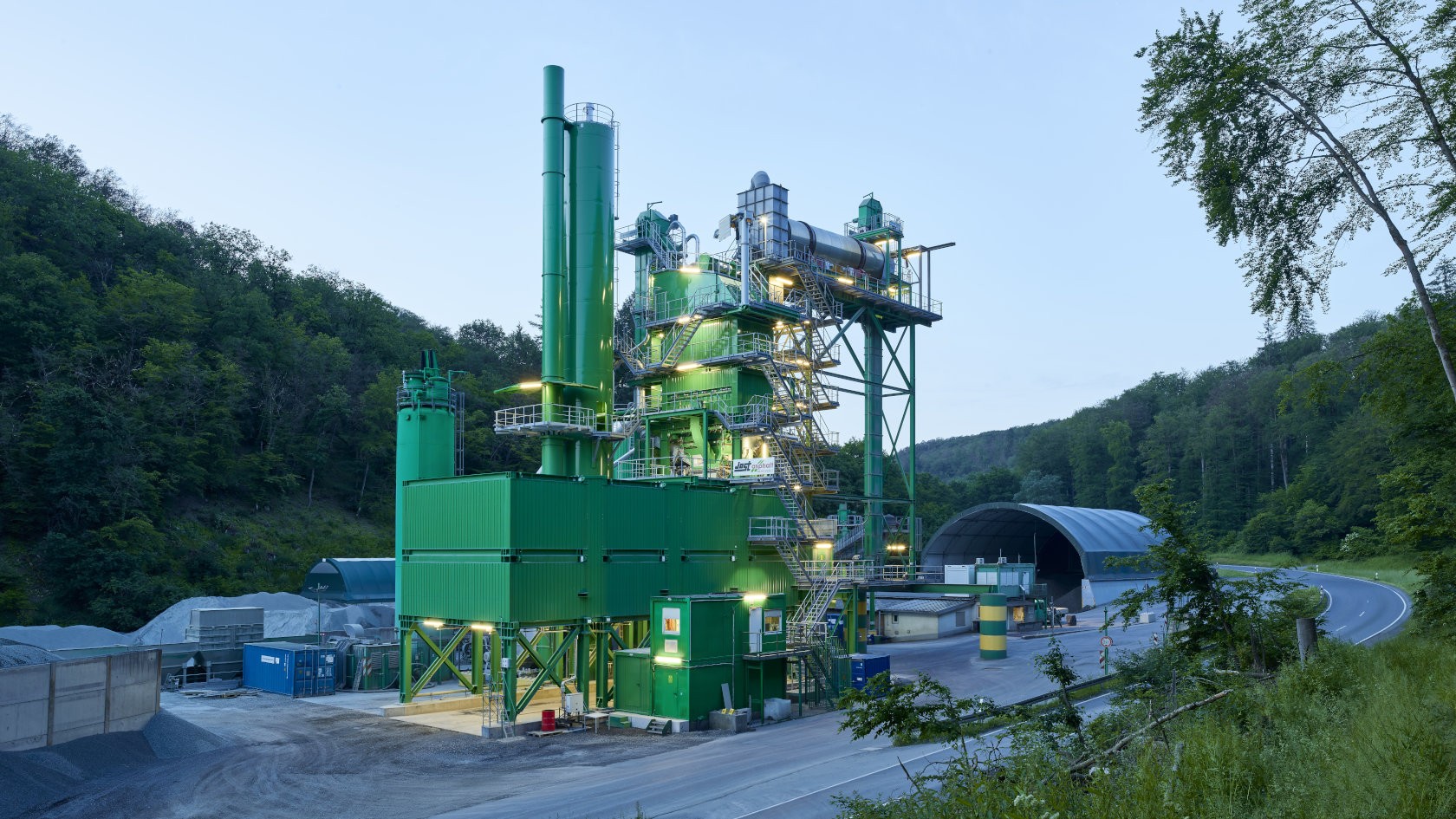
Braunfels (Taunus) | Allemagne
Les solutions de rétrofit de Benninghoven peuvent répondre à un large éventail d'exigences. Un projet dans la région du Taunus le met particulièrement en évidence : Ici, deux zones centrales de l’installation ont dû être entièrement remplacées dans un espace restreint et en tenant compte de plusieurs points fixes. Il s'agissait plus précisément de la tour de malaxage et de la section de séchage. En revanche, la centrale de recyclage et les autres composants devaient être conservés. L’« opération à cœur ouvert » était un défi majeur en termes de planification, de logistique et de montage, qui a été relevé par une équipe expérimentée de Benninghoven – en étroite coordination avec les clients.
