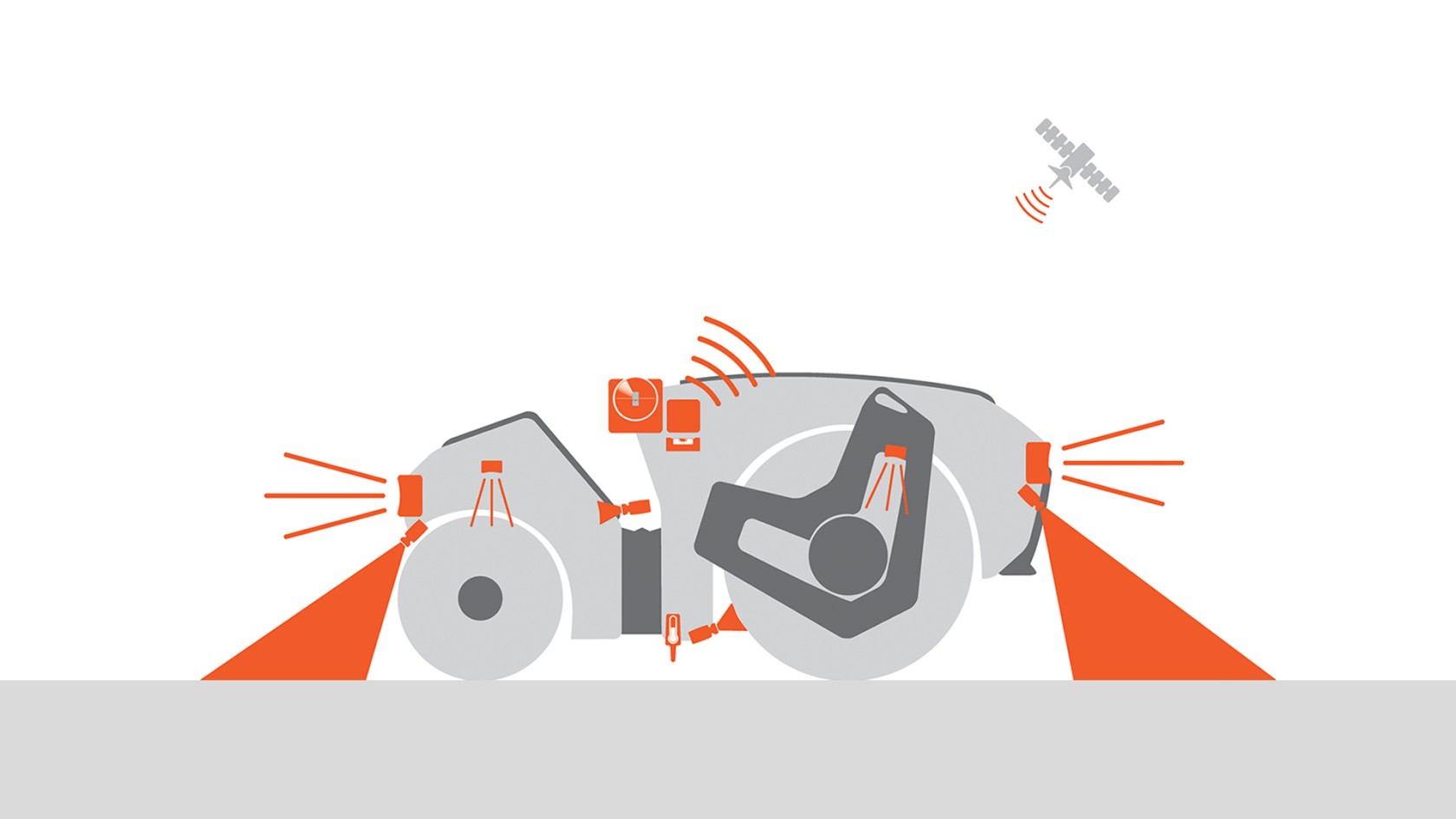
At HAMM, the developers are thinking not only about the next machine generation; they are also focussed on the effects that current megatrends will have on road building in general and on compaction in particular. Here the globally leading roller manufacturer is pursuing a holistic approach taking into account the "hardware" aspects, that is to say trends in machine technology, as well as those relating to "software" such as for example questions concerning the role of people in the construction process of the future. In the Technology Center, visitors to bauma 2019 will have an opportunity to immerse themselves in the "HAMM future".
What will the 'Construction Site 4.0' look like? What added values can HAMM, as a roller manufacturer, contribute to BIM? Which technical characteristics of machines will be relevant in 10, 20, 30 years' time? And what demands will employees place on their working environment in road building in 2030? In addressing these questions, we are developing our visions for the future of road building. From these we generate concrete new concepts and solutions around our core competence, compaction" says Dr Axel Römer, Head of Research and Development at HAMM. In the Technology Center, visitors to bauma 2019 can discover the approaches HAMM is pursuing. On show will be examples of concrete solutions for the present day, concepts for the forthcoming machine generations and studies as to how the vision of the future might look.
