Roads have to withstand heavy loads, which over time lead to fatigue and deterioration and cause serious long-term damage. As long as only the top layer of the road structure is affected, surface layer rehabilitation is an appropriate maintenance measure.
Fast and Effective
The focus of maintenance work is usually on improving surface quality.
This includes keeping the surface watertight and ensuring that drainage measures are effective so that no water on the road surface or along the edge of the road can cause damage such as ruts, potholes, fractures, and cracks on the asphalt surface.
Heavily trafficked roads are lifelines for the regions and cities that are connected by them. This is why contractors and public authorities also have to consider the effects of construction sites on traffic and the economy when planning the maintenance of important connecting roads. This is one reason why surface layer rehabilitation is so common in road maintenance – because of the speed with which it can be completed.
Only an undamaged asphalt surface layer can fulfill its role of preventing the penetration of surface water into the bituminous surface layer and ensuring that the surface remains safe to drive on for many years. This is why during surface layer rehabilitation, the damaged asphalt layer is removed and replaced with fresh hot mix asphalt (HMA). The challenge in this process is to only remove and replace the damaged layers of the road structure – while at the same time obstructing traffic as little as possible. As long as the road bed is not damaged, this is an adequate solution.
“WIRTGEN large milling machines
are powerhorses for large-scale removal.”
Profile-Perfect Milling Lays the Foundation
The maintenance process begins with the cold milling machine. Its job is to remove the asphalt surface layer and lay a level base for the subsequent asphalt paving work. The removal of asphalt pavements via cold milling is unrivaled in terms of both logistics and speed of execution. As the market leader, WIRTGEN offers the widest range of cold milling machines. The results of the milling operation play a pivotal role in determining the quality of the new surface layer to be paved, its functional properties, and the efficient and cost-effective completion of further construction work. During surface layer rehabilitation, the cold milling machine prepares the surface perfectly so that the asphalt paver can begin to work next without the need for corrective measures.
“The ECO plant’s components are based
on ISO freight container dimensions.
This makes transportation and relocation
quick and cost effective.”
Paving High-Quality Hot Mix Asphalt
After the milling work is completed, pavers lay a new surface layer which is then compacted by compactors. The material of choice for surface layer paving is HMA with the corresponding specifications. Even if the binder layer was damaged during milling, the surface layer generally consists of only one asphalt layer, because paving different layers of material would require more preparation and increased logistics, making it impossible to complete the job quickly.
