The efficiency turbo.
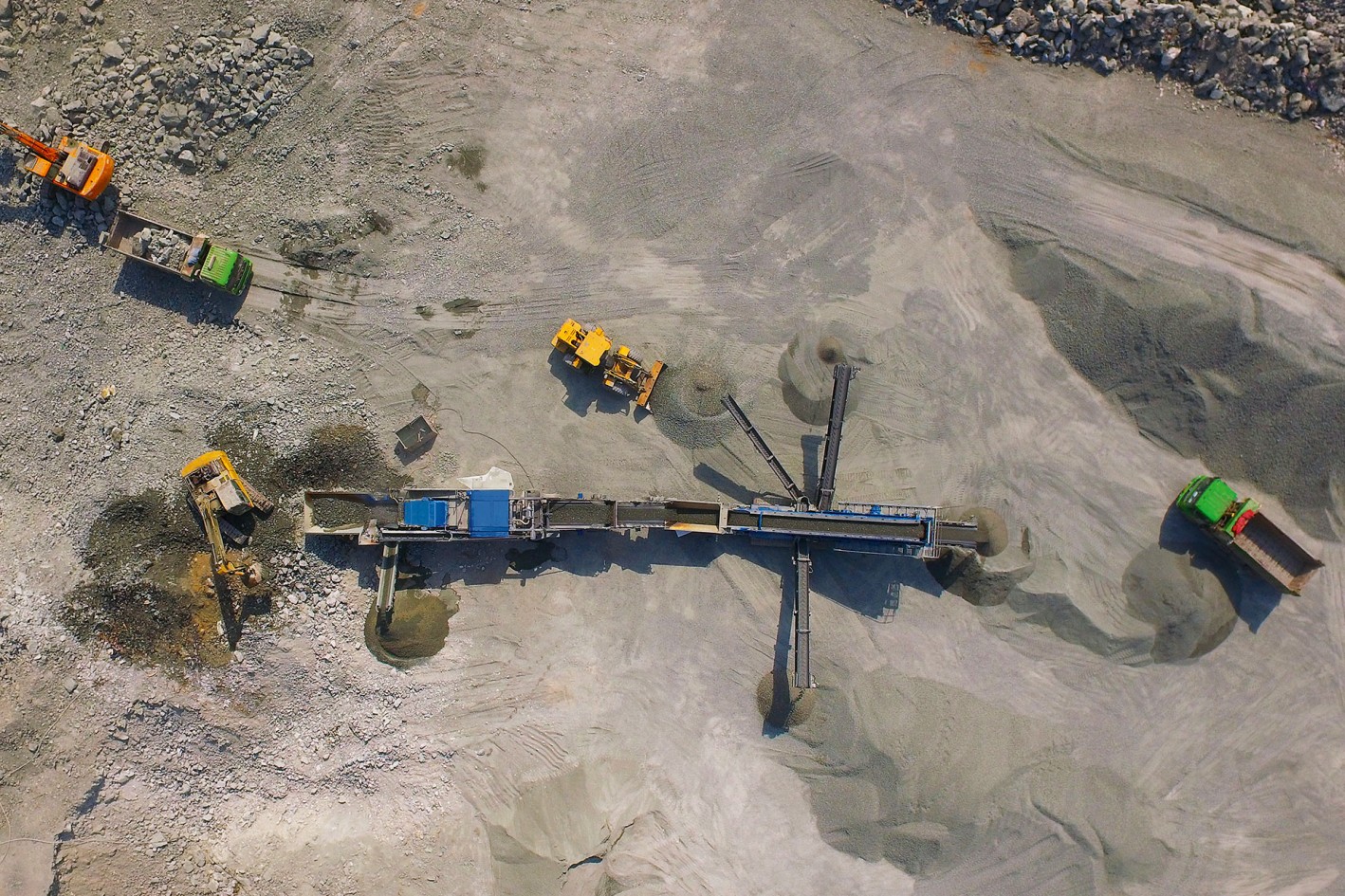
XXIV Winter Olympics, Beijing 2022: the Xingyan Highway is a part of the Olympian infrastructure.
A MOBIREX impact crushing plant keeps the transport routes in Beijing short and converts excavated tunnel material into first-class raw material.
A tunnel as a raw material supplier
The Xingyan Highway was an ambitious new construction project with a length of 42 km with four lanes, which has been opened to traffic in the meantime. The new stretch connects the Northwest 6th Ring Road in the metropolitan area of Beijing with the Yanqing District and was constructed with the 2022 Winter Olympics in mind. The national Ski-Alpine Center and the national Bob and Toboggan Run Xiaohaituo are under construction in Yanqing District.
On the way there, in Changping District, the construction company China Railway Construction Corporation Limited (CRCC) won contract section III of the highway. The greatest challenge: the construction of two tunnels with a length of 3.5 km – one tunnel per direction of travel. The team demonstrated on site impressively how money can also be made with stones that lie in the way instead of just creating disposal costs. A key role was assigned to a KLEEMANN impact crushing plant of type MR 130 Z EVO2. It processes excavated tunnel material to create a new raw material for construction of the highway.
Conserving resources, saving costs through recycling directly on the site with the transport-friendly,tracked mobile KLEEMANN plants.
Economic further utilization
Recycling of the excavated tunnel material helped achieve two central objectives: conservation of resources combined with savings on costs. Recycling plays an important role for CRCC – in this area, the technologies from KLEEMANN provided valuable support.
The bulk of the material, 300,000 m³ of limestone, was processed near to the tunnel construction site. This is also made a big contribution to efficiency and thus cost-effectiveness. After all, short routes mean: fewer trucks, less fuel, lower emissions. When they arrived at the work site, the construction vehicles unloaded the stones, where bucket excavators then loaded them into the MOBIREX. Following the crushing process, the MR 130 Z EVO2 transferred the material to a MOBISCREEN triple-deck screening plant MS 19 D. Overall, four classified final products were thus created with an output of 230 t/h. The plant team even had large capacity reserves as the maximum output is twice as high.
Following construction companies to practically every work site
The mobile crushing and screening plants from KLEEMANN guarantee short transport routes because, with their crawler chassis, they reach places where the stone is extracted – or, in this case, near a tunnel construction site.
Mobile impact crusher
Drive concept | D-DRIVE (Diesel-direct) |
Max. feed size | 41 in x 26 in x 16 in |
Feed capacity up to approx. | 496 US t/hr |
Mobile classifying screen
Drive concept | H-DRIVE (Diesel-hydraulic) |
Max. feed size | 7 in x 4 in x 3 in |
Feed capacity up to approx. | 551 US t/hr |