Remettre des centrales d‘enrobage existantes à niveau par rétrofit
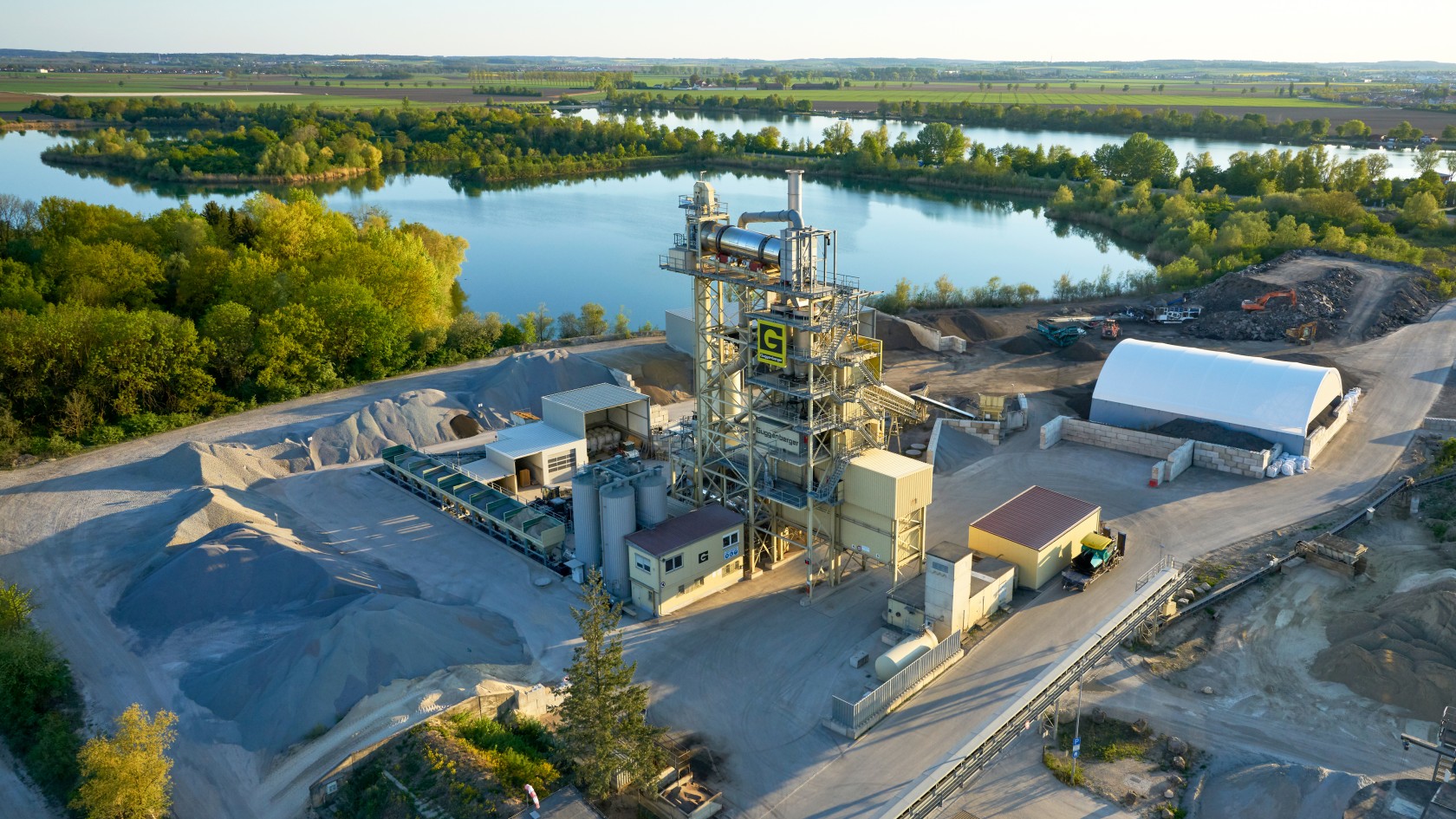
La durée de vie habituelle d‘une centrale d‘enrobage atteint facilement 20 à 30 ans, voire même plus. Durant cette période incroyablement longue, beaucoup de choses changent, par exemple les exigences en termes de formulations et de qualités d‘enrobé, de même que les exigences réglementaires que doivent satisfaire les exploitants pour obtenir l‘autorisation d‘exploiter. Benninghoven accompagne les clients et utilisateurs pour tous les défis de la modernisation grâce à un département dédié au rétrofit.
