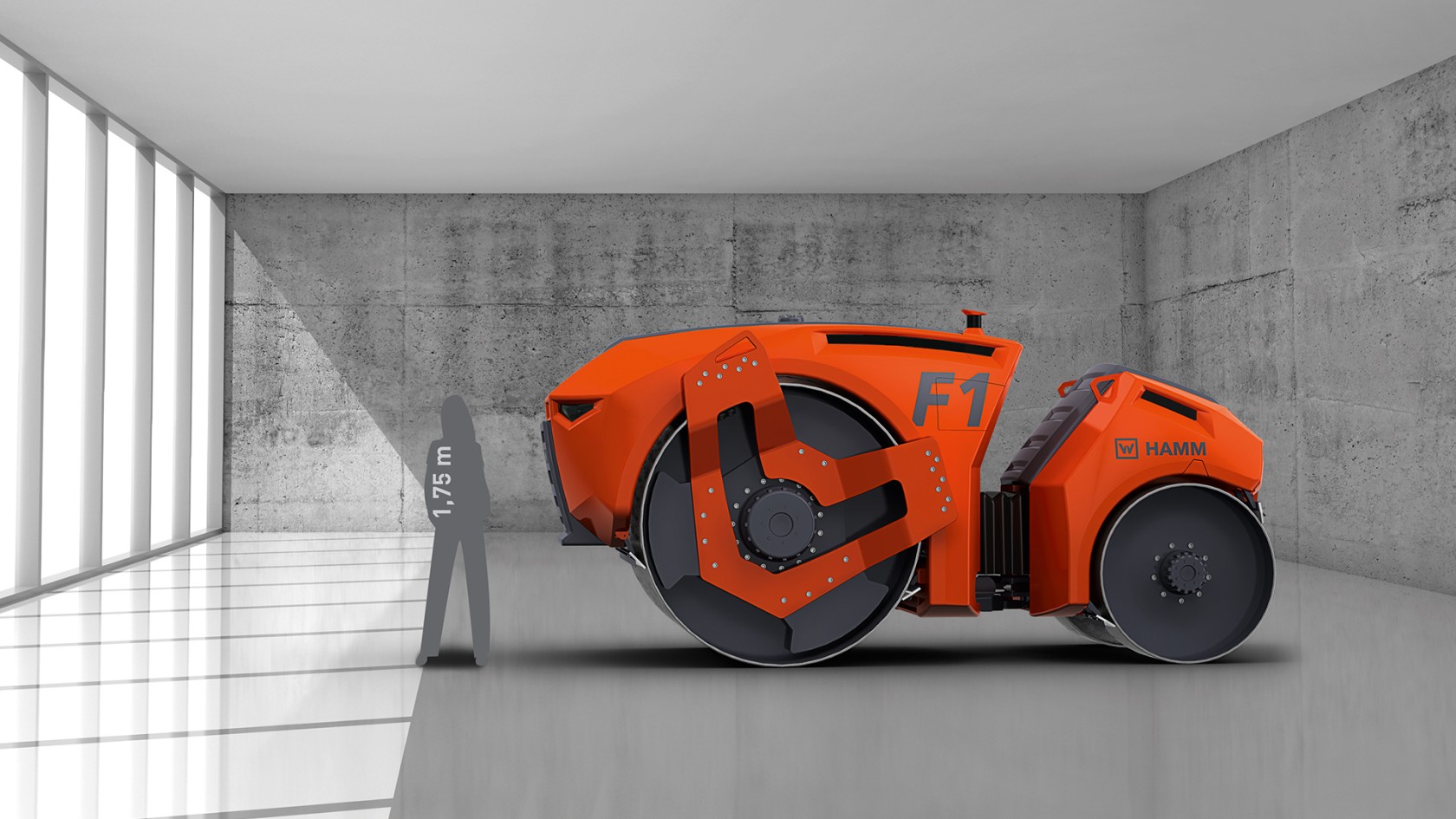
Los vehículos que se desplazan de manera autónoma sin intervención humana todavía no forman parte de nuestro día a día, pero son cada vez más accesibles. En otros ámbitos de la vida, brotan como hongos productos y servicios en torno a la conducción o trabajo autónomo, por ejemplo, los robots cortacésped o limpiacristales. En la industria de la maquinaria de construcción, por el momento existen pocas máquinas que se desplacen de manera autónoma. Sin embargo, los sistemas de asistencia conquistan el sector de la construcción. Desde siempre, HAMM AG se incluye entre las empresas de técnica de compactación que marcan tendencia y que no tardan en utilizar las nuevas tecnologías para mejorar los rodillos. Ahora, la empresa HAMM, con el foco puesto en la tecnología, vuelve a marcar la pauta: esta vez en el desarrollo de equipos de compactación autónomos.
