Tecnologia de britagem
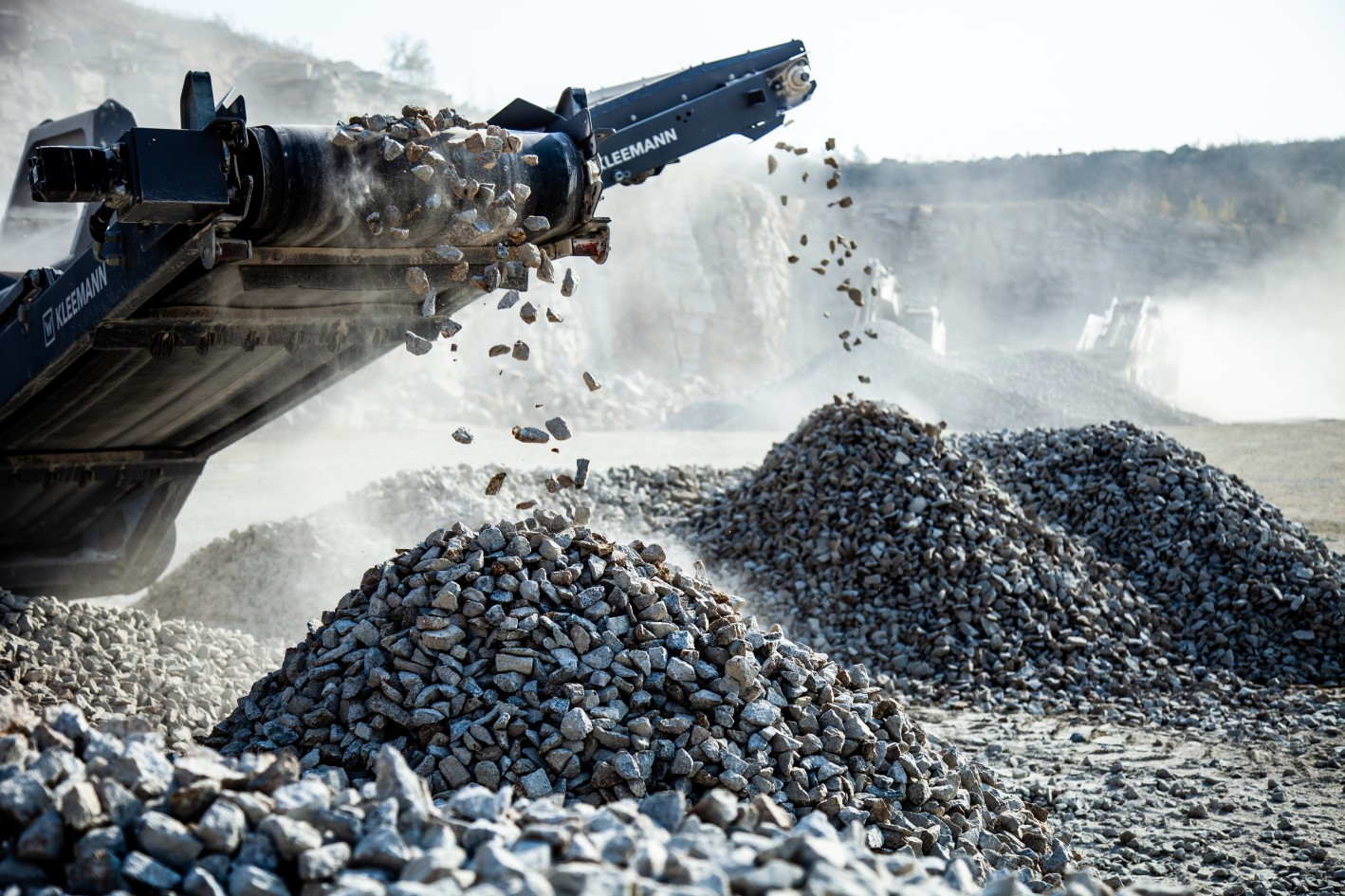
Material de carregamento, produto final necessário e rentabilidade influenciam a seleção da tecnologia de britagem.
A extração de tipos de pedra natural está associada ao uso de máquinas que trituram, específica e eficazmente, materiais com alta resistência à pressão. Os britadores de mandíbulas se adaptam perfeitamente em condições difíceis em pedreiras e são usados, principalmente, como britadores primários.
Os britadores de mandíbulas trabalham segundo o princípio da trituração por pressão. A trituração do material britado acontece na fenda em forma de cunha, entre a mandíbula fixa e a mandíbula móvel deslocada por um veio excêntrico. O produto é esmagado devido ao movimento elíptico e cai devido à força da gravidade. Isso continua até que o material fique menor do que a fenda de britagem ajustada.
A energia de trituração atua sobre o produto triturando com altas forças e velocidade baixa. O nome Britador de mandíbulas deriva das mandíbulas de britagem necessárias para a trituração e do movimento de mastigação.
