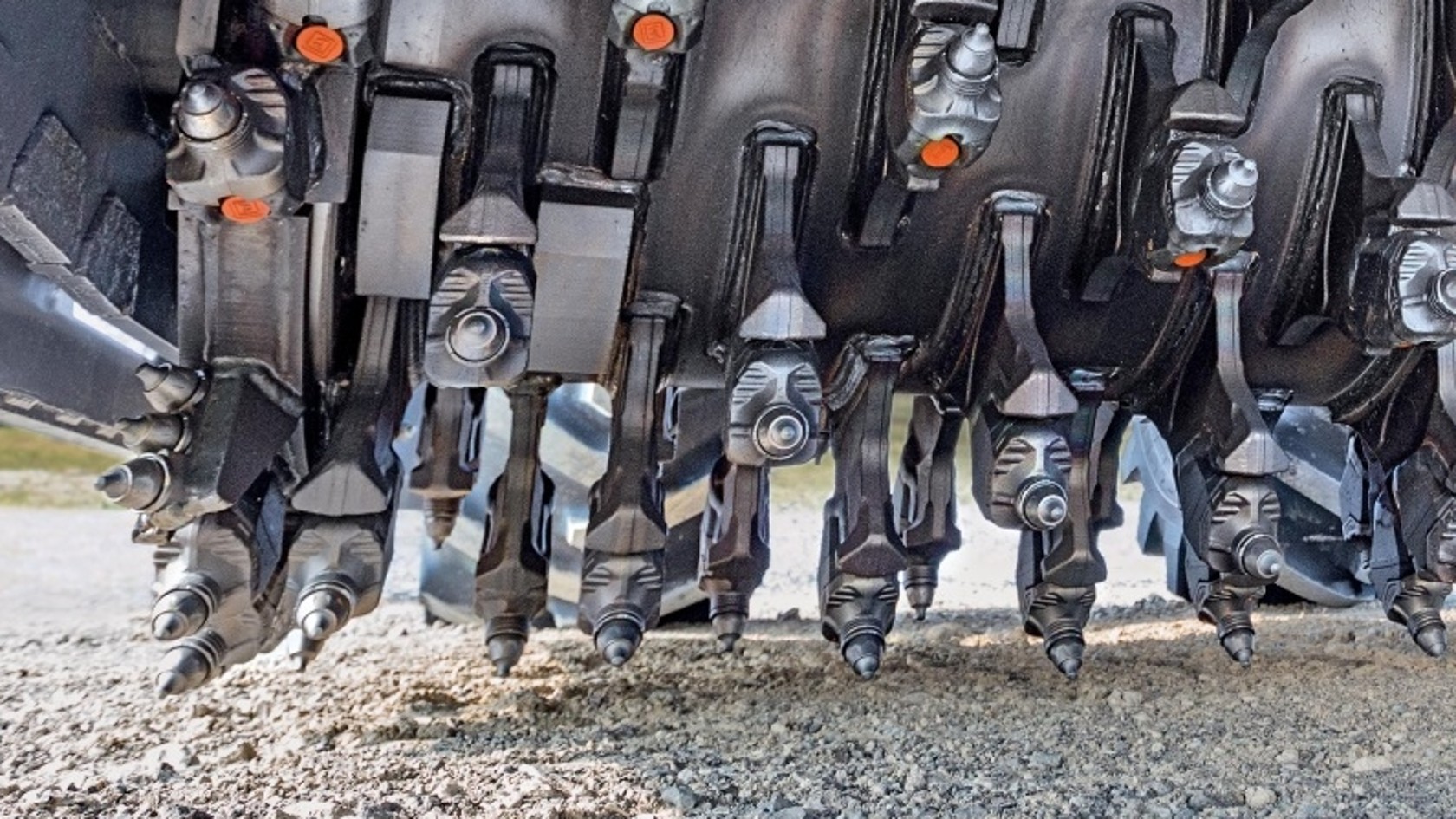
The in-place (on-site) mixing method involves having a cold recycler granulate an existing road surface and mixing in binder and water homogeneously. This creates a new construction material mixture in one work step. The cold recyclers are equipped with a powerful milling and mixing rotor and spray injection systems.
The exact, optimal pick layout on the milling and mixing rotor – paired with the powerful, mechanical drum drive – assures top milling and mixing performance – a basic prerequisite for ideal, homogeneous mixtures. In addition, wear-resistant, quick-change toolholder systems assure optimal turning response of the picks, easy pick changes and long working intervals.
This range includes our state-of-the-art cold recyclers and soil stabilizers. The wheeled machines in the WR series are perfect for cold recycling when the road surface has been structurally damaged up to a working depth of 22 in (560 mm) and are also multifunctional when used for soil stabilization measures. The CR series of cold recyclers equipped with crawler units are particularly suitable for recycling asphalt pavements in need of rehabilitation up to a working depth of 14 in (350 mm).
Generally, a separate STREUMASTER spreader lays down binder material like cement or lime. Behind it, the high-performance milling and mixing rotor of the cold recycler/soil stabilizer thoroughly mixes the asphalt layer to be reconstructed or the non-load bearing soil with the binder that has been applied ahead of it.
Water is provided via a hose line that is connected to a water tank car, and it is applied to the mixing space from an spray injector bar. The pressurized scrapers on the rear drum flap trowel the prepared material for optimal flatness. Finally, suitable HAMM compactors with roller drums compact the soil.
The milling and mixing rotor thoroughly mixes upcoming soil, and if necessary mixes in lime or cement and sprayed water that has been spread in front of it.
The milling and mixing rotor mills asphalt, granulates it, sprays in binder and water as necessary, and mixes the construction material mixture.
If necessary, a STREUMASTER binder spreader spreads cement in front, followed by a water and binder tank car. The milling and mixing rotor of the W 240 CR / W 240 CRi granulates the asphalt layers. At the same time, the cement is mixed in, and water and bitumen emulsion or foamed bitumen is sprayed into the mixing chamber via spray injection bars. The prepared construction material is conveyed to the rear via a primary conveyor belt. The VÖGELE paving screed spreader with spreading auger ensures application appropriate to the profile and position. Then, HAMM drum rollers handle final compaction.
The rugged milling and mixing rotor granulates the damaged asphalt layer. The granulated material is mixed homogeneously in the mixing chamber with spray-injected binder and water to produce a new mixed construction material locally, i.e., on-site.
The spiral-shaped construction of the milling and mixing rotor then conveys the mixed material to the middle and then via the primary conveyor to the installation aggregate. There, the spreading auger spreads the material uniformly in front of the variable paver screed spreader, which ensures paving with proper profile and position.
If necessary, a STREUMASTER binder spreader spreads cement in front, followed by a water and binder tank car. The milling and mixing rotor granulates the asphalt layers. At the same time, the cement is mixed in, and water and bitumen emulsion or foamed bitumen is sprayed into the mixing chamber via spray injection bars. The prepared construction material is conveyed via the belt unit directly into the material bunker of the VÖGELE asphalt paver, which then installs it. Then, HAMM drum rollers handle final compaction.
The rugged milling and mixing rotor granulates the damaged asphalt layer. The granulated material is mixed homogeneously in the mixing chamber with spray-injected binder and water to produce a new mixed construction material locally, i.e., on-site.
The spiral-shaped construction of the milling and mixing rotor then conveys the mixed material to the middle and then via the primary conveyor and the discharge conveyor to the material hopper of the asphalt paver. The paver then installs the mixed material according to the profile and position.