An investment with future.
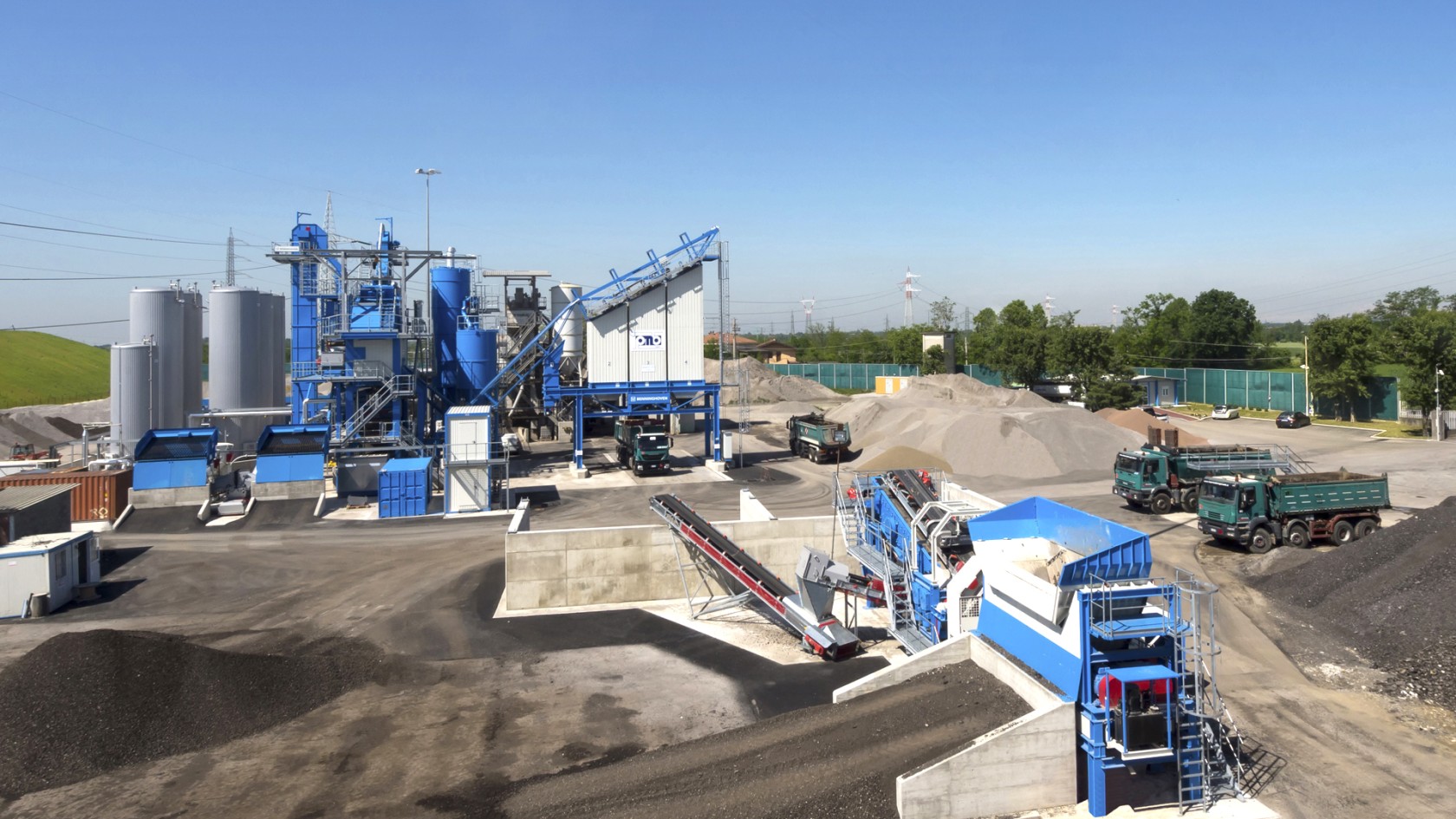
It is the first BENNINGHOVEN plant to produce asphalt in Italy: a TBA 3000 is improving productivity and flexibility for its owner, PMB s.p.a.
The city of Bergamo is known throughout Italy for its thriving industry, with the production of build-ing materials as one of the most important fields. The latest innovation in this segment is a recently acquired asphalt mixing plant from BENNINGHOVEN. And it’s something of a sensation. The type TBA 3000 is the first ever that BENNINGHOVEN has delivered to Italy, with the market being dominated by local suppliers. So what made the difference? “Our machine pool comprises 20 WIRTGEN milling machines, VÖGELE pavers and HAMM rollers. That’s why we have so much confidence in the WIRT-GEN GROUP. Once we had visited the BENNINGHOVEN headquarters and looked at the performance characteristics, we were fully convinced this was the right choice.“ This is how the partners of PMB s.p.a, Angelo Legrenzi, Mauro Bergamelli and Matteo Bergamelli, explain their investment in technol-ogy “made in Germany”.
The transportable BENNINGHOVEN type TBA asphalt mixing plants are characterized by their modular design, a large performance range, the possibility of adding more than 70% of RAP material, high robustness and the wide range of options. These features make the acquisition of a type TBA 3000 plant a strategic decision for PMB s.p.a., since it allows the company to boost its productivity, gain flexibility with regard to new market requirements and significantly improve eco-friendliness.
The TBA 3000 of the Italian contractor PMB is equipped with a 3,000kg mixer and guarantees a mix-ing output of 240t/h. Plants of this type are typically designed to be extremely robust, allowing them to be installed even in earthquake zones and making them resistant to high wind loads. Even so, their modularity and the preinstalled cabling designed for rapid connection means that each TBA is easy to transport and install speedily at another location.
Specializing in asphalt production, “Produzione Materiali Bituminosi” — or PMB s.p.a. for short — was founded in 1980 as a joint venture between three companies that had already been actively involved in this field since the 1950s. PMB operates two asphalt mixing plants in the immediate vicinity of the A4, one of the busiest motorways in Europe. The need to replace one of these plants was used as an opportunity to upgrade the technology for the future.
Two central components are responsible for the high portion of RAP material that can be used: the upstream stationary granulator SBRG 2000 and the multivariable RC feed system. The innovative BENNINGHOVEN granulator crushes the reclaimed asphalt particularly gently, preserving the grain structure. In the asphalt mixing plant these RAP granules are delivered “cold” into the mixer by means of a multivariable feed system. The procedure is as follows: a space-saving elevator delivers the granules to the mixing tower. The defined feed quantity is delivered to the mixer in small quanti-ties. This prevents shocks caused by steam expansion, thus protecting the plant and minimizing maintenance.
As well as the recycling technologies, PMB attaches great importance to diversity: “We want to offer our customers the greatest possible range of asphalt grades. That’s why we opted for multiple bi-tumen tanks — not least because it enables us to store modified bitumen,” says Angelo Legrenzi of PMB. Here too, BENNINGHOVEN offer an innovative solution: in the tanks, the 160 — 180°C hot bitu-men’s temperature is maintained electrically — and hence cost-efficiently — under constant move-ment by the BENNINGHOVEN mixing nozzle.