Os britadores de mandíbulas são usados para a trituração grosseira e trituração prévia de rochas frágeis, semiduras e duras. São, maioritariamente, usados como britadores primários.
Os britadores de mandíbulas raramente conseguem gerar um produto final de acordo com as normas. Em algumas aplicações de reciclagem, pequenos britadores de mandíbulas podem ser usados para produzir camadas de base de brita para a construção de rodovias e estradas secundárias.
Os britadores de cone são usados em rocha natural de dureza média a alta, bem como abrasiva e no tratamento de matérias-primas em aplicações de mineração. No 2º e 3º estágio de britagem, os britadores de cone fornecem as granulações finais cúbicas de acordo com as normas.
Há britadores de cone de diversos tamanhos, versões e para diferentes aplicações.
Nos britadores de cone, a trituração é feita por pressão em uma fenda de britagem abrindo e fechando continuamente, entre o manto de britagem e o cone de britagem. A abertura e fechamento ocorre ao mesmo tempo em lados opostos do compartimento de britagem.
Há britadores de cone em diversas formas construtivas. Nos britadores de cone usados pela KLEEMANN, o eixo de britagem é pressionado na estrutura inferior. O suporte do cone de britagem é transferido para uma unidade de acionamento excêntrica. Através da rotação da unidade de acionamento, a fenda entre o cone de britagem e o manto de britagem abre de forma circunferencial. O grau de granulação a ser produzido se altera, levantando e baixando o manto de britagem.
Os britadores de cone e os britadores giratórios são usados, principalmente, quando já não é possível uma trituração por impacto devido a alta resistência à pressão do produto a ser triturado ou quando a abrasividade da pedra representa custos de desgaste tão altos que deixam de ser economicamente justificáveis.
Devido a seu design, os britadores de cone e os britadores giratórios são limitados quanto à dimensão do carregamento e ao grau de trituração alcançável.
Nas instalações móveis, os britadores de cone são usados, principalmente, para pós-britagem no nível de trituração secundário e terciário.
Os britadores giratórios se distinguem devido a sua forma construtiva de britadores de cone.
Contrariamente ao britador de cone, que dispõe de um veio fixo, sobre o qual a unidade de acionamento e o suporte do cone giram, o britador giratório possui um eixo principal hidraulicamente móvel no sentido vertical, no qual o suporte do cone está bem firme. O veio está apoiado axialmente na extremidade inferior, em um mancal axial que, por sua vez, é deslocado no êmbolo de deslocação. O ajuste da fenda de britagem é feito levantando e baixando do êmbolo de deslocação e, assim, também o veio principal. Na extremidade superior, as forças de britagem horizontais são transferidas para a parte superior do britador, através do mancal superior, que está integrado em uma barra transversal, a chamada "Spider".
Devido a seu design, a altura de um britador giratório é, geralmente, significativamente maior do que a de um britador giratório comparável.
As plantas multifuncionais potentes
Seja na pedreira ou na obra – com britadores de impacto a pedra é triturada de forma eficiente para que o formato do grão, a distribuição granulométrica e a limpeza correspondam aos rigorosos padrões das normas para agregados de concreto e de asfalto. As plantas de britagem de impacto atingem não só uma qualidade de produto de primeira classe como também capacidades produtivas notáveis.
Ao contrário da trituração por pressão, o britador de impacto trabalha segundo o princípio da trituração por impacto e por golpe. Neste processo, o material britado é colhido por um rotor em movimento rápido, muito acelerado e projetado contra uma parede de impacto fixa, os braços oscilantes de impacto. A partir daí, volta a cair para dentro do alcance de impacto do rotor. Desta forma, o material britado é britado várias vezes até que possa passar pela fenda entre o rotor e os braços oscilantes de impacto.
O verdadeiro processo de britagem ocorre quando a rocha entra em contato com as travessas de impacto e os braços oscilantes de impacto. Além disso, ocorre uma trituração através do contato das rochas entre si.
Os britadores de impacto são usados como britadores primários e secundários. Como britadores primários, os britadores de impacto são usados em pedra calcária; principalmente quando são necessárias altas proporções finas de material, boa cunicidade e angularidade, bem como alto desempenho .
Graças a seu alto desempenho e excelente qualidade do produto final, são hoje indispensáveis para a reciclagem moderna de concreto, asfalto e resíduos de edifícios. Contrariamente à trituração por pressão, são capazes de remover impecavelmente aço reforçado do concreto e, assim, produzir um produto final, em grande parte, isento de ferro.
Como britadores secundários, são frequentemente usados depois de britadores de mandíbulas, para a produção de produtos finais de acordo com as normas.
Os moinhos de impacto, normalmente, são usados quando se pretende produzir um produto final que só deve ter uma granulação de até aprox. 10 milímetros. Frequentemente, os moinhos de impacto são usados como pós-britadores no terceiro ou quarto estágio de britagem, pois as dimensões de carregamento devem ser suficientemente pequenas.