If the mixing plant is located too far away or the construction site doesn’t meet the logistical requirements to conduct the entire recycling process in one pass, cold in-plant recycling is often the perfect solution.
Crushers and Mixers On the Move
Cold in-plant recycling
During cold in-plant recycling, a mobile cold recycling mixing plant is set up near the construction site. The materials to be recycled are brought to this plant by truck, processed, and transported back to the construction site by truck as a high-quality finished product and directly used to pave the road surface. This approach is popular in road construction, but is also possible in demolition recycling. The process makes financial and environmental sense because the short distances between the construction site and the cold recycling mixing plant save time, money, and miles driven. Various machines and plants from the WIRTGEN GROUP work together during the cold in-plant recycling process.
“The mobile concept of the WIRTGEN cold
recycling mixing plant means the plant can
be used in the direct vicinity of the operation
site, saving both money and time.”
Demolition Recycling
If a building is demolished, for example, the building’s concrete can be recycled. Within this process, we can unlock synergies between KLEEMANN and WIRTGEN plants. First of all, the concrete must be crushed. There is often a challenge to overcome in this regard, however: reinforced concrete. With reinforced concrete, you often don’t know exactly how hard the concrete is and how much steel it contains. This can push many crushers to their limits.
The MOBIREX MR 130 Z EVO2 from KLEEMANN is perfect for this job. The mobile impact crusher has an optimized inlet geometry for better feed characteristics. In addition, the crusher inlet flap, which can be raised hydraulically, and the upper crusher impact swing arm prevent jamming at the entrance to the crusher unit. In addition, the continuous feed system via sensors ensures that the crushing chamber is filled in an ideal manner.
„With the help of KLEEMANN impact crushers, high-quality cold mixes can be produced.”
It couldn’t be any easier or safer
Overload protection shields the crushing unit from large metal parts such as T-beams. Sensor-controlled hydraulic cylinders allow the impact swing arm to move back when an unbreakable part enters the crushing chamber. The metal part is diverted and transported to the crusher discharge belt, which can be equipped with an optional magnetic separator. The electric or permanent magnet attracts the metal part and throws it to the side so that the crushed concrete is fed into the secondary screening unit without reinforcement.
The secondary screen sorts the crushed concrete into different grain sizes. Oversized material is returned to the crusher unit via the oversized material return belt in a closed loop. All of the MOBIREX MR 130 Z EVO2’s functions can be controlled via the simple and intuitive SPECTIVE control concept. For example, the crushing gap can easily be adjusted to the desired size via touch – even while the rotor is in operation. It couldn’t be any easier or safer.
The concrete aggregate with the desired gradation is then fed into the WIRTGEN KMA 220 via wheel loader or directly from the crusher. The cold recycling mixing plant mixes the concrete with binding agents and water to produce a high-quality final product, e.g. for a hydraulically bonded base layer that can then be immediately used for repaving. Due to the mixing location in the immediate vicinity of the demolition site, not much time passes between demolition and paving in the cold recycling process.
