Train d'installations composé des concasseurs à mâchoires MOBICAT MC 120i PRO et MC 110i EVO2, du broyeur à cône MOBICONE MCO 90i EVO2 et de l'installation de criblage MOBISCREEN MSC 953i EVO dans l'espace limité de la carrière.
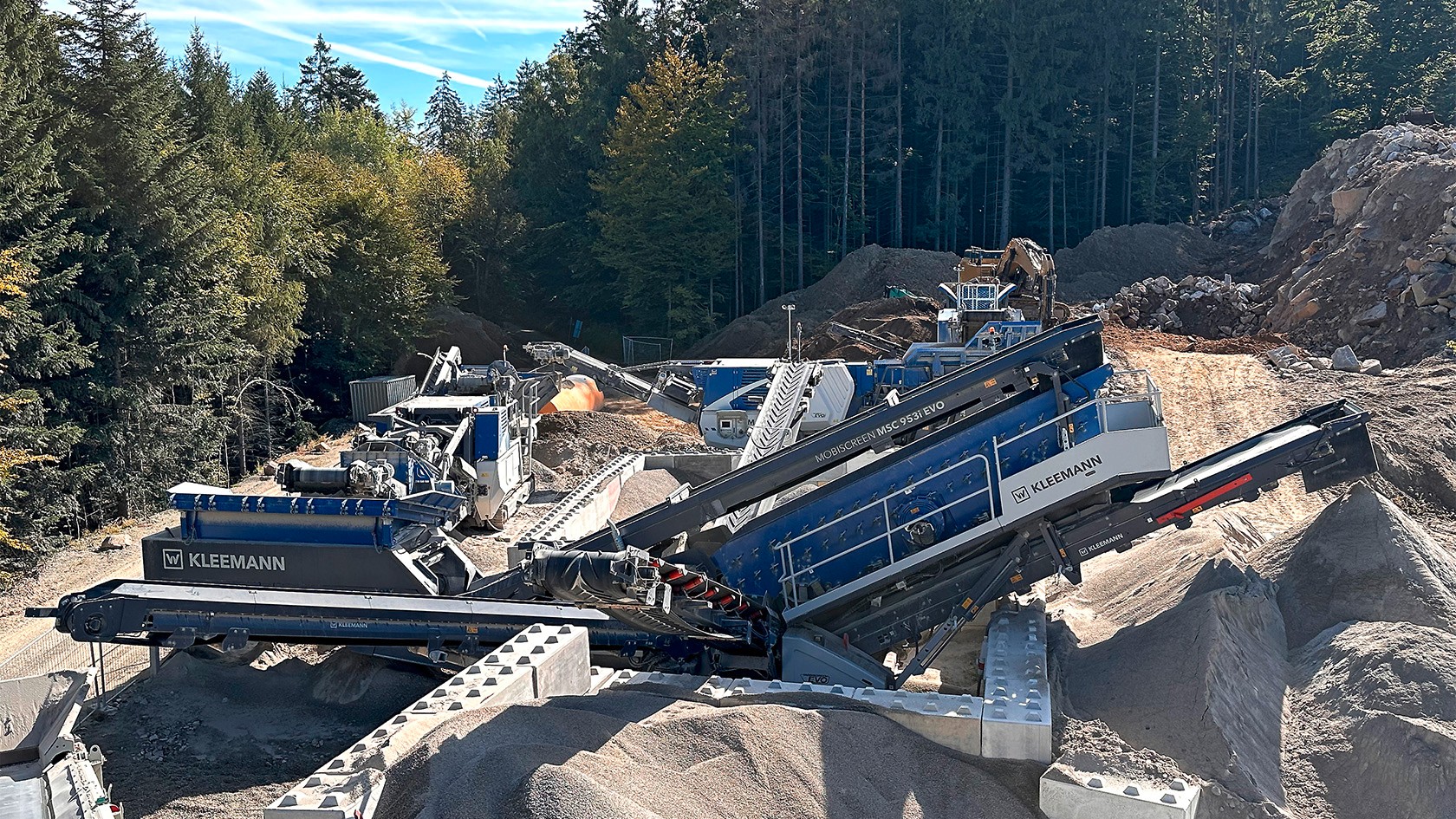
Une configuration parfaitement optimisée des installations valorise aujourd'hui de grandes quantités de déblais dans la forêt bavaroise
Dans une carrière à Winklarn dans la forêt bavaroise, la société Godelmann, le spécialiste des pavés, réduit du granite en gravillons fins. Non seulement le matériau du site est extraordinairement dur, mais l'espace disponible est également réduit. Après plusieurs séries de test, l'objectif est atteint avec une configuration quelque peu inhabituelle : deux concasseurs à mâchoires, un broyeur à cône plus une installation de criblage.
La société Godelmann de la ville bavaroise de Fensterbach est l'un des leaders de la fabrication de pavés en béton. La durabilité tient à cœur de l'entreprise tout au long du processus de fabrication, comme en témoigne l'attribution du prix allemand de la durabilité 2023. Il va de soi que l'entreprise accorde depuis longtemps une attention particulière à la transparence et à la durabilité de ses chaînes d'approvisionnement, à commencer par la production régionale de ses propres matières premières.
Train d'installations composé des concasseurs à mâchoires MOBICAT MC 120i PRO et MC 110i EVO2, du broyeur à cône MOBICONE MCO 90i EVO2 et de l'installation de criblage MOBISCREEN MSC 953i EVO dans l'espace limité de la carrière.
