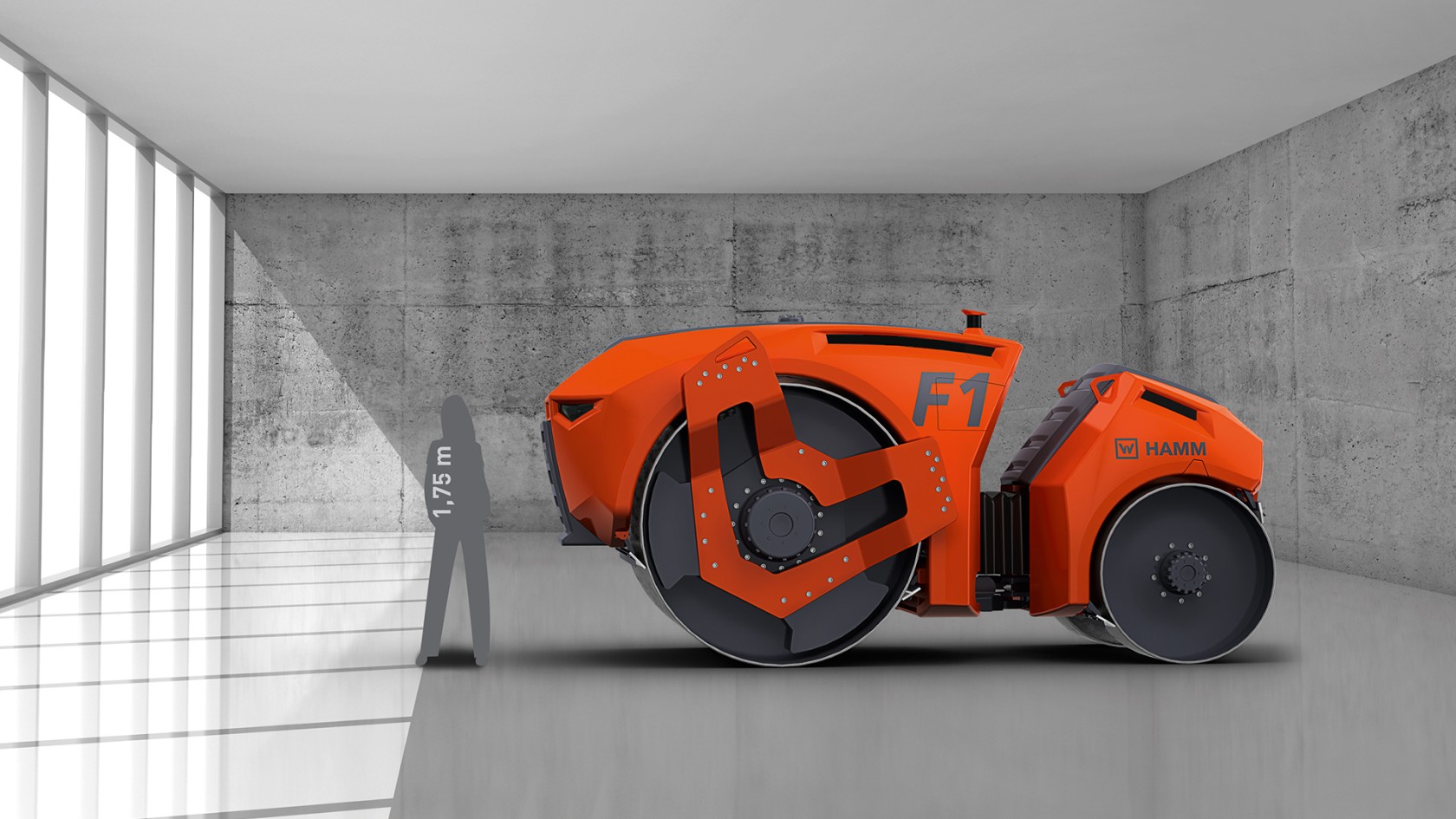
Autonomous vehicles that can move about without human intervention are not yet a part of everyday life, but they are within reach. Also in other areas, products and services relating to autonomous driving or working – such as lawn-mowing and window-cleaning robots – are springing up like mushrooms. While there may be only a small number of self-driving machines in the construction machinery industry, assistance systems are rapidly establishing themselves on the vehicles in the construction sector. In the field of compaction technology, HAMM AG has always been a company that sets trends and is quick to adopt new technologies in order to continually improve its rollers. Now, the technology-focused company HAMM is once again setting new standards, this time in the development of self-driving compaction machines.