Les dirigeants de Wilhelm Jost GmbH & Co. KG approchèrent Benninghoven avec la volonté initiale de vouloir augmenter la production de 200 t/h. La tour de malaxage existante, en particulier, devenait de plus en plus un « goulot d'étranglement ». L'entreprise de construction routière de la région du Taunus a développé cette activité avec succès au cours des 20 dernières années. La flotte d’installation de l'entreprise pose 80 % du matériau enrobé de l'usine à Braunfels même, et seul un cinquième est vendu.
Jost a décidé de travailler avec Benninghoven, même si l’installation provenant à l’origine d'un concurrent. « Cependant, nous entretenons une relation d'affaires depuis 15 ans. Tout a commencé par la mise à niveau d'un brûleur EVO JET », explique Bernd Jost, directeur général. « Ce brûleur fonctionne parfaitement depuis lors. La bonne réputation qui précède Benninghoven s'est confirmée à nos yeux. Notre collaboration ne m'a jamais déçu. » La liste des projets déjà réalisés ensemble comprend également des cuves de bitume mises à niveau, l'intégration des systèmes d’addition à froid et à chaud et le remplacement du système de commande de l'installation par un BLS 3000 de Benninghoven. « C'est pourquoi nous savions que notre partenaire répondrait également à nos attentes dans ce projet », déclare Bernd Jost.
« La bonne réputation qui précède Benninghoven s'est confirmée à nos yeux. Notre collaboration ne m’a jamais déçu. »
Bernd Jost, directeur général de Wilhelm Jost GmbH & Co. KG
D’anciens composants intelligemment intégrés : Vue de la centrale d'enrobage modifiée chez Wilhelm Jost GmbH & Co. KG à Braunfels dans la région du Taunus.
Lors des premières discussions sur le site de Jost, il est apparu que, outre la tour de malaxage, la section de séchage devait également être remplacée afin d'augmenter la production. En effet, les anciens silos à chaud pour le stockage de matière minérale blanche chauffée n'étaient que de 80 t. Avec la nouvelle technologie Benninghoven basée sur la TBA 4000, il y a maintenant 130 t dans sept compartiments, et la capacité de l'installation de criblage est de 290 t/h. Jost a doublé la capacité du silo de stockage d’enrobé à 440 t. Il est possible d'y stocker jusqu'à huit types de matériaux enrobés différents, dans deux des chambres même pour une période plus longue. Les livraisons sont ainsi bien plus flexibles.
La décision concernant la nouvelle tour de malaxage elle-même a également été prise pour le type d'installation TBA 4000. Grâce à un malaxeur de 4 t, Jost pourra à l'avenir produire jusqu'à 320 t/h de matériau enrobé et – comme c'est le cas pour Benninghoven – réaliser une grande variété de formulations. Grâce au tambour parallèle du système d'adjonction à chaud de Benninghoven, existant et maintenu en place, un taux de recyclage allant jusqu'à 70 % peut être réalisé. L'ajout dans le malaxeur du système de recyclage à froid permet même de recycler 30 % supplémentaires.
Photo : Travail sur mesure – l'un des plus grands défis pour l'équipe d'installation de Benninghoven était l'espace disponible extrêmement exigu. L’installation est située dans une vallée et juste à côté d'une route publique.