Lo que sucede actualmente en la zona contigua a un circuito de pruebas forma parte del proyecto de futuro «rodillos autónomos». Pasarán todavía muchos años hasta que los rodillos HAMM puedan desplazarse y compactar de forma completamente autónoma, pero los análisis y ensayos realizados por HAMM han demostrado ya una cosa: la calidad y la rentabilidad de la compactación aumentan notablemente con los rodillos autónomos. En los modernos coches y camiones se utilizan cada vez más sistemas de asistencia. Sistemas GNSS de navegación, Tempomat, mantenimiento de distancia, asistente de carril, ayuda de aparcamiento y maniobra y el encendido y apagado automático de la luz de cruce van ganando cada vez más terreno. En muchos países se han convertido incluso en el equipamiento estándar de los vehículos nuevos. Estos sistemas de asistencia conforman la base de los camiones y coches que circulan de forma autónoma y que ya funcionan hoy en día en circuitos de pruebas, desarrollados por los pioneros del sector.
Dr. Stefan Klumpp, del consejo técnico de HAMM AG
HAMM: creador de tendencias con los rodillos autónomos
Aquí HAMM es pionera, continúa explicando el ingeniero mecánico Dr. Klumpp: «Actualmente no conocemos ninguna otra empresa de nuestro sector que tenga un rodillo autónomo. Gracias a nuestras investigaciones sabemos que nuestros clientes pueden aumentar la calidad de la compactación y la rentabilidad con estos rodillos. Hemos visto que otras empresas, líderes en sus sectores, ya están valorando las oportunidades y consecuencias de la «obra autónoma». Así, con algunos clientes ya llevamos bastante tiempo dialogando sobre este tema. El objetivo es optimizar más los procesos de construcción ante una situación de disponibilidad limitada de personal especializado, por un lado, y el uso de máquinas de elevada calidad y eficiencia que consumen pocos recursos, por otro lado».
Ya existe un estudio de diseño
El Dr. Axel Römer, director de investigación y desarrollo de HAMM, ya ha explorado con su equipo cómo podría ser un rodillo autónomo: «Hemos tenido en cuenta aspectos técnicos, constructivos y económicos y los hemos valorado en diversos estudios. El resultado es un rodillo sin conductor que no necesita puesto del conductor, pero sí claramente más sensores, que supervisan el entorno del rodillo, además de los parámetros de compactación. Hemos relacionado estos requisitos y vemos gran cantidad de nuevas posibilidades de diseño. Así, podríamos construir rodillos autónomos con diámetros de tambor mucho mayores, depósitos de agua más grandes y espacio para las baterías de un rodillo accionado eléctricamente. Esto aporta ventajas en cuanto a la calidad, el respeto al medio ambiente y la eficiencia».
En colaboración con diseñadores industriales, HAMM ha ideado y desarrollado el concepto correspondiente con un estudio de diseño. El resultado es impresionante, especialmente el tambor de la máquina de 9 t con un diámetro de cerca de 2 m. En este caso, la altura total de la máquina es mucho menor que en las máquinas actuales con cabina o techo.
