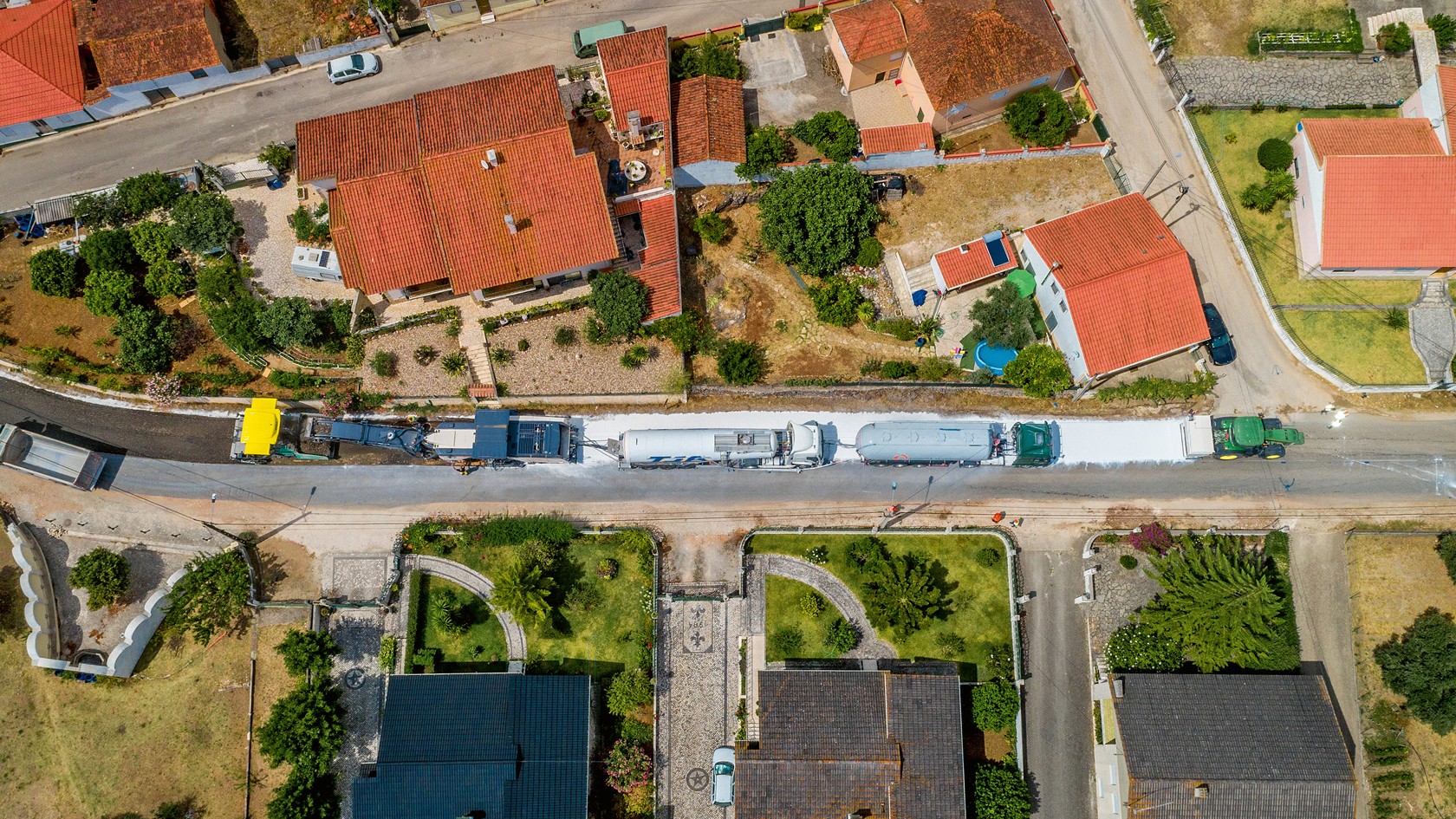
Había que renovar estructuralmente la carretera nacional ER 361 a su paso por la localidad de Monsanto —a unos 100 km al norte de Lisboa— en un tramo de 2,7 km en ambos sentidos. El organismo licitante, Infrastructuras de Portugal, había planificado unas 12 semanas para el saneamiento. Los expertos en construcción de carreteras de la empresa Pragosa solventaron el trabajo con el método de reciclaje en frío en solo 4 días.
