Tecnología de trituración
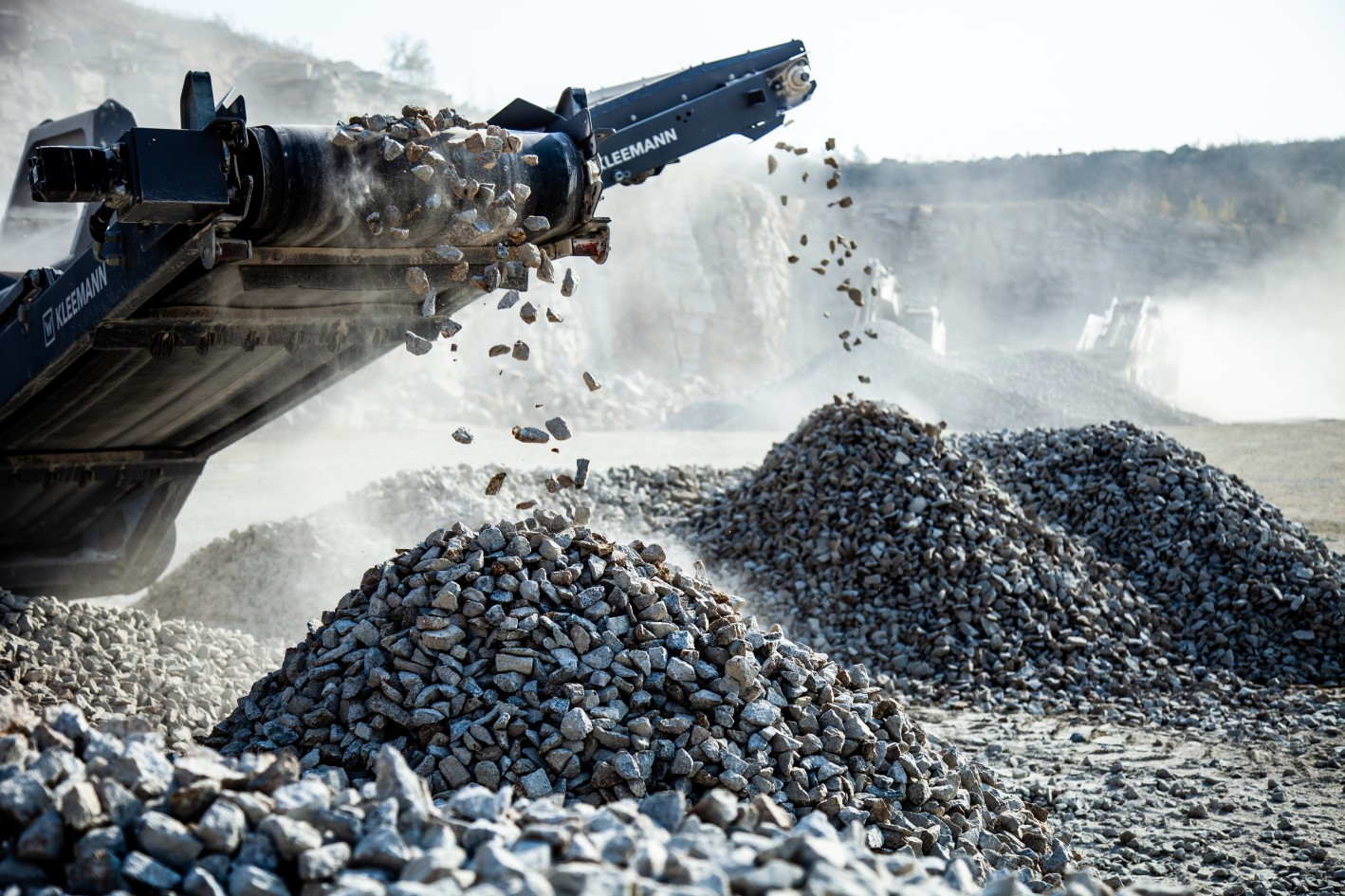
El material de carga, el producto final deseado y la rentabilidad son factores que influyen a la hora de elegir la técnica de trituración.
La extracción de los tipos de roca natural se asocia con el uso de máquinas que trituran materiales con alta resistencia a la compresión de una manera específica y efectiva. Las machacadoras de mandíbulas son perfectas para las aplicaciones exigentes en las canteras y se usan principalmente como machacadoras previas.
Las machacadoras de mandíbulas trabajan según el principio de trituración por presión. La trituración del material de carga se realiza en la ranura en forma de cono entre la mandíbula trituradora fija y la mandíbula trituradora movida por un eje excéntrico. El movimiento elíptico provoca que el material de carga se triture y caiga hacia abajo debido a la fuerza de la gravedad. Este proceso continúa hasta que el material es más pequeño que la rendija de machacado ajustada.
La energía de trituración actúa con gran fuerza y poca velocidad en el material de carga. El nombre «machacadora de mandíbulas» proviene de las mandíbulas de trituración necesarias para triturar y del movimiento que recuerda a la masticación.