Sistemas de asistencia usados ya en la actualidad
Aún falta mucho camino hasta que una máquina así se haga realidad. En HAMM, calculamos que serán décadas. Pero el viaje comenzó hace mucho tiempo con la utilización de numerosos sistemas de asistencia. El más conocido es el HCQ Navigator. Con ayuda de un ordenador a bordo del rodillo y datos GNSS en tiempo real, muestra si ya se ha compactado y cuánto o con qué frecuencia. A esto se añaden las funciones de conducción, como la inversión automática de marcha o el Tempomat, así como las características de seguridad, como las cámaras de marcha atrás. Todas ellas contribuyen a aligerar el trabajo del conductor y a mejorar en la actualidad la calidad de la compactación. Los desarrolladores de HAMM ya están trabajando en otros sistemas, como el asistente de carril, ayudas adicionales a la dirección y el perfeccionamiento del HCQ Navigator.
Sensores y programación complejos
Para que un rodillo pueda moverse de forma totalmente autónoma y al mismo tiempo realizar una compactación de alta calidad, se requieren claramente más sensores y un software más inteligente que en los rodillos actuales. Los sensores registran todos los datos relevantes del entorno del rodillo. Estos son, entre otros, la posición en el espacio, el sentido de marcha, la distancia con otros objetos, los parámetros actuales del material de la superficie que se va a compactar (por ejemplo, la temperatura y la rigidez) y la información meteorológica (por ejemplo, viento o velocidad de enfriamiento). El rodillo debe comparar estos datos con las especificaciones de la superficie (¿dónde se quiere compactar?), con el esquema de compactación (¿cuántos rodillos y cuáles trabajan conjuntamente?) o la compactación deseada (¿qué proporción de huecos se pretende?). A esto se suma la reproducción de la estrategia de compactación con instrucciones para maniobrar antes de invertir la marcha, el procesamiento de bordes, la velocidad de marcha, el uso de sistemas de excitación, etc. En resumen: se trata de una tarea compleja.
10 000 horas de servicio en el circuito de pruebas continuas
HAMM ya ha dado los primeros pasos con éxito y no solo sobre el papel, sino de forma muy concreta con un circuito de pruebas continuas en la fábrica de Tirschenreuth y con la construcción de un «rodillo sombra» que circula sin conductor detrás de otra máquina. Este circuito de pruebas continuas está activo desde 2014. Se creó principalmente para probar prototipos. Desde entonces, los desarrolladores de HAMM hacen pruebas en condiciones reproducibles con sus nuevos desarrollos durante semanas, día y noche, sin conductor. La máquina lleva a cabo un programa predefinido de manera autónoma, se desplaza ella sola para repostar y se estaciona sola cuando finaliza la prueba. Para que el rodillo no choque con personas ni con objetos, los desarrolladores de HAMM han instalado un amplio sistema de vigilancia del entorno. «Hemos hecho pruebas en este circuito durante más de 10 000 horas y hemos aprendido algo sobre la conducción autónoma», explica el Dipl.-Ing. Hans-Peter Patzner, que ha participado en el desarrollo del control de la instalación. En estos momentos le está esperando un nuevo reto, ya que HAMM está trabajando en un segundo circuito de pruebas, de forma que en el futuro podrá haber dos rodillos simultáneamente sobre el terreno. «Para ello hemos desarrollado un sistema de vigilancia anticolisión, otro importante paso hacia la conducción autónoma», afirma el experto en automatización.
Rodillo sombra sin conductor
Pero el segundo proyecto tenía otra orientación: en colaboración con la Escuela Superior de Osnabrück se ha conseguido que un rodillo adaptado sin conductor pueda circular de manera automatizada detrás de una pavimentadora simulada. En palabras del Dr.-Ing. Römer, director de desarrollo: «Si se piensa en este "rodillo sombra", podemos aprovechar todas las posibilidades de la automatización del proceso de compactación. Así, podemos aumentar la calidad cumpliendo las ventanas de velocidad y las trazadas. Con el frenado selectivo del rodillo podemos evitar que se sobrepase el campo del rodillo y, por tanto, la sobrecompactación. Sin olvidar que un cambio preciso de la pista del rodillo puede evitar hundimientos. Todos estos sistemas aportan automáticamente más eficiencia, especialmente cuando estos conceptos se aplican a toda la flota».