El corazón del tren de reciclaje en frío es la nueva W 380 CR de Wirtgen, que en esta obra llevó a cabo su primer trabajo para Pragosa. Es capaz de reciclar las capas antiguas de la carretera en una sola pasada. Una extendedora de Vögele se encarga del extendido acorde a las capas y varios compactadores de Hamm realizan la compactación final.
Fresado, tratamiento, extendido y compactación: saneamiento de carreteras ecológico con tecnología de WIRTGEN GROUP
Desde el principio de la obra alineamos todas las máquinas en el patio de la empresa constructora e impartimos a todo el equipo de la obra la formación correspondiente acerca de la tecnología y la técnica de las máquinas. Una vez preparados de forma profesional para los requisitos del proyecto, los integrantes del equipo y las máquinas de WIRTGEN GROUP colaboraron a la perfección y el proyecto se concluyó con gran eficiencia y unos resultados excelentes. Pocas veces he trabajado en el mundo con un equipo tan magnífico y bien compenetrado.
Mike Marshall, experto en reciclaje de WIRTGEN GmbH
El tiempo es otro factor de éxito del reciclaje en frío in situ, como se denomina esta aplicación. Acortar la duración de la obra de 12 semanas a 4 días solo fue posible gracias a que no hubo que transportar ningún material. La planificación de la obra en sí había previsto excavar ambos carriles a 54 centímetros de profundidad y renovarlos desde la base. Esto suponía una acumulación de 7500 m³ de material que habría que haber transportado desde la obra para a continuación sustituirlo por el correspondiente material nuevo. Incluidos todos los trabajos correspondientes, la sustitución de ese material daba lugar al plazo de construcción planificado de 12 semanas. El reciclaje en frío in situ hace innecesaria la sustitución del material, ya que permite reutilizar el material existente in situ («in-place» en inglés). Añadiendo cal y betún espumado como ligantes y utilizando todos los materiales ya existentes se produce directamente in situ un nuevo material de construcción de alta calidad. El nuevo material estabilizado con betún (BSM, por sus siglas en alemán) ejerce como «columna vertebral» de la populosa carretera y se puede volver a transitar por ella de inmediato en cuanto se concluye un tramo.
En la obra, la anchura de vía oscilaba entre 2,75 m y 3,25 m. Por tanto, la recicladora en frío W 380 CR se utilizó allí con su anchura de trabajo estándar de 3,8 m con una unidad del prestador de 3,2 m de anchura de trabajo. El innovador sistema MCS permitió hacer el reequipamiento incluso en la propia obra.
El diseño mixto para la nueva capa de BSM y las pruebas de la estructura de carretera existente corrieron a cargo de la Universidad del Miño. En dichas pruebas se constató que la base de la carretera aún ofrecía suficiente capacidad portante como para que una capa de BSM más una capa de rodadura nueva de asfalto constituyera una alternativa duradera a la convencional nueva construcción, que supone un alto coste. Para elaborar la nueva capa de BSM había que incorporar a la mezcla 7 kg de cal por metro cuadrado. La cal se aplicó directamente sobre la calzada antigua antes del proceso de mezcla. El Streumaster SW 5 RC unido a un tractor John Deere se encargó de una distribución ideal gracias a su grupo esparcidor especialmente preciso. La anchura de trabajo máxima de 2,5 m exigió que el esparcidor recorriera dos pistas para alcanzar la anchura de trabajo de 3,2 m del CR. La aplicación limpia y el ajuste adaptado de la anchura de trabajo permitieron garantizar una especial precisión en el esparcido, lo que mantuvo los costes al nivel mínimo posible.
El esparcidor de ligante en polvo SW 5 RC montado en la parte trasera distribuye con precisión la cantidad de cal necesaria por delante del tren de reciclaje en frío.
