In industrially developed countries, significantly more roads are rehabilitated or extended than completely new roads are built. But what happens to the old road surface?
The Asphalt Cycle
“BENNINGHOVEN offers recycling
technologies – whether hot or cold
feed system – for every customer
requirement.”
BENNINGHOVEN asphalt plant
Recycling asphalt is an economic imperative in order to conserve natural resources. Using the maximum amount of recycled asphalt not only protects the environment, it also positively affects RAP prices.
BENNINGHOVEN offers a wide range of "hot and cold" recycling feed systems designed to produce the highest quality RAP. The recycling technologies can also be individually customized and integrated to retrofit existing asphalt mixing plants. The maximum theoretical amount of asphalt that can be added depends largely on its grading curve – or, to put it another way, on the quantity, size, and composition of its constituents. As a result, one goal must be to align the grading curve of the crushed asphalt as closely as possible to the desired grading curve of the final asphalt product.
MOBIREX MR 130 Z EVO2
This is where the MOBIREX MR 130 Z EVO2 mobile impact crusher from KLEEMANN, equipped with a secondary screening unit, comes in. The ability to flexibly adjust the rotor speed and the crushing gap via a touch panel makes it possible to achieve the desired grading curve.
First, however, the asphalt must be recovered by removing individual layers of the road structure. Cold milling machines are perfect for this because they are capable of selectively milling these layers. As a result, it’s possible to remove the surface layer, binder course, and base layer separately and recycle them separately.
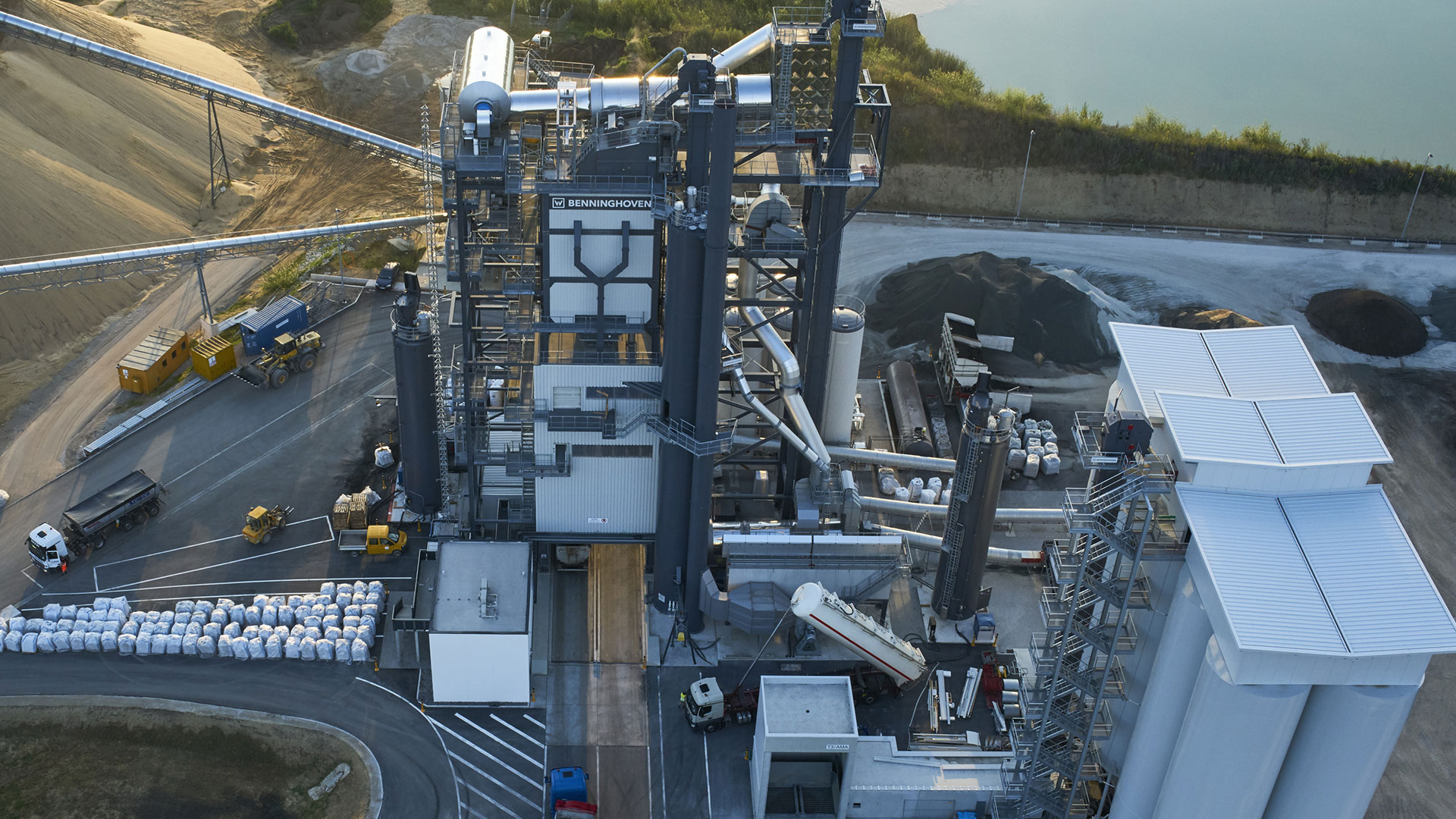
Hot Gas Generator with Counterflow Parallel Drum System
- More than 90% + x recycled material can be added
- Highest possible rates of added recycled material
- Material heated indirectly
- Lowest emission values Cges < 50 mg/Nm³
- Total energy required to operate the plant decreases
- RC material is already heated to processing temperature (160°C) through this process
“WIRTGEN’s levelling technology allows
surface layer, binder course and base course
to be milled selectively and fed back
separately into the material cycle.”
