Reciclaje al más alto nivel.
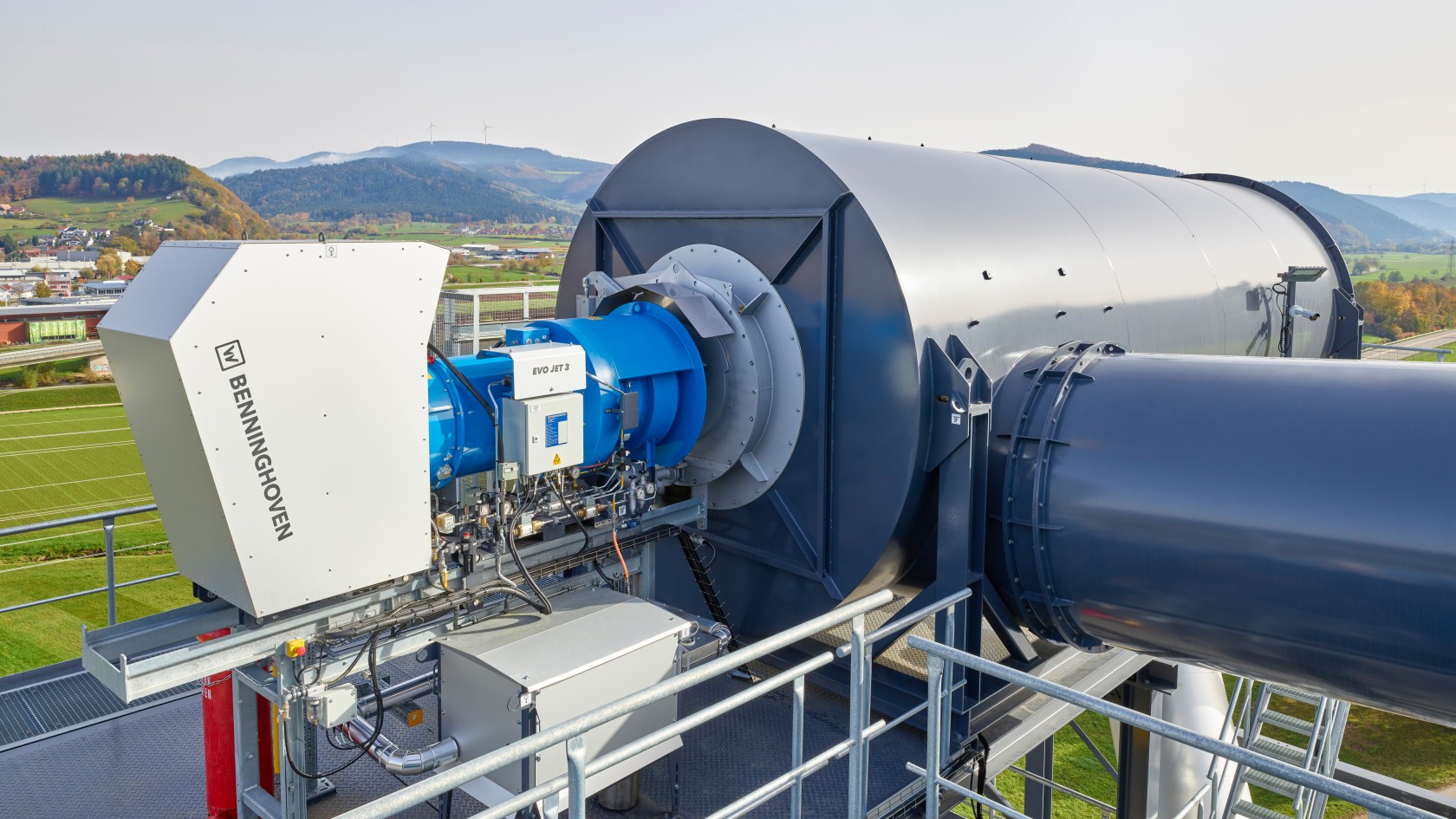
La industria del asfalto está siempre en busca de soluciones para optimizar los procesos que se llevan a cabo en las plantas de mezcla asfáltica. Un principio esencial es aumentar la cantidad de añadido de asfalto de revestimiento en todas las fórmulas.
Los tambores de reciclaje en los procesos de corriente continua operan actualmente a nivel mundial en todos los tamaños y niveles de rendimiento. Esta técnica ha demostrado su eficacia en las últimas décadas y los fabricantes de plantas la han desarrollado continuamente. Sin embargo, todo buen concepto topa con sus limitaciones. Esto mismo le ha ocurrido al calentamiento del asfalto en los procesos de corriente continua, donde el material fluye en la misma dirección para generar calor. Las temperaturas de salida durante este proceso están limitadas a 130 °C debido a las emisiones de escape que se producen.
Las propiedades físicas del secado de corriente continua, así como las características negativas asociadas (tales como una temperatura del gas de escape superior a la temperatura del producto y, como resultado, unos valores altos de emisión de gas de escape y un mayor consumo de energía) nos han impulsado a explorar nuevos caminos.
El material reciclado se calienta – nuevo – en contracorriente. Es decir, el material en el tambor fluye en sentido opuesto a la fuente de calor. De esta forma, las temperaturas del material son más altas; lo que logra reducir al mismo tiempo la temperatura del gas de escape. La temperatura de salida de 160 °C coincide con la temperatura de procesamiento y la temperatura del gas de escape se sitúa por encima del punto de rocío, a aproximadamente 100 °C.
Efecto positivo para el material blanco: Como el material ya no tiene que transportarse sobrecalentado, se reduce significativamente el consumo de energía. El proceso solo es posible empleando un generador de gas caliente, ya que con un calentamiento directo el material reciclado ardería y quedaría inservible. El quemador, el generador de gas caliente, el tambor de secado, la campana de separación y el sistema de circulación de aire están perfectamente adaptados entre sí.
El quemador se desplaza sobre su bastidor hacia delante y hacia atrás automáticamente según el estado de funcionamiento. A continuación, el aislamiento se desliza hacia dentro y hacia fuera. Este procedimiento ha sido diseñado específicamente para que después de apagar el proceso de quemado, los componentes integrados en el interior del quemador no sufran daños. Debido al efecto chimenea y al aumento del aire caliente asociado procedente del tambor de reciclaje, el quemador sin este aislamiento no estaría protegido. Si el quemador se inicia de nuevo, el aislamiento se repliega y toda la unidad está en posición de funcionamiento.
El quemador suministra la energía térmica necesaria para el secado y el calentamiento del material reciclado. Este quema en el generador de gas caliente, donde la llama se mezcla intensamente en contracorriente con el aire de circulación. El material reciclado se calienta entonces de manera indirecta a través del aire caliente. De esta forma, los niveles de emisión contaminante se sitúan por debajo de los límites normales.
En el tambor, el material reciclado se calienta en contracorriente a lo largo del tambor; donde los gases, a su vez, se enfrían. El material ya calentado a la temperatura final pasa directamente a uno de los dos silos de almacenamiento. Aquí se extrae por medio de una báscula y se suministra al mezclador. La sección transversal de la campana de escape es lo suficientemente grande como para reducir la velocidad de los gases de escape despedidos y que, así, arrastren la menor cantidad de partículas finas. Las partículas separadas caen en una bandeja colectora y se transportan desde aquí a la salida del tambor. De esta forma, se mantiene la composición granulométrica de la materia prima. Este proceso es necesario para cumplir con seguridad los futuros niveles de emisión más estrictos.
Public Relations
Reinhard-Wirtgen-Straße 2
53578 Windhagen
Alemania