Asphalt consists of rock, filler (rock flour), and bitumen, which are thermally processed into a material mixture at high temperatures. This mixture can be produced either in batches or continuously in an asphalt mixing plant. BENNINGHOVEN is the WIRTGEN GROUP specialist for high-quality, batch-production asphalt mixing plants. Here, the components of the asphalt mixture are first weighed before they are mixed in batches in the asphalt mixing plant according to a specific recipe. The batch production process is very flexible, since the recipe of the mixture can be changed for each batch. This allows BENNINGHOVEN asphalt mixing plants to easily deliver material for various projects within a tight time frame.
CIBER is the WIRTGEN GROUP brand that specializes in con-tinuous asphalt production and is available in Latin America, Africa, Oceania, and Southeast Asia. In the continuous process, the production cycle runs without interruption and the asphalt mixture is not produced in different batches.
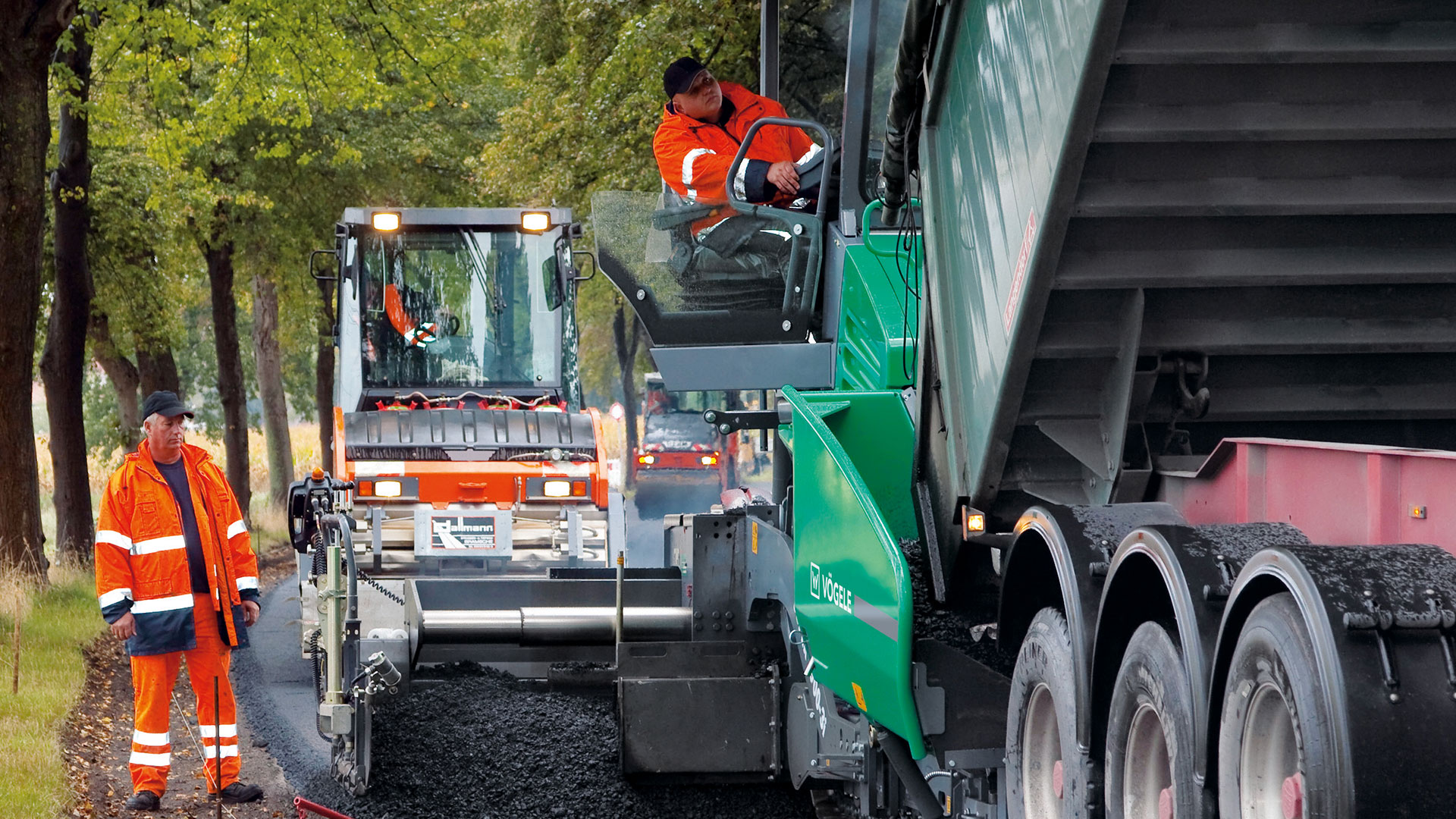
The cost-efficient route to high quality paving
Paver technology plays a crucial role when producing an asphalt pavement of impeccable quality, true to line and level. And this is where VÖGELE come into play: with 50 different pavers and 26 screed types, the world market leader offers the right solution for every paving scenario – from narrow park paths to runways at international airports. A very diverse range of requirements must be met when paving surface courses:
firstly, the paving process must proceed as efficiently and economically as possible; secondly, the resultant pavement must be absolutely even and, on highly frequented roads, it must also be able to withstand maximum loads. VÖGELE have developed the SUPER 1800-3i SprayJet paver with just this in mind: it can pave thin layers hot on spray seal as well as conventional surface and binder courses. Using its five spray bars with a total of 24 nozzles, the paver applies bitumen emulsion, overlaying it with thin asphalt surfacing in one and the same pass.
High quality surface courses can be produced particularly economically by these means. MT 3000-2i Offset or MT 3000-2i Standard PowerFeeders are used on large job sites, such as motorway rehabilitation projects, which require a particularly high material throughput, uninterrupted paving and the non-contacting transfer of mix. Among other things, they prevent costly interruptions to paving and jolts during the transfer of mix, guaranteeing high quality paving. Using the VÖGELE InLine Pave process, contractors can also pave binder and surface course "hot on hot" in a single pass. With this method, a paver for binder course, a paver for surface course and a material feeder operate one behind the other, leaving one lane open to traffic. This is hence an ideal solution for the rehabilitation of heavily trafficked roads.