The trials currently underway within the limits of a test track are just one component of the future-oriented "autonomous rollers" project. Although it will be some years until HAMM rollers are driving and compacting entirely autonomously, studies and trials at HAMM have already demonstrated that such machines allow compaction quality and efficiency to be noticeably increased. In modern cars and trucks, the use of assistance systems is experiencing rapid growth. GNSS systems for navigation, speed control, spacers, lane assistants, parking and steering aids or automatic switching on and off of the dipped beam are increasingly establishing themselves. In many countries, they are even standard on new vehicles. These assistance systems form the basis of the self-driving trucks and cars that are being developed by industry pioneers, and that are already being put through their paces on test tracks.
Dr Stefan Klumpp, Chief Technology Officer at HAMM AG
HAMM: Trend-setter with self-driving roller
HAMM is a pioneer in this field, affirms mechanical engineer Dr Klumpp: "We know of no other company in our industry with a self-driving roller. Our investigations have shown that such rollers enable our customers to increase compaction quality and efficiency. We have noticed that other leading companies in their sectors are also looking into the opportunities and impacts of the 'autonomous construction site'. For example, we have maintained a dialogue on this subject for some time with a number of our customers. Against the background of limited availability of qualified personnel on the one hand, and high-quality, highly efficient and resource-saving use of machinery on the other, the objective is to further optimise construction processes."
Design study already available
Dr Axel Römer, Head of R&D at HAMM, has already examined with his team what a self-driving roller might look like: "We have considered technical, constructive and economic aspects and evaluated them in various studies. The result: A driverless roller will not have an driver's platform any more but will need significantly more sensors to monitor not only the compaction parameters but also the area surrounding the roller. We have connected these requirements and see many new and constructive possibilities. For example, we could construct autonomous rollers with significantly larger drum diameters, bigger water tanks and more space for the batteries of electrically powered rollers. This offers advantages in terms of quality, environmental friendliness and efficiency."
In collaboration with industrial designers, HAMM has developed and drawn up a corresponding concept and design study. The result is impressive – in particular the drum of the 9 tonne machine with its diameter of just under two metres. At the same time, the overall height of the machine is significantly lower than that of current machines with a cab or roof.
Assistance systems already in use
There is a long road to travel before such a machine will have been realised – HAMM has a horizon of decades for projects like this. The journey, however, has long begun in the sense that numerous assistance systems have come to be used. The HCQ Navigator is especially well known. Using an on-board computer and GNSS data, it provides a real-time display of the areas that have already been compacted, including how often and by how much. This is complemented by driving functions such as automatic reversing or speed control, as well as safety features such as rear-view cameras. All of them relieve the burden on drivers and, even today, help to increase compaction quality. The developers at HAMM are already working on other systems, including a lane assistant, additional steering aids and the further development of the HCQ Navigator.
Complex sensor technology and programming
Significantly more sensors and more intelligent software than can be found in today's machines will be required for rollers that are able to manoeuvre autonomously in carrying out high-quality compaction. The sensors capture all relevant data from the area surrounding the roller. This includes spatial position, direction of travel, distance from other objects, current material parameters of the surface to be compacted (e.g. temperature and rigidity) or weather information (e.g. wind or cooling rate). The rollers must compare this data with specifications for the area (which parts should be compacted?), the rolling pattern (how many and which rollers work together?) or the desired compaction (what is the desired void content?). Also to be considered is the illustration of the compaction strategy, including instructions for cornering before reversing, edge-finishing, vehicle speed, the use of exciter systems, etc. In short: A complex undertaking.
10,000 hours of endurance testing
HAMM has already successfully completed the first steps of the journey. Not just on paper but in practice, in the form of endurance testing at the Tirschenreuth plant, and by developing a driverless "shadowing roller" that follows a preceding machine. The endurance test track has been operational since 2014, with the primary purpose of testing prototypes. Since then, the developers at HAMM have been testing their new developments under reproducible conditions and in around-the-clock operation for weeks at a time – with no driver at the wheel. In these trials, the machines autonomously complete a specified programme, drive themselves to refuelling points and park themselves when the test is completed. To prevent collisions with persons or objects, the developers at HAMM have outfitted the rollers with comprehensive surroundings-monitoring systems. "We have now clocked up over 10,000 hours on this test track and learned a great deal about autonomous driving in the process," explains Dipl.-Ing. Hans-Peter Patzner, who worked on the development of the control system for the project. Patzner is now looking ahead to the next challenge, because the current construction of a second test track at HAMM will enable two different rollers to drive simultaneously. "For this, we have designed a collision monitoring system, which represents another important step towards autonomous driving," says the automation specialist.