The construction site of the future
Digitalisation, electromobility and globalisation are already changing our world today in many ways. Nevertheless rollers will continue to be needed for the compaction of soil and asphalt in the years to come – albeit with growing requirements in terms of process efficiency, precision and transparency. HAMM identified this trend at an early stage and equipped the rollers with numerous assistance systems to aid the driver as well as for process documentation and optimisation. An example of this is the compliance with compaction specifications with the aid of the HCQ Navigator. With WITOS HCQ, HAMM is expanding its offering in this area. The new module enables the compaction progress to be monitored – in real time as well as remotely. For example, construction managers will in future be able to obtain comprehensive information on the progress of construction at any time without having to be on site. They will be able to control processes from the office and take decisions on the basis of qualified information. This in turn brings savings in travel time and costs and enables quality improvements to be achieved through timely interventions. HAMM also sees the potential for even greater efficiency in the optimisation of machine utilisation with the aid of WITOS FleetView. It facilitates maintenance and diagnostics, speeds up response times in the event of faults and also enables systematic analyses of operating and user behaviour. Finally, regular maintenance and timely, cost-optimising replacement of wearing parts increases roller availability. At the same time, unscheduled downtimes, often involving transport costs and organisational work, are avoided.
Remote-controlled rollers and autonomous driving
Another HAMM approach for the workplace of the future is a remotely controlled compactor that has already been operating for two years at a quarry in Germany. In the Technology Center, visitors can form a picture of the application and experience what is already possible today.
If the remote control concept is projected further down the line, the so-called shadow rollers quickly lead on to autonomously operating rollers. HAMM has adopted a scientific approach to the subject and has for the first time visualised the thinking on the subject in the form of the "Autonomous Roller F1". This is not based on an actual machine, but is a study on the compaction of the future. It shows what a driverless roller with alternative drive concepts might look like and what technical, organisational and economic opportunities might be derived for road building. At the end of 2018, HAMM was accoladed with the "Best of Best" award at the Automotive Brand Contest 2018 in the category "Commercial Vehicles" for this innovative vision of the future. Added to this achievement was the "German Design Award 2019 in Gold" in the category "Utility Vehicles" at the beginning of 2019. Both are prestigious design prizes awarded by international juries from the automotive and design worlds.
The working environment of the future
The progressive developments are also set to transform workplaces in the compaction sector. Obviously, however, a totally autonomous, driverless construction site remains in the distant future. This is the reason why in recent years HAMM has developed the Easy Drive operating concept for the current generations of tandem rollers, compactors and pneumatic tyre rollers. HAMM has consequently succeeded in simplifying and standardising the operation of the rollers. HAMM has, therefore, taken ergonomics and operator comfort to a new level. The company will continue to pursue this path in the years ahead and is presenting a new cabin concept at bauma 2019. With even more space and scope for individual adjustment of the workplace, the working environments in the next generation of rollers will be even more agreeable and comfortable than before. Another aspect is the presentation of information for the roller drivers. The developers are currently working on alternative concepts for the integrated display of all machine and construction site data. Here the emphasis is providing the drivers with clear and comprehensive information on the machine and the compaction process enabling them to record and evaluate the status quickly and easily. This brings about an improvement in compaction quality, while reducing the physical burden.
Sustainable construction
The ever-growing importance of the "environmental friendliness" megatrend for rollers in the years to come is already becoming apparent today. "Protecting the environment and cutting costs often go hand in hand," says Dr Axel Römer. This is demonstrated by the latest solutions from HAMM in the Technology Center on the subject of sustainability: For example, the power hybrid technology, engine stop function and Eco mode ensure reduced fuel consumption and thus lower exhaust gas and noise emissions. One of the biggest tasks for developers in the coming years is the adaptation of the rollers to the requirements of the next exhaust emission standard (EU Stage V). This makes the rollers even more environmentally friendly. The sustainable compaction range is already complemented by a range of technologies – for example, with oscillation compaction, the number of passes can be reduced. Another example for sustainable construction is the HCQ Navigator. Through process optimisation, it facilitates faster and more homogenous compaction, which ultimately saves energy, time and costs.
Continuing to optimise compaction
In general, the exhibits at bauma 2019 emphasised that HAMM will be remaining true to itself and offering the construction sector innovative solutions regarding the core competence of compaction in the coming decade, too. In line with this, HAMM is premiering a new development, a split oscillation drum, in Munich. This patented solution combines the advantages of oscillation with those of a split drum.
"As the trendsetter and driving force of the compaction sector we will continue to forge ahead and develop in a sustainable way in the years to come – and that is to say with equal emphasis on asphalt construction and earthworks. To this end, we maintain an active dialogue with our customers and will continue to serve as a partner to the construction industry in the years ahead," stresses Dr Stefan Klumpp, Chief Technology Officer at HAMM.