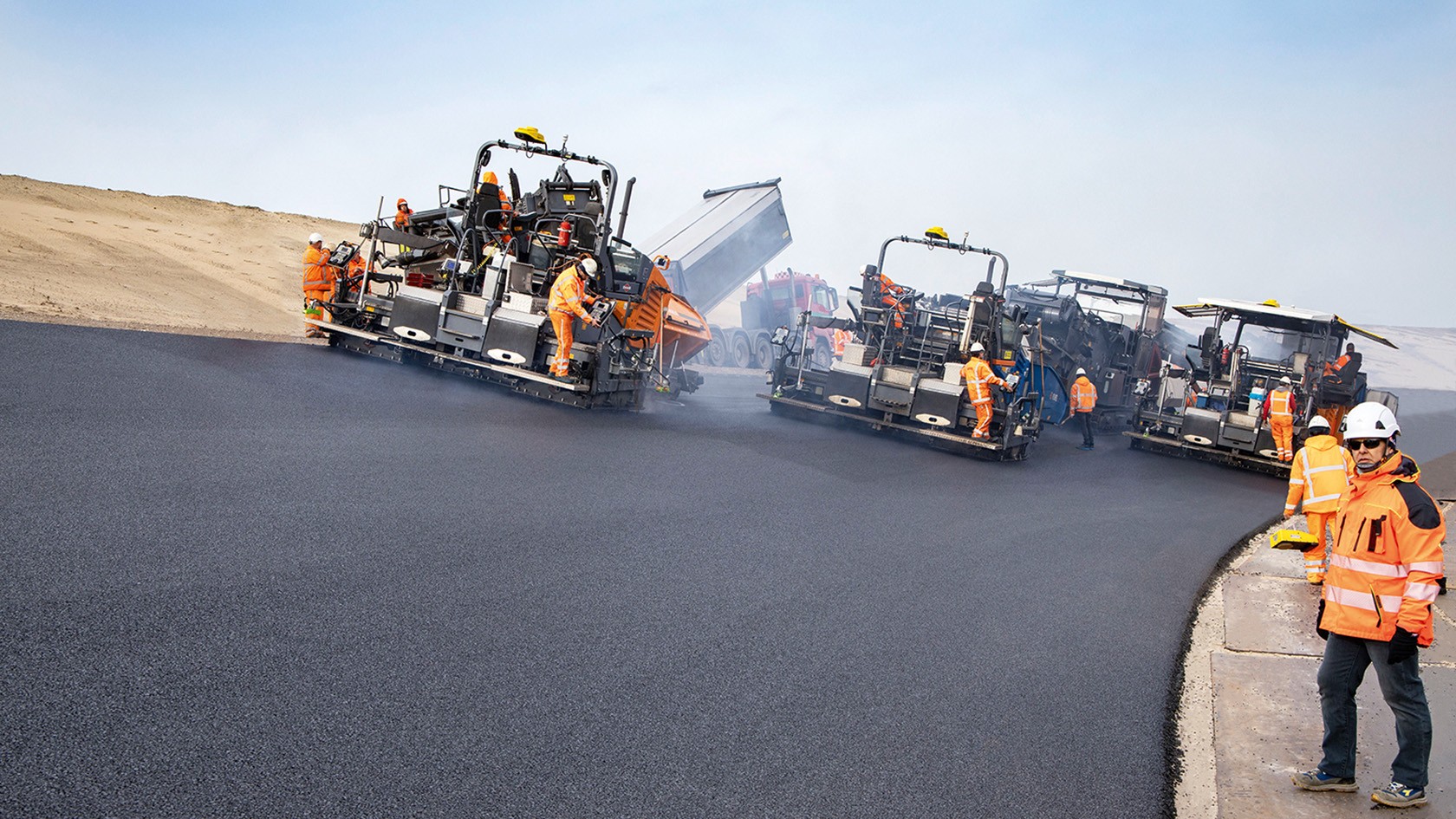
Some construction projects are so special that few contractors can draw on a significant wealth of experience to execute them. That's one reason why it's so valuable to have a partner at your side with the right degree of expertise and commitment. The rehabilitation and redesign of the Zandvoort racetrack was one such project.