Las machacadoras de mandíbulas se utilizan para la trituración gruesa y la pretrituración de piedras quebradizas, duras y semiduras. Se utilizan principalmente como machacadoras primarias.
Las machacadoras de mandíbulas no suelen poder generar un producto final normalizado. En algunas aplicaciones de reciclaje, se pueden utilizar machacadoras de mandíbulas pequeñas para producir capas portantes de balasto para la construcción de carreteras y caminos secundarios.
Las machacadoras de cono se utilizan en piedra natural de dureza media a alta y en piedra natural abrasiva, así como para el procesamiento de materias primas en instalaciones de minería. Las machacadoras de cono suministran granos finales cúbicos normalizados en las etapas de trituración segunda y tercera.
Las machacadoras de cono se encuentran disponibles en diferentes tamaños, modelos y para distintas aplicaciones.
En las machacadoras de cono, la trituración se realiza mediante trituración por compresión en una rendija de machacado que se abre y cierra constantemente entre el forro fijo y el forro móvil. La apertura y el cierre se producen simultáneamente en los lados opuestos del espacio de trituración.
Las machacadoras de cono se encuentran disponibles en diferentes diseños. KLEEMANN utiliza machacadoras de cono en las que el eje de la machacadora está introducido a presión en el bastidor. El soporte de la machacadora de cono se apoya en una unidad de accionamiento excéntrica. La rotación de la unidad de accionamiento provoca la apertura constante de la ranura entre el forro móvil y el forro fijo. La granulometría objetivo se modifica elevando o bajando el forro fijo.
Las machacadoras de cono y las machacadoras rotatorias suelen utilizarse cuando ya no es posible una trituración por impacto debido a una mayor resistencia a la compresión del material de carga o cuando los costes de desgaste debidos a la abrasividad de la roca no son rentables.
Por su forma constructiva, las machacadoras de cono y las machacadoras rotatorias están limitadas en lo que respecta al tamaño de entrada y a la relación de trituración posible.
En instalaciones móviles, las machacadoras de cono se utilizan principalmente para el postriturado en las etapas de trituración secundaria y terciaria.
Las machacadoras rotatorias se distinguen de las machacadoras de cono por su diseño.
A diferencia de la machacadora de cono, que dispone de un eje fijo sobre el que rotan la unidad de accionamiento y el soporte del cono, la machacadora rotatoria cuenta con un eje principal de desplazamiento vertical hidráulico sobre el que se embute con fuerza el soporte del cono. El eje se apoya axialmente en el extremo inferior sobre un cojinete de empuje que, por su parte, está alojado en el émbolo de ajuste. La rendija de machacado se ajusta elevando y bajando el émbolo de ajuste y, por tanto, el eje principal. En el extremo superior, las fuerzas de trituración horizontales se derivan a la parte superior de la machacadora a través de la quicionera, integrada en un travesaño transversal denominado «spider».
Por su forma constructiva, la altura de una machacadora rotatoria suele ser mucho mayor que la de una machacadora de cono equiparable.
Los potentes todoterreno
Tanto en la extracción en cantera como en la obra: con los molinos de impacto, la roca se tritura con eficiencia, de manera que se cumplen las exigentes normas para áridos de hormigón y de asfalto en cuanto a forma del grano, distribución del grano y limpieza. Además de una calidad de producto excelente, los molinos de impacto también consiguen capacidades de rendimiento considerables.
A diferencia de la trituración por compresión, el molino de impacto funciona con el principio de trituración por impacto y golpe. Un rotor que gira a gran velocidad captura el material de carga, lo acelera y lo lanza contra un mecanismo de impacto fijo, las placas de ajuste. Desde allí, vuelve al circuito de impacto del rotor. De este modo, el material de carga se tritura hasta que puede pasar por la ranura entre el rotor y las placas de ajuste.
El proceso de trituración en sí se produce cuando la roca entra en contacto con los barrones y las placas de ajuste. También se produce la trituración cuando las piedras entran en contacto entre sí.
Los molinos de impacto se utilizan como machacadoras primarias y secundarias. Se utilizan como machacadoras primarias con piedra caliza, sobre todo cuando es necesario obtener una gran parte de finos, una buena cubicidad y superficie de corte, así como un gran rendimiento.
En la actualidad, el alto rendimiento y la excelente calidad del producto final de los molinos de impacto se han convertido en elementos indispensables para las instalaciones de reciclaje moderno de hormigón, asfalto y escombros. A diferencia de lo que ocurre en la trituración por compresión, son capaces de liberar limpiamente el acero de armadura del hormigón y producir así un producto final sin apenas hierro.
Como machacadoras secundarias, suelen utilizarse después de las machacadoras de mandíbulas para generar productos finales normalizados.
Se habla de molinos impactores cuando el producto final que se quiere producir con ellos solo debe tener una granulometría de hasta aprox. 10 milímetros. Los molinos impactores se utilizan para la trituración posterior en la tercera o cuarta etapa de trituración, ya que los tamaños de entrada deben ser menores.