Le choix des nouveaux composants a été résolu très rapidement pour Jost. Après une visite de l'équipe de l'installation et des responsables à l'usine principale de Benninghoven à Wittlich, l'équipe a en effet pu tout voir et clarifier les questions. Les experts en planification du bureau technique de Benninghoven fournirent des conseils compétents.
La planification, en revanche, s'est avérée plus compliquée. Comme les composants et les zones existants de l'installation devaient être conservés, de nombreux points fixes ont dû être pris en compte, c'est-à-dire des conditions structurelles non modifiables autour desquelles les ingénieurs ont dû planifier la nouvelle tour de malaxage et la section de séchage. Pour cet espace de construction très limité, Benninghoven a également entrepris l'analyse structurelle pour la construction métallique de la centrale d’enrobage et du silo de stockage d’enrobé – y compris la détermination des charges de support pour les fondations en béton sur site et les profilés d'acier nécessaires.
Le plus grand obstacle était naturellement la centrale de recyclage avec son tambour parallèle à une hauteur de 30 m. Mais l'intégration des autres composants, à savoir l’unité de prédosage, le brûleur EVO JET, les silos de poudre de charbon et les cuves de bitume, y compris le tubage, a également été exigeante, tant en termes de planification que de montage. Un autre défi consistait à conserver la cabine de commande, y compris le conteneur de puissance, et à intégrer un conteneur supplémentaire. Les nouvelles armoires de commande des composants de la tour de malaxage, du silo de stockage d’enrobé, du tambour-sécheur et du dépoussiéreur ont été installées dans ces derniers. Les convertisseurs de fréquence pour l'exhausteur et le tambour-sécheur ont trouvé place dans un conteneur de puissance supplémentaire.
« La recette du succès de notre département Rétrofit est d'offrir un « pack complet zéro souci ». De la planification à la mise en service, nous prenons tout en charge. »
Achim Keller, Service commercial de Benninghoven
Avec un projet de rénovation aussi vaste et exigeant, rien ne garantit que le processus se déroulera sans heurts. Car les impondérables sont nombreux. Sur le chantier, certaines choses s'avèrent différentes de ce que l'on avait prévu au bureau. Il faut alors faire appel au talent d'improvisation et à la recherche de solutions. Néanmoins : « Avec des investissements importants, il est particulièrement important d'avoir un partenaire sur lequel on peut compter à 100 % », a déclaré Kai Philipps, chef de projet chez Jost.
Au vu de l'énorme complexité, l'équipe de Benninghoven a plus que justifié cette confiance : « Nous avons commencé à démonter les anciens composants en hiver. L'objectif était de pouvoir mettre la nouvelle technologie en service dans les six mois. Nous y sommes presque parvenus, nous n'avons eu que quelques jours de retard » se réjouit Christian Bode, chef de projet chez Benninghoven. « La recette du succès de notre département Rétrofit est d'offrir un « pack complet zéro souci ». De la planification au démontage et du montage à la mise en service, nous proposons une prise en charge totale à nos clients. Le projet de Braunfels a montré de manière impressionnante à quel point nous nous sommes bien préparés entre-temps. »
Le chef de poste de Jost, Frithjof Löhr, approuve : « Comme pour tous les projets d’envergure, il y a des moments où la situation est bloquée et où le cœur vous lâche momentanément. Mais dans l'ensemble, les gars de Benninghoven ont fait un excellent travail. » Une fois tous les tests de mise en service terminés, le moment tant attendu arriva enfin : les premiers camions de matériau enrobé de Wilhelm Jost GmbH & Co. KG se dirigèrent vers le chantier.
Photo : Transfert du matériau enrobé – la mise en service de la centrale d'enrobage modifiée s'est déroulée avec succès.
« Avec des investissements importants, il est particulièrement important d'avoir un partenaire sur lequel on peut compter à 100 %. »
Bernd Jost, directeur général de Wilhelm Jost GmbH & Co. KG