Driverless shadowing roller
The second project had a different focus: In collaboration with the University of Osnabrück, the team has successfully converted a roller that, without a driver, automatically follows a simulated road paver. According to Head of Development, Dr.-Ing. Römer, "If you further consider the approach of this 'shadowing roller', we can leverage much potential through the automation of the compaction process. There will be an increase in quality thanks to compliance with lanes and windows of speed. Targeted braking of the roller can avoid going beyond the rolling areas and any subsequent over-compaction. Not least, the extremely precise change of compaction lanes helps to prevent deformation. Together, these systems automatically lead to greater efficiency, in particular when such concepts are applied across the fleet."
Automation for more quality
No matter how autonomous compaction is to be designed – from our present point of view, the way there involves assistance systems. "They will relieve the burden on drivers in the coming years bit by bit, but are already inspired by the vision of the autonomous roller. And, of course, every new assistance function – independently of the vision of autonomous rollers – is beneficial for the compaction process," explains Dr Klumpp. As long as surroundings monitoring is not sufficiently precise for fully autonomous driving, a roller driver will have to be in the cab. He would only take over in specific situations, for example for refuelling, during loading and unloading, or in the event of unforeseen incidents. A similar situation already prevails in the field of aviation: In modern commercial aircraft, the autopilot and other systems carry out the greater part of in-flight tasks. The pilots only control the aircraft during take-off and landing, and in exceptional situations, otherwise their main task is to monitor the processes.
New products necessitate regulatory frameworks
Aside from the technology, there are a number of legal issues to consider before such rollers can be put to work on the "autonomous construction site" of the future. A number of questions arise, such as: Who is liable in the case of damage caused by a self-driving machine – the manufacturer, the owner, the planner? Moreover, questions will have to be answered regarding the assessment of unclear cases: Should the control system be configured such that nearby objects are protected, or should optimum compaction quality always take precedence? Manufacturers and users will have to discuss such aspects with clients, authorities, politicians and legislators.
Improved structure in the construction process
Because the development of autonomous construction machinery will invariably involve a good deal of expenditure on the part of manufacturers, HAMM has also examined the framework conditions for the establishment of such systems. Says Dr Klumpp: "We think that, even in 50 years, asphalt and concrete roads will still be required and constructed. However, to take a step closer to self-driving machines, the general environment must change, including the construction processes. In our industry, self-driving machines are found in the mining sector, for example. There, highly standardised work is carried out in closed systems; there are few points of contact with the outside world and few unforeseeable influences on the process. Under such clearly defined boundary conditions, giant dumpers are already transporting rock across large mines that span kilometres – without a driver. In road building, by comparison, the processes are far less clear-cut and less easy to structure. Every construction site is a little different. There is also much more contact with the surroundings (and thus more potential hazard), and user behaviour is not uniform. So that we can continue to leverage potential through automation, we would have to introduce, for example, larger construction sections and more standardisation in road building. In turn, this requires a change in thinking among planners and construction companies."
Dr Stefan Klumpp, Chief Technology Officer at HAMM AG
From roller driver to roller manager
Ultimately, the job description of the roller driver will also change. First of all, further automation could alleviate the issue of skills shortage. The job description would change again in the subsequent step, when shadowing rollers or largely remote-controlled rollers become established on the construction site: From a driver steering a machine to a roller manager who configures and supervises an entire fleet of machines – perhaps even working from an office. This kind of development will initially occur in the high-wage countries, provided that it entails qualitative and commercial advantages. In this case, it would be the achievement of cost savings through greater efficiency, and with fewer staff. In addition, rework would be eliminated thanks to higher quality. Of course, this will demand suitable interfaces and planning tools on the part of planners and customers, as well as a corresponding legal framework. This environment will have to evolve in parallel with the machines.