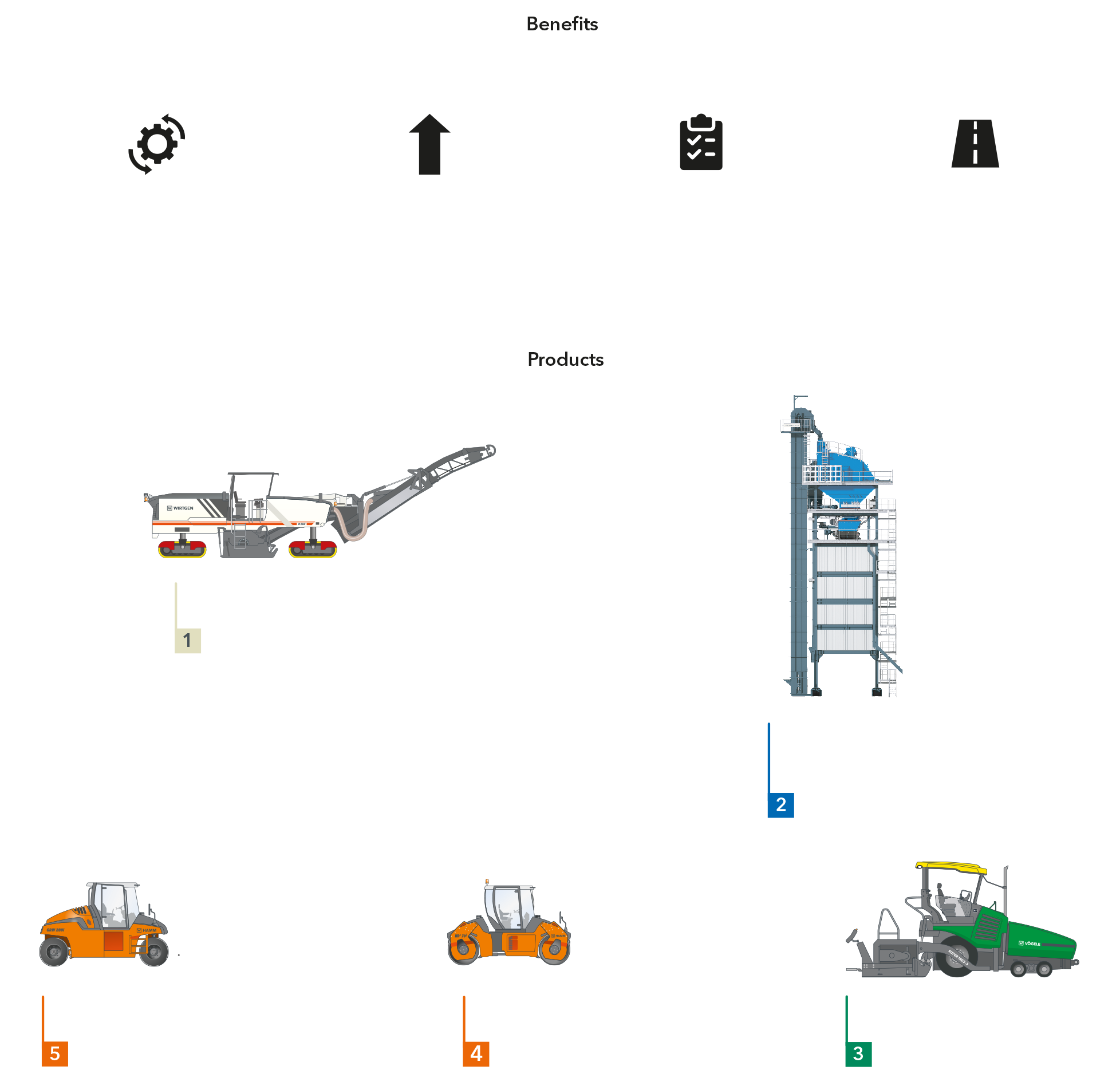
The Perfect Surface
The complete, uniform compaction of the asphalt surface is essential to maximizing the performance of the newly paved asphalt. The purpose of compaction is to bond the asphalt-coated aggregates together to achieve stability and resistance to deformation (or rutting), while reducing the void content of the mixture and improving its durability.
By paving with high-compaction screeds, the compactors moving behind the paver achieve the final density specified by the customer in fewer passes. In most cases, the road paver is designed for either high compaction or fast speed, which affects the number of passes required. The fast and high-grade compaction of the asphalt surface must be carried out by high-performance asphalt rollers while the asphalt is still hot (~160 °C to 100 °C). The ideal temperature range depends on the composition of the mixture, the thickness of the pavement, and the type of bitumen used.
Choosing the right compactor is an extremely important step. HAMM tandem rollers with vibration and oscillation guarantee fast, cost-effective, and high-grade dynamic compaction. Tandem rollers with an oscillating and a vibrating drum are particularly suitable for achieving higher degrees of compaction than tandem vibratory rollers, and save time due to a lower number of passes. In this case, one drum oscillates (tangential shear forces) while the other drum vibrates (vertical forces), which significantly increases the compaction effect.
Working with reliable equipment is essential to achieving the high level of performance and speed required on the job site. It is also critical that this maintenance activity is carried at the right time before the road quality drops drastically. Then the pavement and asphalt base layer can remain untouched for countless years. With the 360° machine solutions from the WIRTGEN GROUP, the maintenance cycle can be efficiently closed so that one section of road’s milling, paving, and compaction processes can be carried out in the shortest possible time.