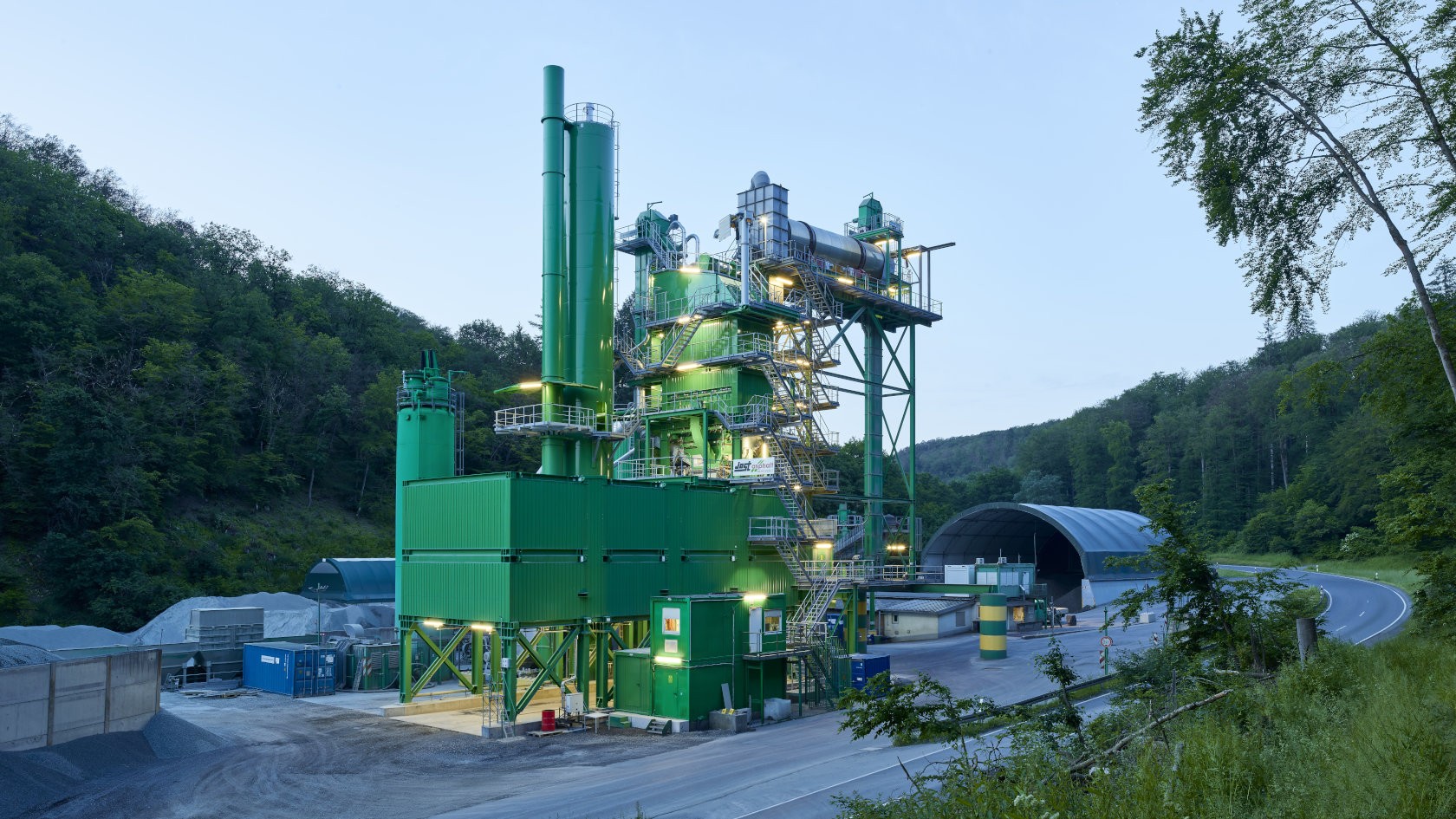
Braunfels (Taunus) | Alemanha
As soluções Retrofit da Benninghoven têm capacidade para cumprir uma ampla variedade de requisitos. Isso foi particularmente evidente em um projeto realizado em Taunus: o objetivo era realizar a substituição completa de duas áreas centrais da usina, em condições de espaço limitadas e tendo em consideração vários pontos fixos. Mais concretamente, as áreas a substituir eram a torre de mistura e o trajeto de secagem. Em contrapartida, havia o objetivo de preservar a usina de reciclagem e outros componentes. A “operação de coração aberto” foi um enorme desafio em termos de planejamento, logística e montagem. Porém, esse desafio foi enfrentado por uma equipe experiente da Benninghoven — em estreita coordenação com os clientes.
