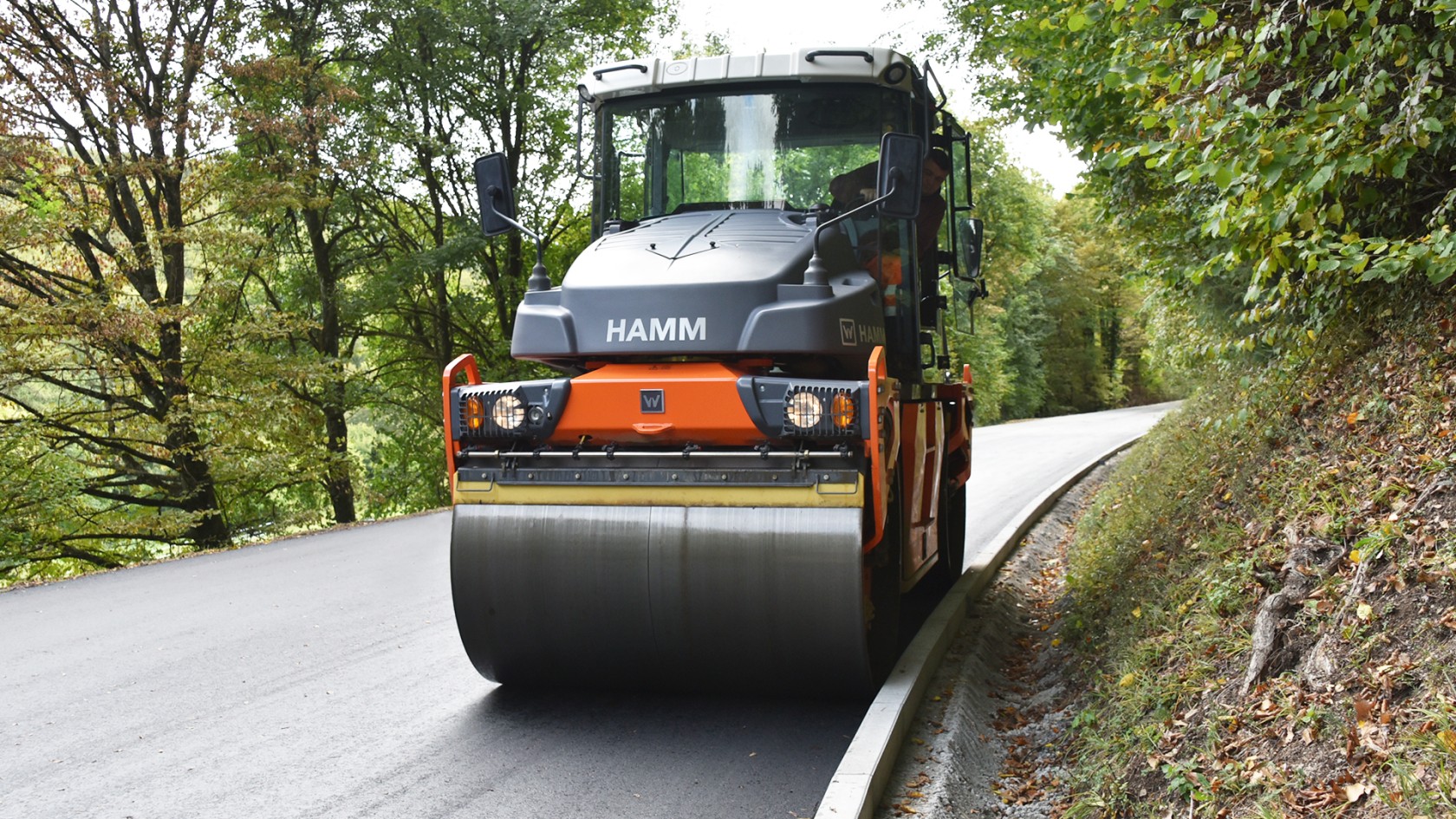
HAMM, who have always been pioneers when it comes to oscillation, again significantly further developed this technology in 2019 with the split oscillation drum and brought this to series production in the rollers of the DV+ series. In practice, it is already very clear that this premium solution produces first-class surfaces. This applies in particular where the compaction is particularly demanding due to tight curves, lots of steering movements or asphalt types that are particularly susceptible to displacement.
In the run-up to the development, numerous customers were surveyed in order to determine the demand for split drums. The responses and wishes represented an important basis on which the HAMM designers could work. The result is a patented premium solution for the DV+ series because, above all, the users of these pivot-steered rollers expressed a wish for a split drum with oscillation. The HAMM range therefore now includes the DV+ 70i VS-OS and DV+ 90i VS-OS models. In these models, the "OS" in the name (O stands for "oscillation" and S stands for "split") indicates that they have split oscillation drums.
Two oscillation units per drum
In the split oscillation drum from HAMM, one full oscillation unit works in each half. These two units are mechanically independent of each other. To ensure that the two drum halves always vibrate synchronously, despite their different rotation speeds around corners, HAMM has integrated an electrohydraulic control. This adapts the position of the unbalanced mass quickly and precisely to the position of the two drum halves. It is precisely this that is decisive for the high quality of the compaction because, in this way, shear stresses in the asphalt that is to be compacted are minimized. This, in turn, ultimately prevents material displacement and cracks.
Successfully using split oscillation drums
On various construction sites across Central and Northern Europe, customers are already familiar with the advantages of compaction using split oscillation drums. A prime example of using the split oscillation drum was the compaction when laying asphalt in the rotary at a junction on freeway A 7 in Northern Germany: "Despite the extremely tight radii, the DV+ 90i VS-OS created a crack-free and, therefore, high-quality surface for the rotary," confirms building contractor Ferdinand Kalinowsky from Ewald Kalinowsky GmbH & Co. KG in Bad Beverstedt. These experiences were also confirmed by Arnold Rijper from BAM Infra in the Netherlands: "Using the split oscillation drum, we have achieved outstanding compaction results within a short time. The drum particularly impressed us when compacting in curves." A significant advantage of oscillation is the rapid increase in compaction. In practice, this means that compaction with oscillation is quick and is therefore extremely economical. When using the split oscillation drum, this feature is now combined with the increase in quality during compaction in curves and for every steering movement.
Quiet compaction, reduced maintenance
In practice, the DV+ 90i VS-OS also scores highly among drivers thanks to its low noise level. The reason for the reduced emissions is, among other things, an optimized drive concept. Furthermore, HAMM uses a new type of toothed belt in all oscillation drums – in the split and non-split models. The toothed belt therefore no longer needs to be changed after 2000 operating hours, as was previously the case. This leads to an additional advantage because the oscillation drums are not only quieter than previous drums, they are also completely maintenance-free. Another benefit: Thanks to highly wear-resistant fine grain steel and high material strength, the drum shells on all oscillation drums from HAMM are extremely robust.