Más calidad gracias a la automatización
Independientemente de cómo acabe siendo la compactación autónoma, desde la perspectiva actual el camino pasa por los sistemas de asistencia. «En los próximos años irán aligerando poco a poco el trabajo del conductor, pero ya se inspiran en la visión del rodillo autónomo. Asimismo, cada nueva función de asistencia es útil en el proceso de compactación, independientemente de la visión del rodillo autónomo», explica el Dr. Klumpp. Mientras la vigilancia del entorno no tenga la precisión suficiente para una conducción totalmente autónoma, el conductor del rodillo es imprescindible a bordo. Su intervención es necesaria en determinadas situaciones, por ejemplo, para repostar, en la carga y descarga y si se producen imprevistos. En aviación sucede hoy en día algo parecido: en los modernos aviones comerciales, el piloto automático y otros sistemas se encargan de la mayor parte del trabajo durante el vuelo. Los pilotos manejan el avión durante el despegue y el aterrizaje y en situaciones extraordinarias; por lo demás, su tarea principal consiste en vigilar el proceso.
Nuevos productos que requieren un marco legal
Hasta que los rodillos puedan compactar en la «obra autónoma», además de la técnica también hay que tener en cuenta los aspectos legales. Así, se plantean dudas tales como: ¿Quién es el responsable si una máquina autónoma provoca daños: el fabricante, el propietario, el diseñador? También hay que dar respuesta a determinadas cuestiones: ¿El diseño del control debe priorizar la protección de un objeto del entorno o bien la calidad de compactación óptima? Estos aspectos serán debatidos por fabricantes y usuarios en conversación con clientes, autoridades y representantes políticos y legislativos.
Un proceso de construcción más estructurado
Puesto que el desarrollo de máquinas de construcción autónomas supone un gran esfuerzo para los fabricantes, en HAMM se ha reflexionado también sobre las condiciones marco en las que se establecerán estos sistemas. El Dr. Klumpp explica a este respecto: «Creemos que las carreteras de asfalto y hormigón seguirán siendo necesarias y seguirán construyéndose dentro de 50 años. Pero para seguir avanzando hacia las máquinas autónomas, es necesario que cambie el entorno y, por tanto, los procesos de construcción. Las máquinas autónomas existen en nuestro sector, por ejemplo, en la minería. Allí se trabaja en sistemas cerrados con un alto grado de estandarización, existen pocos puntos de contacto con el exterior y pocas incidencias imprevisibles sobre el proceso. En estas condiciones marco tan definidas, ya hoy en día enormes dúmperes transportan la roca sin conductor durante kilómetros a través de grandes minas. En comparación con esto, en la construcción de carreteras los procesos están mucho menos definidos y no son tan estructurados. Cada obra es un poco diferente. Hay mucho más contacto con el entorno (y, con ello, mayor potencial de peligro) y el comportamiento de los usuarios no está estandarizado. Para poder seguir aprovechando el potencial de la automatización, tendría que haber, por ejemplo, partidas de obra más grandes y mayor estandarización en la construcción de carreteras. A su vez, esto requiere un cambio en el modo de pensar de los diseñadores y de las empresas que ejecutan las obras».
Dr. Stefan Klumpp, del consejo técnico de HAMM AG
De conductor del rodillo a mánager del rodillo
En última instancia, también se transformará el perfil profesional del conductor del rodillo. En un primer momento, una mayor automatización podría ayudar a paliar el problema de la falta de especialistas. Más adelante, cuando los rodillos sombra o los rodillos manejados a distancia conquisten las obras, el perfil profesional cambiaría de nuevo: de ser el conductor que maneja la máquina, a mánager que parametriza y vigila una flota entera de máquinas, quizás incluso desde la oficina. Esta evolución tendría lugar primero en países con un nivel salarial más alto, suponiendo que traiga consigo ventajas cualitativas y comerciales. En este caso, el ahorro de costes se conseguiría con mayor eficiencia y menos personal. A esto se le sumaría que ya no serían necesarios los trabajos de repaso gracias a la mayor calidad. Todo esto requiere herramientas de planificación e interfaces adecuadas para diseñadores y clientes, así como el correspondiente marco legal. Este contexto se irá desarrollando paralelamente a las máquinas.