Réfection de la piste de la base aérienne de Büchel
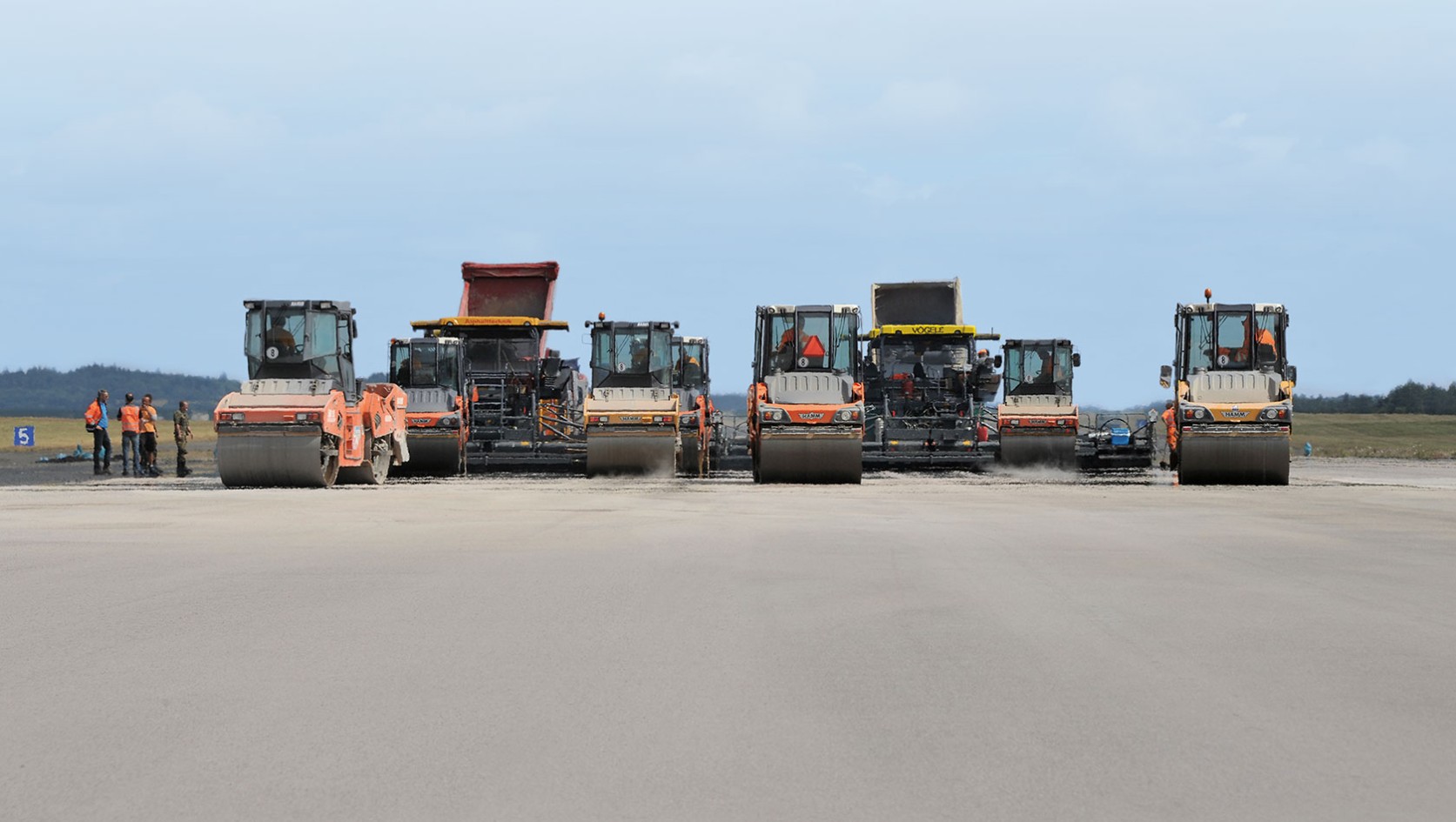
La puissance concentrée du WIRTGEN GROUP au service de la base aérienne de Büchel : des machines WIRTGEN, VÖGELE et HAMM assistées de centrales d’enrobage BENNINGHOVEN rénovent avec une parfaite maîtrise la couche de roulement de la piste de décollage et d’atterrissage – dans les délais et avec une qualité optimale. Le secret : une logistique de chantier minutieusement préparée, des technologies précises et fiables ainsi qu’une forte implication des entreprises de construction participantes.