Paramètres pouvant changer au cours de la « vie » d’une centrale d’enrobage :
Les clients demandent de nouveaux enrobés de plus haute qualité qui exigent de la centrale d’enrobage des capacités d’adjonction spéciales. Les normes antipollution exigées par la loi sont plus strictes. La proportion d’adjonction de matériau de recyclage augmente afin de réduire les coûts des matières premières, mais uniquement pour les exploitants disposant de la technologie appropriée. Les réglementations relatives à la protection contre la poussière et le bruit (par exemple TA-Luft et TA-Lärm en Allemagne) à respecter pour conserver le droit d’exploiter sont plus strictes, souvent parce que les zones résidentielles viennent s’étendre jusqu’à la centrale d’enrobage qui était jusqu’alors isolée. Des combustibles alternatifs sont demandés pour le brûleur de la centrale d’enrobage.
Le rétrofit de Benninghoven modernise des installations de tous les fabricants
Les solutions de rétrofit permettant de moderniser des centrales d’enrobage existantes sont conseillées pour de nombreuses raisons et sont souvent plus avantageuses que d’investir dans une nouvelle construction. Dans les régions à forte densité de population, le rétrofit représente même quasiment la seule solution car il serait fastidieux et incertain d’obtenir une nouvelle autorisation administrative. Dans de nombreux pays, il n’est pas nécessaire de demander une nouvelle autorisation en cas de rénovation d’une installation existante. Pour tous les projets de rétrofit, Benninghoven s’avère être un partenaire compétent pour les exploitants de centrales d’enrobage, quel que soit le fabricant ayant installé la centrale à l’origine. Les clients profitent ainsi de l’expertise et de l’impartialité qui caractérisent Benninghoven.
« Le rétrofit proposé par Benninghoven constitue quasiment une solution clé en main », explique Markus Bühl, Area Sales Manager pour les produits Benninghoven dans la filiale du Wirtgen Group située à Augsbourg. Pour illustrer cette déclaration, prenons l’exemple du projet de rétrofit de la centrale d’enrobage de l’entreprise Guggenberger GmbH à Mintraching. Il s’agissait ici de remettre à niveau une centrale Benninghoven de type BA 4000. L’objectif était avant tout d’augmenter les performances et l’efficacité de l’installation. Pour cela, il fallait notamment remplacer le tambour de séchage et le brûleur. Il fut rapidement évident qu’aucun tambour standard ne conviendrait. Markus Bühl ramena ce challenge à l’usine mère de Benninghoven afin de concevoir une solution avec le bureau d’étude technique.
Solution de rétrofit complète du même fabricant
De la conception à la mise en œuvre technique jusqu’à la réalisation sur site : les experts Benninghoven des filiales du Wirtgen Group suivent le processus de rétrofit de la prise de contact jusqu’à la réception finale. Ils sont également en contact direct avec l’usine mère de Benninghoven. Cela s’avère très précieux pour les exploitants de centrales car chaque centrale d’enrobage est unique. De nombreuses solutions doivent être adaptées ou même créées de façon individuelle pour que la centrale soit préparée pour les exigences à venir. Pour que tout soit parfaitement ajusté à la fin, la procédure se divise en trois étapes : développement en commun d’un plan de rétrofit, examen et mise en œuvre techniques dans l’usine mère de Benninghoven, implémentation de la nouvelle technologie sur site.
