Tecnica di frantumazione
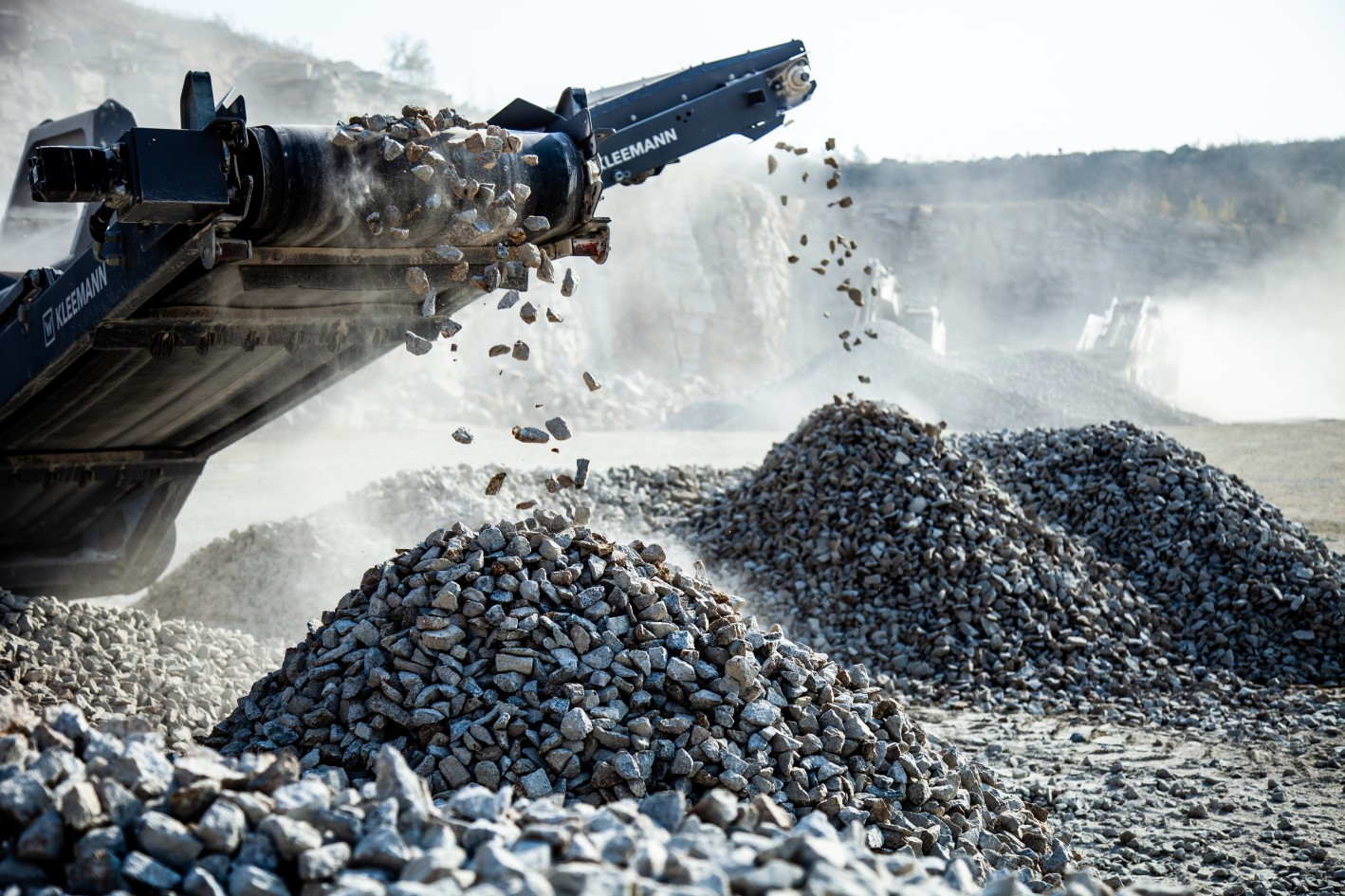
Materiale in entrata, prodotto finale necessario ed economicità influiscono sulla scelta della tecnica di frantumazione.
L'estrazione di tipi di roccia naturali è collegata all'uso di macchine in grado di frantumare il materiale con elevata resistenza a compressione, in modo mirato ed efficace. I frantoi a mascelle sono ideali per l’uso impegnativo in cave e sono utilizzati prevalentemente come frantoi primari.
I frantoi a mascelle lavorano applicando il principio della triturazione per compressione. La triturazione del materiale avviene nella fessura a forma conica tra la mascella di frantumazione fissa e la mascella mossa da un albero a eccentrico. Il movimento ellittico frantuma il materiale, che cade per gravità. Questo processo continua finché il materiale non diventa più piccolo della fessura di frantumazione.
L'energia di frantumazione agisce sul materiale di frantumazione da lavorare, con grandi forze e a bassa velocità. Il nome frantoio a mascelle deriva dalla mascelle necessarie alla frantumazione e dal movimento di "masticazione".
I frantoi a mascelle sono utilizzati per la frantumazione grossolana e preliminare di rocce fragili, di media durezza e dure. Vengono usati più frequentemente come frantoi primari.