Lorsque l'occasion s'est présentée de traiter les déblais accumulés depuis de nombreuses années dans une carrière de granite de l'organisme régional des eaux et forêts, dans la forêt bavaroise, la direction de l'entreprise autour de Bernd Godelmann et du directeur technique Josef Regler a saisi cette chance. Jusqu'à présent, un tailleur de pierre de la région prélevait des pierres de taille dans la carrière pour fabriquer des produits en granite de grande taille, comme des plans de travail ou des pierres tombales. Cette extraction produit d'énormes quantités de résidus qui ne sont plus utilisables pour cette application, car infiniment durs et abrasifs. « Jusqu'à présent, aucune entreprise n'osait vraiment se lancer dans le traitement de ce matériau », raconte Andreas Wagner, expert Kleemann de Wirtgen Deutschland, « d'autant plus que le site de la carrière est loin d'être optimal. » Il est en effet situé en pleine forêt. L'accès est un challenge pour les appareils de grande taille et le site est extrêmement étroit.
L'expert Kleemann de Wirtgen Deutschland Andreas Wagner (à gauche) et le responsable technique de Godelmann Josef Regler (à droite) devant le train d'installations Kleemann.
« Nous avons dû faire de nombreux essais pour arriver au résultat d'aujourd'hui. Les techniciens Kleemann se sont vraiment beaucoup investis dans tout le processus, l'ont peaufiné et optimisé avec nous. Et à présent, nous avons trouvé une solution peu habituelle, mais parfaitement opérationnelle. »
Josef Regler, responsable technique chez Godelmann
Godelmann a vu dans cette carrière une opportunité de développer l'approvisionnement régional en matières premières. L'idée d'utiliser des déblais jusqu'ici inutilisés s'inscrit également dans la stratégie de durabilité de l'entreprise. Et les installations flexibles et mobiles de Kleemann sont peut-être la solution pour cette tâche hors du commun !
Après la prise de contact avec les techniciens de procédé de Kleemann, une longue série de tests a commencé. Aujourd'hui, les efforts déployés ont finalement abouti et un train d'installations Kleemann qui réduit comme souhaité le matériau dur en gravillons de taille 0-16 mm est en service dans la carrière. « Le département de technique des procédés de Kleemann a vraiment fait de l'excellent travail », selon Josef Regler. « Nous avons dû faire de nombreux essais pour arriver au résultat d'aujourd'hui. Les techniciens Kleemann se sont vraiment beaucoup investis dans tout le processus, l'ont peaufiné et optimisé avec nous. Et à présent, nous avons trouvé une solution peu habituelle, mais parfaitement opérationnelle. »
Les experts Kleemann ont tâtonné avec les techniciens de Godelmann en faisant de nombreux essais pour arriver à la configuration actuelle, en commençant par un concasseur à mâchoires MOBICAT MC 110i EVO2 plus un broyeur à cône MOBICONE MCO 90i EVO2, dans différentes configurations, sur différents sites : mais soit l'usure était trop importante, soit la consommation énergétique était trop élevée ou le temps nécessaire trop long. Rapidement, on s'est aperçu que les solutions conventionnelles ne permettaient pas d'obtenir l'objectif souhaité. La configuration classique – un concasseur à mâchoires, deux broyeurs à cône et en bout de chaîne une installation de criblage – s'est également avérée non praticable.
Dans la forêt bavaroise, des gravillons de qualité sont obtenus en réduisant du granite dur et fortement abrasif.
Au final, l'entreprise a décidé d'intégrer un MOBICAT MC 120i PRO dans le processus. Il réduit dans un premier temps le matériau d'alimentation massif d'une taille de 0-600 mm à 0–200 mm. Outre de bonnes performances, cette installation offre l'avantage d'un entraînement diesel-électrique. Ainsi, elle fournit l'énergie pour l'installation de criblage mobile MOBISCREEN MSC 953i EVO, en bout de train, ce qui abaisse la consommation de carburant globale. En plus, le MC 120i PRO peut être utilisé ailleurs, avec une infrastructure adaptée, en mode entièrement électrique et localement sans émission – un argument important pour l'entreprise Godelmann axée sur la durabilité.
En aval du premier concasseur à mâchoires se trouve un deuxième concasseur, le MOBICAT MC 110i EVO2, qui réduit la taille d'alimentation 0–200 mm en 0–60 mm et prépare ainsi le traitement avec le broyeur à cône MOBICONE MCO 90i EVO2. Celui-ci produit quant à lui le produit principal 0–16 mm. L'installation de criblage en bout de chaîne sépare les produits finaux 0–2, 2–5, 5–11 et 11–16 mm.
« Tout le process de l'installation est surveillé en permanence par l'interconnexion. C'est un avantage certain qui sécurise l'ensemble du cycle de production », selon Christian Pröls, responsable d'exploitation de la carrière. « Mais ce sont aussi de nombreux détails, comme la commande intuitive via SPECTIVE et la bonne accessibilité de tous les composants importants, qui font que tout fonctionne parfaitement. » Le responsable technique Josef Regler ajoute : « Le plus important est d'avoir reçu une assistance si complète de la part de notre interlocuteur Andreas Wagner et des techniciens de l'usine Kleemann. Ils ont compris notre objectif, ont tout testé et contrôlé avec nous jusqu'à atteindre la configuration idéale pour le process. »