La W 380 CR fresó a continuación a 16 cm de profundidad a través de la capa de rodadura de asfalto dañada hasta la capa interior. «La profundidad de trabajo de la recicladora en frío fue de 16 cm para producir una capa de BSM con suficiente capacidad portante», explica Mike Marshall. Añadiendo solo un 2,6 % de betún espumado y agua, la cal se incorporó directamente a la mezcla. Con el método Downcut se mezcló la nueva capa de base homogénea a partir de material existente tomado de la capa de rodadura y parte de la capa interior junto con los aditivos. La enorme potencia de motor de la CR, unida a la potente barra de betún espumado, permitió avanzar a 5 m/min. En este sentido, la CR produjo unas 320 toneladas de material mezclado BSM de alta calidad a la hora. «Como ligante se eligió el betún espumado. Ofrece muchas ventajas en cuanto a procesabilidad y eficiencia de costes. Además, gracias al tratamiento en frío se consigue una considerable reducción de CO₂», explica Mike Marshall.
La cinta de carga con regulación flexible de la W 380 CR transportó las 320 t de BSM al silo de la Super 1900-3i de Vögele que la seguía. Con su capacidad de rendimiento máxima de hasta 900 t/h, la extendedora trabajó en el modo ECO con un especial ahorro de combustible. La regla extensible TP2 utilizada, con tecnología de alta compactación de Vögele, cuenta con equipo de compactación y dos listones de presión. Se encargó de una intensa compactación previa y, gracias a la posibilidad de regular el número de giros y la elevación, se adaptó a la perfección a las características del material reciclado. Unos sistemas de nivelación ideales, unidos al diseño compacto de la Super 1900-3i, le permitieron a la CR seguirla dentro del carril y extender el nuevo carril en la posición correcta.
Para finalizar la obra, siguieron a la extendedora tres compactadores de Hamm. Un rodillo tándem HD+ 110i con tambores lisos se encargó de un primer sellado y aseguramiento de la capa extendida con limpieza. A continuación, dos rodillos de neumáticos GRW 18 realizaron la compactación final. El alto rendimiento de compactación de los rodillos de Hamm estableció una transición sin fisuras con el carril no fresado. Tras unas pocas pasadas de los rodillos de neumáticos, la calidad superficial de la capa de BSM era tan buena que se pudo liberar el carril para el tráfico. Incluso la carretilla elevadora de horquillas de una empresa local pudo transitar con plena carga por la calzada reciclada sin dañar la superficie.
Tras el tren de reciclaje en frío, como último paso se aplicó el «Fog Sealing»: se trata de una emulsión bituminosa diluida que sirve para proteger la capa de BSM y que no se abra. El «Fog Sealing» no se tuvo que retirar antes de superponer la nueva capa de rodadura de 5 centímetros de grosor. Sirve adicionalmente como capa interior y es capaz de soportar durante mucho tiempo todo el tráfico. En este caso más de cinco meses hasta que se aplicó definitivamente la capa de rodadura.
La pequeña localidad de Monsanto se beneficia plenamente de la obra de construcción. En solo cuatro días se consiguió terminar la obra, aunque la localidad representaba todo un reto por sus curvas sinuosas y sus entradas de empedrado.
Con el método tradicional, la ER 361 habría resultado intransitable en este punto durante 12 semanas, algo que habría sido muy problemático para los habitantes y las empresas locales. Gracias al reciclaje en frío in situ, las casas solo estuvieron aisladas del tráfico durante media hora antes de que todo volviera a funcionar como de costumbre. Sin agujeros provocados por las excavadoras, sin cortes de tráfico... Incluso bastó con bloquear el carril en el que se estaba trabajando en cada momento.
El capataz Pedro Silva, de la constructora Pragosa, y el experto en reciclaje de WIRTGEN Mike Marshall (izquierda) se mostraron de acuerdo: el reciclaje en frío in situ con la W 380 CR es extremadamente rápido y rentable.
Con el reciclaje en frío, las ventajas para el medio ambiente son evidentes. Según datos de Pragosa se ahorraron aprox. el 98 % de las emisiones de CO₂ en comparación con el método de construcción convencional. Esto se debió fundamentalmente a la reutilización del material de construcción in situ, que de lo contrario en esta obra habría supuesto unos 1500 trayectos de ida y vuelta en camión. Además, también se suprimieron los costes de vertedero derivados de la eliminación y los costes de la extracción del nuevo material. Por tanto, adicionalmente se respetaron los recursos naturales y se ahorraron costes.