Os responsáveis da Wilhelm Jost GmbH & Co. KG contataram a Benninghoven com a intenção inicial de um aumento da atual produção de 200 t/h. A torre de mistura existente, em particular, estava se tornando cada vez mais em um gargalo de produção. Durante os últimos 20 anos, a empresa de construção de estradas da região de Taunus conseguiu um desenvolvimento positivo dessa situação. A própria frota de pavimentação da empresa aplica 80% do material de mistura da usina em Braunfels; apenas um quinto é vendido.
Jost decidiu colaborar com a Benninghoven, apesar de a usina ser originalmente de um concorrente. “Todavia, mantemos uma relação comercial há 15 anos. Tudo começou com a retroatualização de um queimador EVO JET”, referia o Diretor executivo Bernd Jost. “Esse queimador tem funcionado na perfeição desde então. A excelente reputação da Benninghoven ficou assim comprovada. A colaboração nunca me decepcionou”. A lista de projetos já realizados em conjunto também inclui depósitos de betume retroatualizados, a integração dos sistemas de adição de reciclagem a frio e a quente e a substituição do comando da usina por um BLS 3000 da Benninghoven. “É por isso que tínhamos a maior confiança de que nosso parceiro também atenderia nossas expectativas nesse projeto”, diz Bernd Jost.
“A excelente reputação da Benninghoven ficou assim comprovada. A colaboração nunca me decepcionou.”
Bernd Jost, Diretor executivo da Wilhelm Jost GmbH & Co. KG
Componentes antigos, integrados de forma inteligente: vista da usina de asfalto renovada da Wilhelm Jost GmbH & Co. KG em Braunfels, na região de Taunus.
Durante as primeiras reuniões na Jost, ficou claro que, além da torre de mistura, também o trajeto de secagem teria que ser substituído para possibilitar um aumento da produção. Isso porque o antigo silo de armazenamento quente para o armazenamento de mineral branco aquecido tinha uma capacidade de apenas 80 t. Com a nova tecnologia Benninghoven baseada na TBA 4000, sete compartimentos possuem agora 130 t e a produção da instalação de filtração é de 290 t/h. Jost duplicou a capacidade do silo de carregamento para 440 t. Nele, podem ser armazenados até oito tipos diferentes de materiais de mistura; em duas das câmaras, esses materiais podem até mesmo ser armazenados por um período de tempo mais prolongado. Isso permite uma maior flexibilidade de fornecimento.
A decisão pela nova torre de mistura recaiu também sobre a usina do tipo TBA 4000. Graças a um misturador de 4 toneladas, a Jost poderá produzir até 320 t/h de material de mistura no futuro e — tal como tem vindo a ser característico da Benninghoven — produzir uma ampla variedade de fórmulas. Graças ao tambor paralelo do sistema de adição a quente existente e preservado pela Benninghoven, é possível alcançar uma taxa de reciclagem de até 70%. Com o sistema da adição de misturador de reciclagem a frio, continua sendo de até 30%.
Imagem: Trabalho personalizado — um dos maiores desafios para a equipe de montagem da Benninghoven foram as condições de espaço extremamente limitadas. A usina está localizada em um vale, bem próximo a uma estrada pública.