Située dans les hauteurs de l’Eifel en Allemagne, la base aérienne de Büchel affiche une moyenne de 200 décollages et atterrissages de Tornados par mois. S’ajoutent à cela les vols des avions de transport. Ayant près de dix ans de trafic aérien et plusieurs rudes hivers à son actif, la piste risquait de causer des dommages aux appareils (FOD, Foreign Object Damage). Il s’agit de dommages causés par des corps étrangers, par exemple des agrégats minéraux qui se détachent de l’enrobé, sont aspirés et détériorent les réacteurs au démarrage. Ce type de dommages est donc particulièrement redouté des exploitants d’aérodromes.
Après avoir constaté que, sur la piste de décollage de Büchel, des fragments pouvant atteindre 5 cm de diamètre se détachaient à certains endroits, la planification de la réfection du revêtement – une couche de roulement en enrobé d’environ 4,5 cm d’épaisseur devant être recouverte d’un revêtement antidérapant d’environ 0,5 cm – a débuté immédiatement. Durant la phase de planification, le bureau d’ingénieurs Ingenieurbüro Brenner établi à Hennef en Allemagne avait envisagé plusieurs variantes de réfection, mais c’est la réfection de la couche de roulement à l’enrobé Splittmastix qui l’a emporté. Par rapport à d’autres structures de couche de roulement, ce matériau a l’avantage de fournir une adhérence nettement meilleure tout en étant durable et résistant à la déformation.
Les travaux ont commencé par l’intervention de fraiseuses à froid WIRTGEN pour l’enlèvement de la surface d’enrobé endommagée, et ce en deux opérations : les premiers 5 – 10 mm, recouverts d’un revêtement antidérapant, ont dû être enlevés séparément. La couche supérieure a donc été fraisée avec des tambours de fraisage très fin sur une profondeur de fraisage de 10 mm exactement – une profondeur suffisante pour englober toute la couche tout en réduisant au minimum le volume de déchets dangereux. Une mission sur mesure pour les fraiseuses WIRTGEN de type W 210i, toutes deux équipées d’un tambour de fraisage microfin de 1 008 pics, répartis sur une largeur de fraisage de 2 m.
Pour un tel travail de précision, un nivellement précis est de rigueur. Afin de respecter précisément la profondeur de travail, les grandes fraiseuses sont dotées du système moderne de nivellement automatique LEVEL PRO : le réglage en hauteur s’effectue par l’intermédiaire des colonnes de levage des trains de roulement avant et arrière, tous les trains de roulement étant couplés hydrauliquement. Si l’un des trains de roulement passe sur une bosse ou dans un creux, les autres trains de roulement compensent automatiquement la différence de niveau. Ce principe d’essieu quadruple oscillant permet de toujours adapter la machine au terrain rencontré.
À faible profondeur de fraisage, les machines n’utilisent qu’un seul de leurs deux moteurs, ce qui permet de faire d’énormes économies de carburant.
Dieter Klein, gérant DKS Gesellschaft für Fahrbahnsanierungen (Société spécialisée dans les travaux routiers)
Les deux grandes fraiseuses d’une puissance de 537 kW chacune ont fraisé l’enrobé avec une énorme vitesse d’avancement d’environ 25 m/min. Elles étaient suivies par une fraiseuse à froid encore plus grande, pratiquement aussi rapide : une W 250 avec une largeur de fraisage de 3,8 m. C’est elle qui, dans une deuxième opération, a enlevé le reste de la couche de roulement sur une épaisseur d’environ 3,5 cm. Précisons que ces fraiseuses à froid sont toutes trois entraînées par deux moteurs diesel. Le principe en est le suivant : le premier moteur sert d’entraînement pour tous les groupes de fonction travaillant en permanence, le deuxième moteur n’étant activé que si nécessaire.