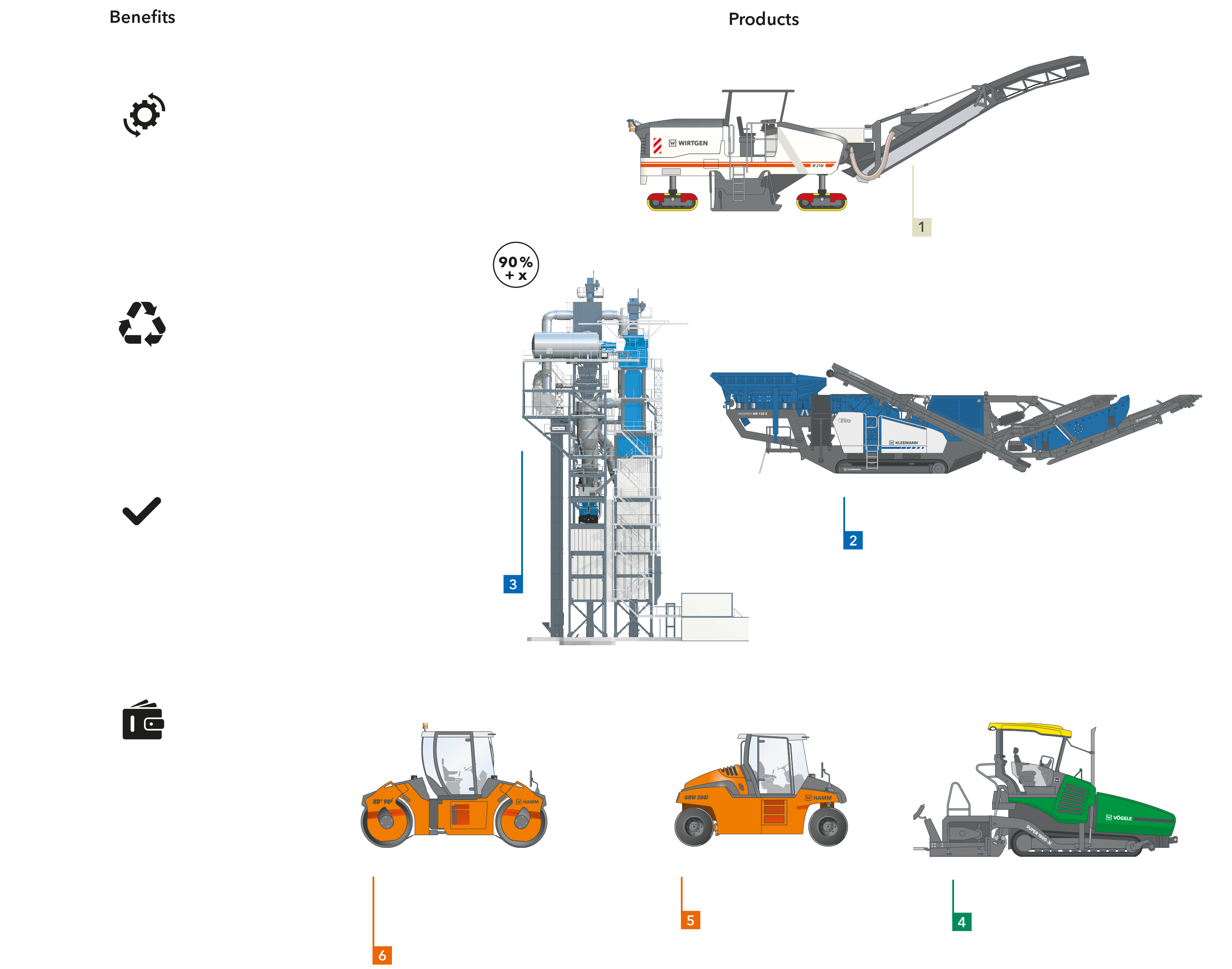