A seleção dos novos componentes foi rapidamente solucionada. Essa rapidez também foi possível graças a uma visita da equipe da usina e dos responsáveis à sede da Benninghoven em Wittlich, que permitiu obter uma ideia geral e onde houve também espaço para esclarecer dúvidas. A consultoria competente foi fornecida pelos especialistas em planejamento do departamento técnico da Benninghoven.
Porém, o planejamento acabou se tornando ainda mais complicado. Uma vez que os componentes e áreas existentes da usina tiveram que ser preservados, numerosos pontos fixos tiveram que ser tidos em consideração, nomeadamente, condições estruturais imutáveis em torno das quais os engenheiros tiveram que planejar a nova torre de mistura e o trajeto de secagem. Tendo em consideração esse espaço de construção extremamente limitado, a Benninghoven também realizou a análise estrutural para a construção metálica da usina de asfalto e do silo de carregamento — incluindo a determinação das cargas de apoio para as fundações em concreto por parte da empresa construtora e os perfis em aço necessários.
O maior obstáculo foi naturalmente a usina de reciclagem, com seu tambor paralelo a 30 m de altura. Mas a integração dos outros componentes, nomeadamente, o sistema de pré-dosagem, o queimador EVO JET, os silos de carvão pulverizado e os depósitos de betume, incluindo a tubagem, também foi um processo exigente — tanto em termos de planejamento quanto de montagem. A preservação da cabine de comando, incluindo o contêiner do quadro de distribuição e a integração de um contêiner adicional também provou ser um desafio. Nesses contêineres, foram instalados os novos quadros de distribuição de componentes para a torre de mistura, o silo de carregamento, o tambor de secagem e a unidade de despoeiramento. Os conversores de frequência para o exaustor e o tambor de secagem estavam situados em um contêiner adicional do quadro de distribuição.
“A receita para o sucesso de nossa Divisão de Retrofit consiste em oferecer um ‘pacote completo e sem complicações’. Desde o planejamento até ao comissionamento, oferecemos produtos chave na mão.”
Achim Keller, Vendas Benninghoven
Com um projeto de Retrofit tão complexo e exigente, não é possível garantir um processo totalmente isento de problemas. As incertezas são enormes. É provável que alguns aspetos considerados no escritório se revelem distintos no canteiro de obras. E é por esse motivo que é necessário um talento para a improvisação e uma abordagem orientada para as soluções. Apesar disso: “Com investimentos significativos, é especialmente importante ter um parceiro em que se possa confiar a 100%”, referia Kai Philipps, Gerente de projeto da Jost.
Tendo em conta a enorme complexidade, a equipe da Benninghoven justificou plenamente essa confiança: “Iniciamos a desmontagem dos componentes antigos no inverno. O objetivo era poder comissionar a nova tecnologia no prazo de seis meses. O prazo proposto somente foi ultrapassado em alguns dias”, declarou Christian Bode, Gerente de projeto da Benninghoven, com grande satisfação. “A receita para o sucesso de nossa Divisão de Retrofit consiste em oferecer um ‘pacote completo e sem complicações’. Desde o planejamento, passando pela desmontagem e montagem, até ao comissionamento, oferecemos aos clientes produtos chave na mão. O projeto em Braunfels mostrou nossa coordenação atual de forma impressionante.”
O mestre em mistura da Jost — Frithjof Löhr — também concordou: “Como em todos os grandes projetos, existem momentos de dificuldade que nos provocam algum receio. Contudo, de um modo geral, o pessoal da Benninghoven fez um excelente trabalho”. Quando todos os testes de comissionamento ficaram concluídos, o momento mais esperado havia finalmente chegado: os primeiros caminhões de materiais de mistura da Wilhelm Jost GmbH & Co. KG partiram para o canteiro de obras.
Imagem: Entrega do material de mistura — o comissionamento da usina de asfalto renovada foi concluído com sucesso.
“Com investimentos significativos, é especialmente importante ter um parceiro em que se possa confiar a 100%.”
Bernd Jost, Diretor executivo da Wilhelm Jost GmbH & Co. KG