L’un des principaux défis était de veiller à un réapprovisionnement suffisant en eau. L’eau est injectée dans le carter de fraisage pour éviter la poussière et refroidir les pics. Sur chacune des grandes fraiseuses, le refroidissement optimal des pics est assuré grâce à deux rampes d’arrosage séparées pulvérisant l’eau à une pression asservie à la charge ainsi qu’à une quantité d’eau réglable en continu. Pour les trois fraiseuses, 60 000 l d’eau au total ont été nécessaires tous les jours – une quantité hors-normes. Une fois les 103 000 m² de couche de roulement en enrobé enlevés en seulement quatre jours de travail, les finisseurs VÖGELE et le compacteurs HAMM ont entamé respectivement les travaux de pose et de compactage de la nouvelle couche de roulement.
Pour la pose de la nouvelle couche de roulement en enrobé, l’entreprise générale Juchem Asphaltbau a apporté à Büchel des engins de premier choix : deux finisseurs VÖGELE de type SUPER 2100-2 et SUPER 2100-3i, chacun équipé d’une table fixe SB 250 TV de 11,5 m de largeur. Afin d’assurer une pose en continu et une couche d’enrobé d’excellente qualité, un alimentateur VÖGELE a alimenté les deux finisseurs en enrobé. Le plus récent des deux finisseurs, le SUPER 2100-3i, venant juste d’être livré en mai à l’entreprise Juchem Asphaltbau, a été mis en oeuvre sur la base aérienne pour la première fois en combinaison avec une table fixe. Il lui a suffi d’une seule journée pour poser la couche de roulement sur la voie extérieure droite des 2,3 km de piste. Le deuxième jour, le SUPER 2100-3i et le SUPER 2100-2, chacun assisté d’un alimentateur VÖGELE, sont entrés en action.
Ces équipes de choc étaient réellement impressionnantes : les deux finisseurs ont réalisé en mode « chaud à chaud » la pose d’une couche en enrobé de 23 m de largeur au total, avec une avance de 2,5 à 4 m/min et sans joint central. Ce dernier point est particulièrement important pour la longévité de la partie centrale de la couche de roulement, qui constitue la zone la plus sollicitée de la piste de décollage et d’atterrissage. Ensuite, le SUPER 2100-3i accompagné d’un alimentateur a réalisé seul la surface d’enrobé de la voie extérieure gauche, également sur une largeur de pose de 11,25 m. Ainsi, les finisseurs et alimentateurs ont pu poser une couche d’enrobé de 46 m de largeur, présentant un dévers constant de 1,4 % et avec seulement deux véritables joints largement éloignés du centre.
L’ajout de rallonges hydrauliques nous permet de réaliser n’importe quelle largeur intermédiaire, même avec des tables fixes – une solution très pratique.
Markus Stumm, chef de chantier Juchem Asphaltbau GmbH & Co. KG
Un facteur de réussite essentiel pour la pose de grandes quantités d’enrobé est la coopération entre finisseur et alimentateur. Le chantier de Büchel a vu la mise en oeuvre non seulement d’un VÖGELE MT 1000-1 mais aussi d’un MT 3000-2i Power-Feeder ramené de Konz avec un SUPER 2100-2 par la société Werwie. Cet alimentateur haute performance convainc par son énorme capacité de réception d’enrobé : en incluant le finisseur, il peut avoir en réserve jusqu’à 40 t d’enrobé. La qualité dépend également pour une part essentielle de la régulation de l’espacement, robuste et fiable, entre finisseur et alimentateur. À cette fin, le VÖGELE PowerFeeder est doté d’un système composé de trois palpeurs laser individuels placés sur la face inférieure du convoyeur à bande. C’est ce qui permet de garder une distance constante entre l’alimentateur et le finisseur. La protection anticollision apporte une sécurité supplémentaire. En cas de risque de collision, ce système arrête le finisseur, évitant ainsi tout choc éventuel.