Aborder les projets de rétrofit dès le début avec un plan
Chaque projet de rétrofit de Benninghoven commence par un rendez-vous sur place. Une équipe de la filiale du Wirtgen Group qui suit le client lui rend visite avec des experts compétents de Benninghoven. L’inventaire de la technologie existante de l’installation et toutes les modifications souhaitées sont consignés par écrit. Les manuels de planification de Benninghoven représentent un outil utile lors de cette étape. Lors de ce premier entretien, des photos de l’installation et des composants à remettre à niveau sont également prises.
Examen technique - élaboration d’une solution personnalisée
Suite au rendez-vous sur place à Mintraching, l’équipe du Wirtgen Group discuta des exigences de l’entreprise Guggenberger GmbH dans l’usine mère de Benninghoven. « Pour cette centrale, il y avait de nombreuses exigences pour lesquelles les solutions standards ne pouvaient pas nous aider », explique Jörg Genetsch, expert en technologie de séchage et de dépoussiérage dans le bureau d’étude technique de Benninghoven. « Mais nous y sommes habitués avec les projets de rétrofit et pouvons réaliser ces commandes de manière rentable, même pour le client. » Pour développer la solution optimale, Benninghoven a misé sur l’intelligence collective, c’est-à-dire sur le savoir-faire de toute l’équipe du bureau d’étude technique combiné à l’expérience des monteurs sur site. Le bureau d’étude technique de Benninghoven est en effet habitué à tirer plus de puissance de la technologie existante et surtout à y adapter des composants techniques existants à de nouveaux composants. « Nous étudions également les anciens composants sur place pour déterminer ce à quoi il faut faire attention et ce qui est à améliorer », précise M. Genetsch. Après la conception, les ingénieurs établissent les spécifications techniques et réalisent les dessins de disposition.
L’équipe du Wirtgen Group présente la solution technique globale au client et en discute avec lui jusqu’à ce que le projet soit validé. « Dès l’étude du projet, les professionnels Benninghoven nous ont montré qu’ils savaient exactement de quoi ils parlaient. Leur savoir-faire est impressionnant. C’est pourquoi nous avons su dès le début que nous étions entre de bonnes mains et que nous serions bien conseillés », indique Karl Weiß, responsable de production de la centrale d’enrobage de Guggenberger GmbH à Mintraching.
Le travail d’équipe peut commencer
Une fois que la planification du rétrofit et que tous les nouveaux composants ont été validés, ces derniers sont fabriqués dans l’usine mère de Benninghoven, puis transportés jusqu’au chantier. Souvent, le personnel de la centrale du client et les techniciens de service Benninghoven forment une équipe. Ce fut aussi le cas pour le projet de rétrofit à Mintraching. « Et cela avec un succès retentissant », se réjouit Thorsten Neidhöfer, l’un des monteurs de Benninghoven sur site.
Nouveau brûleur plus puissant EVO JET 3 pour trois combustibles
La centrale d’enrobage existante a été équipée d’une technologie Benninghoven moderne qui lui permettra de fonctionner de manière rentable et écologique durant de nombreuses années. Les pièces fondamentales sont ici le brûleur et le tambour de séchage. Le nouveau brûleur EVO JET 3 peut maintenant fonctionner avec trois et non plus deux combustibles (fioul, gaz liquéfié et charbon pulvérisé). Cela va rendre Guggenberger plus indépendant des fluctuations des coûts de l’énergie. Un nouveau dispositif de dosage du charbon pulvérisé a été installé et apporte des avantages essentiels en termes de fonctionnalité, de sécurité et de consommation de combustible suite à des adaptations de construction apportées spécifiquement pour Guggenberger. Le brûleur est en outre plus puissant et contribue ainsi à améliorer les performances globales de la centrale. Pour la production d’enrobés tels que le Splittmastix ou l’asphalte coulé, qui sont exclusivement fabriqués à partir de minéraux blancs, le rendement du séchage a augmenté de 140 t/h à 190 t/h.
Public Relations
Reinhard-Wirtgen-Straße 2
53578 Windhagen
Allemagne