Più raramente, i frantoi a mascelle sono in grado di produrre un prodotto finale a norma. In alcune attività di riciclaggio, in abbinamento a piccoli frantoi a mascelle, è possibile produrre strati di pietrisco per percorsi e strade secondarie.
I frantoi a cono sono utilizzati con la pietra naturale da semidura a dura e abrasiva, ma anche per il trattamento di materie prime nelle applicazioni delle attività di estrazione. Nel 2° e 3° stadio di frantumazione, i frantoi a cono forniscono una pezzatura finale cubica a norma.
I frantoi a cono sono disponibili in diverse grandezze, versioni e per differenti applicazioni.
Nei frantoi a cono, la triturazione avviene mediante compressione, in una fessura tra fodera del frantoio e cono di frantumazione che si apre e si chiude continuamente. L'apertura e la chiusura sui lati opposti del vano di frantumazione avviene in contemporanea.
I frantoi a cono sono disponibili in diverse varianti costruttive. Per quanto concerne i frantoi a cono usati da KLEEMANN, l’asse del frantoio è inserito a forza nel telaio inferiore. Il sostegno del cono di frantumazione è supportato da un'unità di trasmissione eccentrica. Mediante la rotazione dell’unità di trasmissione, la fessura tra cono di frantumazione e fodera del frantoio si apre perimetralmente. La pezzatura da produrre viene variata mediante il sollevamento/abbassamento della fodera del frantoio.
I frantoi a cono e rotanti sono utilizzati principalmente quando, a motivo di un'elevata resistenza alla compressione del materiale di frantumazione, una frantumazione ad urto non è più possibile o l'ammontare dei costi d’usura non è più economicamente conveniente a causa dell'abrasività della roccia.
Per ragioni strutturali, i frantoi a cono e rotanti sono limitati per quanto concerne le dimensioni del materiale in entrata e il rapporto di frantumazione ottenibile.
Sugli impianti mobili, i frantoi a cono sono utilizzati principalmente per la frantumazione secondaria nello stadio di frantumazione secondario e terziario.
I frantoi rotanti si differenziano dai frantoi a cono a motivo del loro tipo di costruzione.
Diversamente dal frantoio a cono, che è dotato di un albero fisso, sul quale ruotano l'unità di trasmissione e il supporto del cono, il frantoio rotante possiede un albero principale movibile idraulicamente in direzione verticale, sul quale è calettato a caldo e in modo fisso il supporto del cono. L'albero è supportato assialmente all'estremità inferiore su un cuscinetto reggispinta, che a sua volta si trova sul pistone di regolazione. La regolazione della fessura di frantumazione è effettuata mediante il sollevamento e l'abbassamento del pistone di regolazione e quindi anche dell’albero principale. All'estremità superiore vengono immesse le forze orizzontali di frantumazione nella parte superiore del frantoio, attraverso il cuscinetto di testa integrato in una traversa, la cosiddetta "Spider".
Per ragioni strutturali, l'altezza di un frantoio rotante è in genere chiaramente maggiore rispetto a quella di un frantoio a cono comparabile.
I potenti tuttofare
Sia in cava che in cantiere – con i frantoi ad urto la pietra viene efficacemente frantumata affinché forma e distribuzione della pezzatura e pulizia soddisfino le severe normative relative agli inerti per calcestruzzo e asfalto. Oltre ad un'eccellente qualità del prodotto, gli impianti di frantumazione ad urto raggiungono anche portate considerevoli.
Diversamente dalla triturazione per compressione, in queste macchine la frantumazione avviene per effetto di urti e colpi. Il materiale viene prelevato, accelerato e scagliato violentemente da un rotore dotato di grande velocità di rotazione contro elementi fissi, le corazze. Da qui il materiale ricade nel circuito del rotore. Così il materiale viene continuamente frantumato, fino a raggiungere una dimensione che gli permetta di passare attraverso la fessura tra rotore e corazze.
Il vero e proprio processo di frantumazione avviene mediante il contatto della roccia con i martelli e le corazze. Inoltre avviene una frantumazione a causa del contatto reciproco delle pietre.
I frantoi ad urto sono utilizzati come frantoi primari e secondari. Come frantoi primari, i frantoi ad urto trovano la loro applicazione nel calcare, soprattutto dove è richiesta un'elevata percentuale di materia fine, una buona cubicità ed angolarità del pietrisco e una elevata potenza.
Nel moderno riciclaggio di calcestruzzo, asfalto e rifiuti edili, oggigiorno non si può più fare a meno di essi, considerata la loro elevata potenza e l’eccellente qualità della pezzatura finale. Diversamente dalla triturazione per compressione, essi sono in grado di estrarre ferri d’armatura in modo pulito dal calcestruzzo e quindi di generare un prodotto finale ampiamente senza ferro.
Come frantoi secondari, essi vengono sovente utilizzati dopo i frantoi a mascelle per la produzione di prodotti finali a norma.
Normalmente, si parla di mulini a proiezione quando il prodotto finale deve avere una dimensione della pezzatura soltanto fino a 10 millimetri. I mulini a proiezione vengono sovente utilizzati come frantoi secondari nel terzo e quarto stadio di frantumazione, perché le dimensioni del materiale in entrata devono essere opportunamente piccole.