Les rallonges hydrauliques de VÖGELE permettent d’augmenter de 1,5 m la largeur de pose des tables fixes, comme la SB 250 TV. Cette technologie réunit les avantages des tables fixes et ceux des tables extensibles. En effet, les tables fixes, de conception très solide, ne travaillent plus uniquement sur de grandes largeurs, elles gagnent en flexibilité.
Tables fixes illustrent leurs points forts partout où il est nécessaire de réaliser des travaux sur de grandes largeurs de travail jusqu’à 18 m avec un profil exact.
Suivant les deux finisseurs VÖGELE, dix compacteurs HAMM ont pris en charge le compactage de haute qualité de la couche de roulement. Pour ce faire, Juchem et Werwie ont utilisé des compacteurs articulés de la série HD+ ou HD, avec des poids de service allant de 9 à 12 t – dont quatre compacteurs à billes oscillantes. Une des principales caractéristiques de la série HD+ est sans aucun doute l’excellente visibilité depuis la cabine. Rien, dans cette cabine entièrement vitrée, n’entrave la vue. Les conducteurs ont le chantier, leur zone de travail et les cylindres toujours bien dans leur champ de vision, ce qui contribue fortement au niveau de sécurité élevé des compacteurs.
« L’excellente visibilité est l’une des raisons pour laquelle les clients nous louent de préférence les compacteurs HAMM de la série HD+ », explique Matthias Beckmann, directeur de la flotte de location chez Werwie. Par ailleurs, les compacteurs grands et lourds des séries HD et HD+, mis en oeuvre sur le chantier de Büchel, sont connus pour leur énorme rendement surfacique, résultant de la combinaison entre larges cylindres de grand diamètre, entraînement puissant et système intelligent automatique d’inversion de la marche. S’ajoutent à cela les réservoirs diesel et eau largement dimensionnés qui permettent de travailler pendant toute la durée d’un poste sans devoir réalimenter les réservoirs. Ainsi, les compacteurs HAMM offrent des conditions idéales pour atteindre un maximum de productivité – et c’est une des raisons pour laquelle ils ont été mis en oeuvre sur la piste de Büchel.
Dans les compacteurs de la série HD+, le siège du conducteur peut se décaler jusqu’au bord extérieur de la cabine et pivoter de 90° des deux côtés.
Cette technique de compactage développée par HAMM est tout aussi avantageuse pour compacter les petites superficies, par exemple sur les ponts ou dans les parkings couverts, que les grandes superficies, comme les autoroutes ou les aéroports.
Un tiers des compacteurs déployés sur le chantier de Büchel étaient équipés d’un cylindre oscillant.
Une autre caractéristique essentielle de la série HD+ est la répartition particulièrement avantageuse du poids et de la charge. Cela est dû à l’articulation placée pratiquement au centre de la machine et à sa cinématique particulière. Le résultat en est une excellente stabilité de conduite. Et grâce à la répartition homogène du poids, les compacteurs HAMM de la série HD+ produisent très rapidement des surfaces parfaitement planes, ce qui est essentiel pour les couches de roulement. Outre la répartition de la charge, l’arrosage d’eau est également déterminant pour la qualité du compactage. C’est pourquoi la série HD+ de HAMM est équipée de pompes performantes permettant d’acheminer la quantité d’eau désirée vers les buses, avec précision et fiabilité. L’arrosage d’eau peut être contrôlé à tout moment puisque, grâce à la cabine panoramique et à la conception intelligente du châssis, le conducteur a toujours les rampes d’arrosage bien en vue. Le réglage de la quantité d’eau s’effectue confortablement depuis le poste du conducteur. Enfin, une répartition ingénieuse de l’eau dans deux réservoirs permet une répartition homogène du poids quel que soit l’état de fonctionnement.
Les énormes quantités d’enrobé requises en un temps minimum pour un projet d’une telle envergure – à savoir, 10 000 t en quatre jours sur le chantier de Büchel – ont été produites dans trois centrales d’enrobage BENNINGHOVEN du groupe. Pendant la mise en oeuvre parallèle des deux finisseurs, les centrales d’enrobage d’Ürzig et de Niederwörresbach produisaient environ 140 t/h chacune d’enrobé Splittmastix, et la centrale de Boppard environ 160 t/h. Les chefs des trois installations étaient en contact permanent pendant les quatre jours afin de fournir sans interruption la quantité d’enrobé requise aux deux finisseurs haute performance. Pour ce faire, une intervention simultanée de jusqu’à 50 camions a été nécessaire.