How do you procure and process the mandated special mixes meeting the highest standards of the world motor sport federation, the FIA? How do you build in steep bends with gradients of as much as 32%? And how do you meet requirements that, for Filippo Piccoli, technical director of the experienced civil engineering contractor Studio Dromo, are the "most extreme that I have ever encountered and overseen in race track construction"?
In order to find successful answers to those questions, site manager Mark van Kessel from construction contractor Gebr. Van Kessel involved his counterpart Roel Vissers from the WIRTGEN GROUP Netherlands office in the undertaking right from the beginning. After all, building and rehabilitating a race track is always something special. And it certainly was for the contractors Gebr. Van Kessel B. V. and KWS Infra B.V. - both part of Royal VolkerWessels N. V.
The job involved partial reconstruction of the circuit in the area of the two steep bends, as well as accompanying rehabilitation and modernization work. The two steep bends are designed to enable the race cars to achieve higher cornering speeds and so emerge faster onto the straight. The modifications to the track layout are intended to encourage overtaking, and were made according to the plans of the leading Italian race track design firm Studio Dromo, whose experts also closely supervised the job site.
The top race circuit hosted the Dutch Formula 1 Grand Prix a total of 30 times between 1952 and 1985. Now the elite motor sport class is returning to Zandvoort once again. The circuit in the province of North Holland, located on the North Sea coast between the dunes and the sea, is nicknamed the "sand dune roller-coaster".
Preliminary consultations on the project with the WIRTGEN GROUP experts quickly revealed that the paving work needed to be tested with a trial run to ensure that everything ran smoothly on the circuit itself. The two 32% bends are in fact more steeply curved than those on the high-speed oval courses in the USA. So it was vital to the success of the project that the paving team knew exactly what factors to consider when setting up the machinery and running the process.
In addition to the paving, compaction was also a challenge. It was carried out by HAMM rollers of the HW, HD, HD+ and HD CompactLine series.
Tolerance of just ±2 mm: The three SUPER 1900-3i pavers also had to perform precision work on the steep bends, and were equipped with the Big MultiPlex Ski sensor system from VÖGELE for the purpose.
Three VÖGELE SUPER 1900-3i pavers with AB 500 TV screeds were allocated to the job site in Zandvoort. As is the standard requirement on race track construction sites, paving had to be carried out using the "hot on hot" method.
André Felchner, head of applications engineering at VÖGELE, personally oversaw the preparations and the asphalt work. "These highly complex tasks are what we do. Of course, there's a lot to consider to ensure that the asphalt paving and compaction are successfully executed on a road as extreme as this one," Felchner says. "So it's all the more pleasing to encounter a paving team as highly skilled and motivated as this one. The guys quickly grasped what it was all about."
"We knew that we could rely on VÖGELE's technology. Nevertheless, the job would not have been possible without the application advice and on-site support provided by the WIRTGEN GROUP."
Mark van Kessel, site manager, Gebr. Van Kessel B. V. (right, pictured here with Roel Vissers and Ivo Lakerveld, both from WIRTGEN Netherlands, and André Felchner, VÖGELE head of applications engineering).
Despite the spectacular profile, only minor modifications had to be made to the VÖGELE machinery in order to pave the steep bends. "To achieve a high-quality, precompacted result on the extreme slope, only a slight negative crown profile was created," said André Felchner of VÖGELE, explaining one advantage of the AB 500 extending screed. The independently electronically adjustable Screed Assist feature ensured that sufficient pressure could be applied to the mix in the upper outer paving zone. Screed Assist is a feature of SUPER pavers that enables high-quality results even in complex paving scenarios.
The fact that, when the asphalt work was complete, everyone involved in the project was extremely satisfied with the result was in itself a complete success for the entire Royal VolkerWessels team. An even more pleasing compliment was the smiles on the faces of the drivers who contested the first race on the modernized Zandvoort circuit just a week after the works had been signed off. "Everything worked out exactly as we had planned it together with our partners from the WIRTGEN GROUP. That gives us the confidence to know that we can also count on their support on our next tough project," commented site manager Mark van Kessel.
Extending Screed
Compacting systems | TV, TP1, TP2, TP2 Plus |
Paving width of the screed | 8 ft 4 in - 27 ft 11 in |
Basic width | 8 ft 4 in |