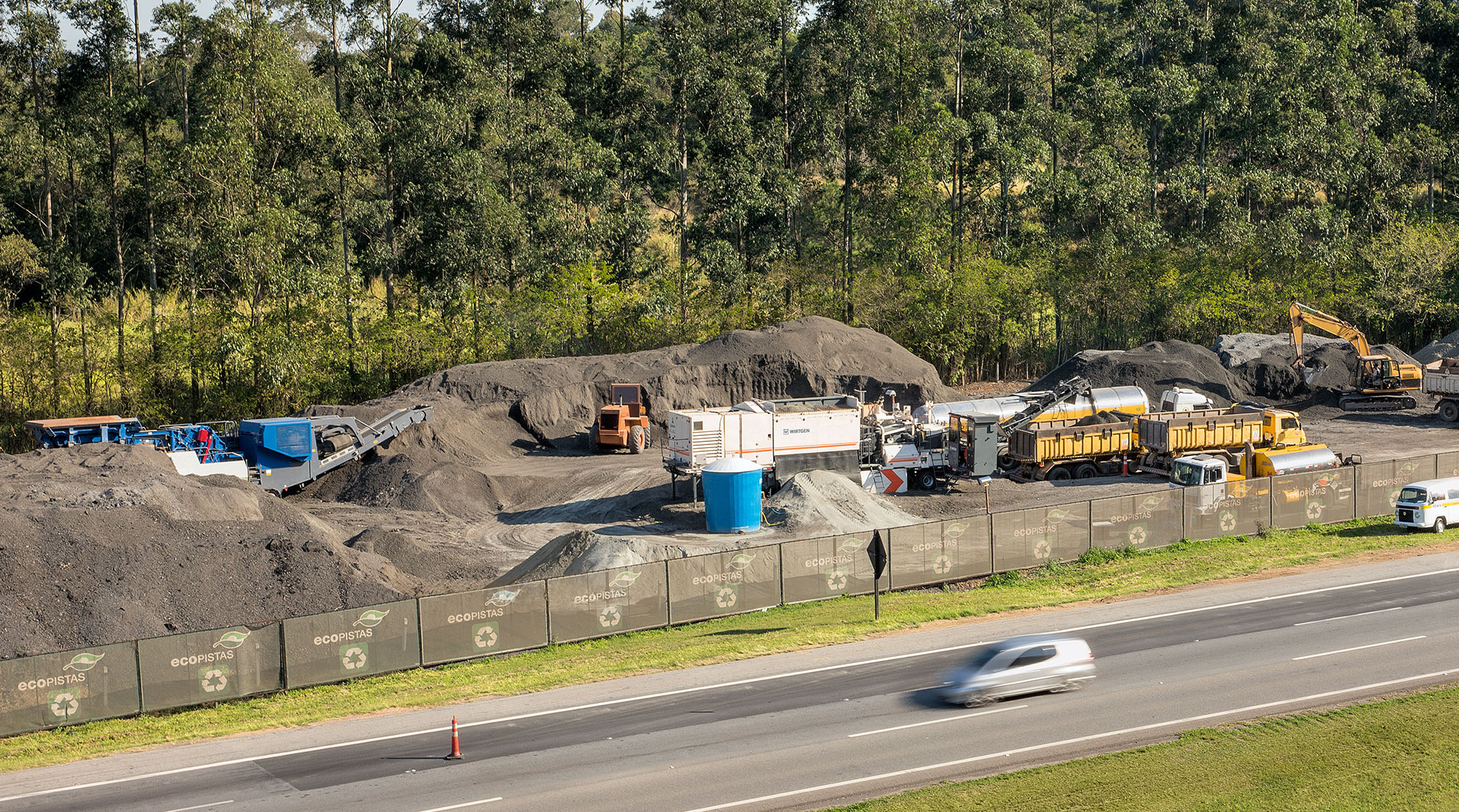
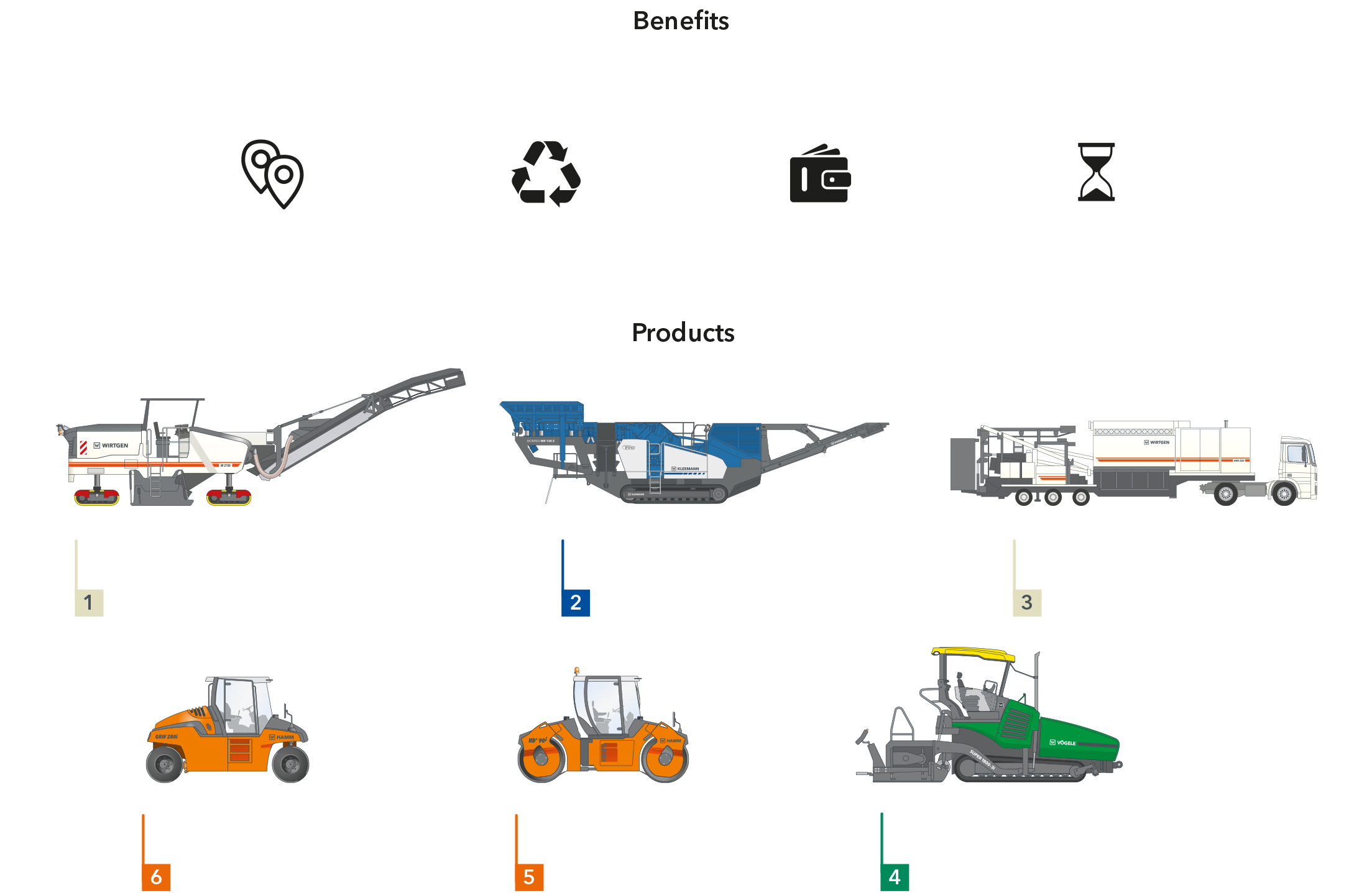
Example Application: Road Rehabilitation
Even more machines from the WIRTGEN GROUP can be combined in road construction. During road rehabilitation, the layers in need of rehabilitation can be milled out with a Wirtgen milling machine. The removed material is then transported by truck to the mixing site near the construction site. These materials are then processed in a Kleemann impact crusher at the mixing site. The milled material is transported by a Deere excavator or wheel loader to the crushing plant where it is crushed down to the required aggregate size.
The cold recycling mixing plant is fed by a John Deere wheel loader or directly from the crusher. In the cold recycling mixing plant, the recycled material is mixed with water and binding agents such as foamed bitumen, bitumen emulsion, or cement. The cold mix is then transported back to the construction site, where it is paved using a VÖGELE paver. Last but not least, the surface is compacted by a HAMM compactor. This is how WIRTGEN GROUP machines and plants complement each other perfectly. Where one plant stops, the next begins its work – for perfect results from a single source.