Une condition pour la réussite du projet était que l’enrobé produit dans chacune des trois centrales soit de qualité identique. C’est pourquoi la société Juchem a utilisé, sur les trois sites, des matières premières provenant des mêmes carrières, et a procédé à un grand nombre de contrôles. Outre la capacité, la technique des centrales d’enrobage était également décisive pour la qualité : « Nous avons utilisé sur les trois sites les tous derniers systèmes de commande BENNINGHOVEN. Nous pouvions ainsi régler les centrales avec précision et produire exactement l’enrobé requis. En même temps, les nouveaux automatismes assurent un mélange peu énergivore, ce qui permet de réduire le coût des consommables », explique Karl-Heinz Thiem, chef de poste.
Les centrales d’enrobage BENNINGHOVEN du groupe Juchem fonctionnent avec des brûleurs EVO JET de dernière génération.
Karl-Heinz Thiem assure la surveillance et le contrôle de la centrale d’enrobage BA 3000 de BENNINGHOVEN sur le site d’Ürzig, déjà installée en 1986. C’est l’une des premières centrales d’enrobage construites par BENNINGHOVEN. Déjà à l’époque, le petit dernier de la famille du WIRTGEN GROUP réalisait des concepts visionnaires, qui se distinguaient surtout par leur flexibilité. C’est pourquoi la centrale a pu être maintes fois dotée de nouvelles techniques ou enrichie – par exemple avec un nouveau système de commande.
Quand un brûleur BENNINGHOVEN fonctionne, il fonctionne. C’est la Mercedes des brûleurs !
Karl-Heinz Thiem, chef de poste d’Ürzig Juchem GmbH & Co. KG
Après deux semaines de travail intense avec les machines et les installations du WIRTGEN GROUP, Juchem a pu terminer son projet ambitieux, du fraisage au compactage, en respectant scrupuleusement les délais. Uwe Müller, chef de projet du maître d’ouvrage, Landesbetrieb Liegenschaften und Baubetreuung (LBB) de Rhénanie-Palatinat en Allemagne, s’est lui aussi montré entièrement satisfait de la réalisation des travaux dans les délais et des excellents résultats atteints : « Nous sommes tout à fait dans les temps, et la qualité des revêtements en enrobé est irréprochable. » La base aérienne, confiée pour deux semaines aux machines de construction, a donc pu reprendre son activité dans les délais.
Rouleau tandem avec deux cylindres vibrants
Poids | 9 220 kg |
Largeur de rouleau | 1 680 mm |
Catégorie de gaz d'échappement | EU Stage V / EPA Tier 4 |
Rouleau tandem avec un cylindre vibrant et un cylindre oscillant
Poids | 9 220 kg |
Largeur de rouleau | 1 680 mm |
Catégorie de gaz d'échappement | EU Stage V / EPA Tier 4 |
Rouleau tandem avec deux cylindres vibrants
Poids | 9 700 kg |
Largeur de rouleau | 1 680 mm |
Catégorie de gaz d'échappement | EU Stage V / EPA Tier 4 |
Rouleau tandem avec un cylindre vibrant et un cylindre oscillant
Poids | 9 460 kg |
Largeur de rouleau | 1 680 mm |
Catégorie de gaz d'échappement | EU Stage V / EPA Tier 4 |
Rouleau tandem avec cylindre vibrant et jeu de roues
Poids | 8 720 kg |
Largeur de rouleau | 1 680 mm |
Catégorie de gaz d'échappement | EU Stage V / EPA Tier 4 |
Rouleau tandem avec cylindre vibrant et jeu de roues
Poids | 8 960 kg |
Largeur de rouleau | 1 680 mm |
Catégorie de gaz d'échappement | EU Stage V / EPA Tier 4 |