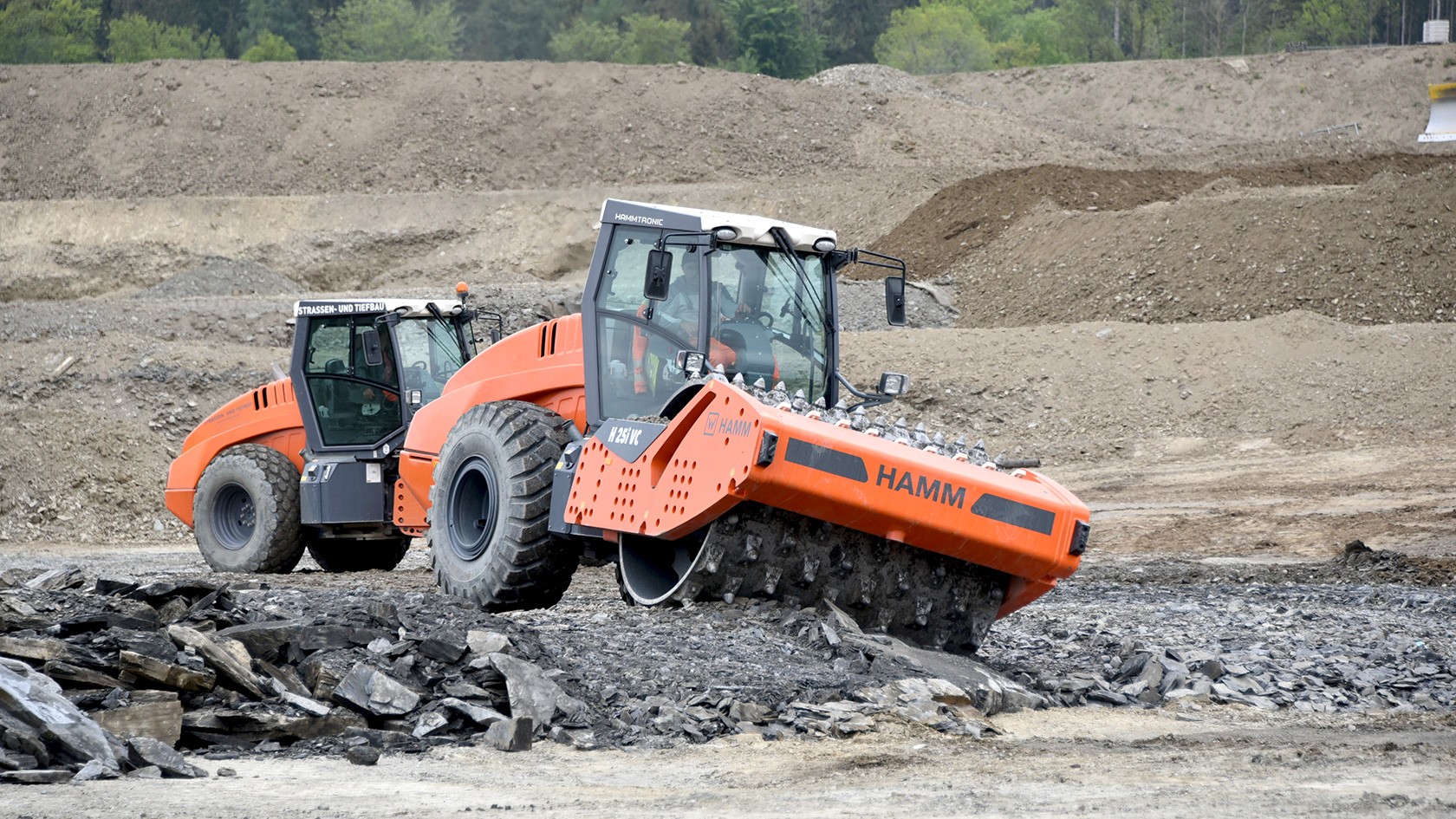
Sauerland/Bad Fredeburg
When constructing a dam with a height of 15 m for a bypass in Bad Fredeburg in the Sauerland region, two HAMM H 25i VC compactors, with their special crusher drum, were used to simultaneously crush and compact the local "Fredeburger" slate. The plate material was originally supposed to be broken to a maximum particle size of 200 mm on the construction site using several jaw crushers, and transported to the dam on a truck. Bulldozers would have distributed the stone there, and compactors would have carried out the compaction in layers. The two H 25i VC compactors were the considerably simpler and more efficient alternative here.
"As soon as I saw the stone, I had a feeling that the HAMM compactor would be perfect for crushing this material."
Michael Tillmann, Construction Manager at Straßen- und Tiefbau GmbH in Kirchhundem
At bauma 2019, Michael Tillmann, from Kirchhundem in the West-German low-mountain region of Sauerland, noticed the H 25i VC compactor. "We were immediately won over by the roller's design. But we never had the right project before," explains Straßen- und Tiefbau GmbH's construction manager. Not long after, there was a project to build a dam for a new bypass using locally available slate.
Without crushers, with significantly fewer transports, but using two compactors: It quickly became clear that the VC compactors from HAMM produced the right fracture pattern for the application.
The site manager was also pleased with the quality of the crushed slate and the compaction achieved for the dam layers. In liaison with the soil expert, a depth of 40 cm was then determined for each layer. The optimal porosity was determined as 6%, and the maximum permitted was 10%. To ensure that the water content was also correct, each layer had to be sprayed with water.
After just a few days, it was clear that speed was now part of the construction process!
"Thanks to decoupling the process steps, we were able to achieve a performance of approx. 4500 m³ per day. This is almost twice as much as set out in the original planning schedule. The main reason for this is the work in layers."
Michael Tillmann
The drum on the VC compactors has a width of 2.22 m and is equipped with 150 quick-change toolholders. Fitting and removing the tools with the VC quick-change system is extremely easy.
Three different attachments are currently available, including one tool set for hard stone and one for soft stone. Their geometries are specially tailored to materials of different compressive strengths. Furthermore, HAMM also offers a padfoot insert for cohesive material.
Marvin Gallus and Mohamed Khalil were at the wheel of the two H 25i VC compactors in Bad Fredeburg and were given detailed instruction on how to use the crusher-rollers by a service technician.
Both singled out its ease of operation and comfort for praise – specifically the quality of the seat and the amount of space available in the cab. The many details designed to make work more pleasant were also much appreciated.
"We found everything very clear and simple after this. The roller is easy to use. I used one of the two 12-V sockets for a cellphone. It is really practical."
Marvin Gallus and Mohamed Khalil, roller operators
Only our genuine spare parts ensure the ongoing reliability of your Wirtgen Group machines, plants, and systems. You can quickly and easily find the spare parts you need on our Parts Website.
Visit Our Parts Website