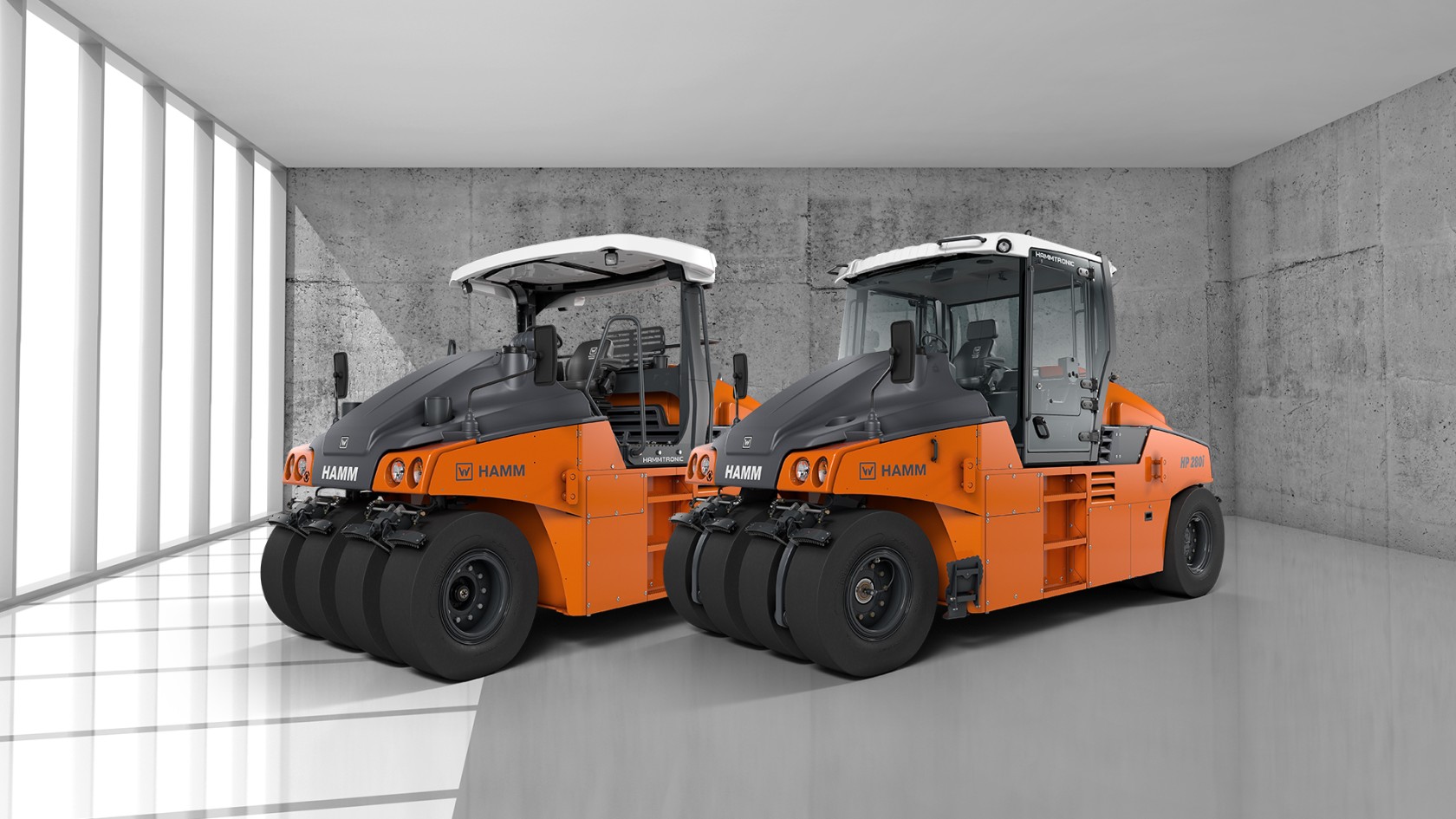
With the HP series, HAMM is presenting a totally new generation of pneumatic tire rollers. The series is full of technical innovations and advances – especially in relation to the operator's platform, the water and additive sprinkling system as well as the ballasting.
In the 1960s, HAMM, the pioneer in the compaction sector, launched the GRW. The machine concept of the pneumatic tire roller was revolutionary at that time, and HAMM has continued to develop these machines up to the present day. Now, a good 50 years later, the compaction specialists from Bavaria are again launching a new generation of this roller type: the HP series. It will replace the existing GRW series worldwide by the end of 2020.
One platform for all markets
For the HP series, HAMM has developed a common platform for all model variants in every market throughout the world. HAMM will also continue producing the pneumatic tire rollers in different basic versions. First, there are the type HP 180 and HP 180i models with operating weights of 8 t to a maximum of 18 t. Second, there are the HP 280 and HP 280i models with operating weights between 10 t and a maximum of 28 t. Here, HAMM is providing the individual markets with the particular models to suit the locally relevant weight classes and equipment variants. The models HP 280i (Tier 4 final), HP 280 (Tier 3) and HP 180 (Tier 3) are already available.
Operator's platform with first-class field of vision
As is customary with HAMM, the new HP series pneumatic tire rollers also offer a modern, spacious operator's platform or panoramic cabin with maximum visibility over the machine and the construction site. In this respect all models comply with the new ISO 5006-2017 operator’s field of view standard which is markedly stricter than the previous provisions. In terms of machine design, HAMM is sticking with the proven asymmetrical frame concept in the HP series. This is not only a hallmark, it is also a quality advantage because it follows the track offset between the front and rear wheel sets and always allows a clear view of the outer flanks of the front and rear wheels.
Clear operating concept
Clarity and an unimpeded overview also prevail on the operator's platform. For example, on all models the operation is designed to be totally language-neutral and is very easy to learn. The minimal number of switches on the operator’s platform is intelligently arranged. User guidance is assisted by the unambiguous color-coded grouping. Drive control is via a joystick ergonomically positioned on the armrest. Numerous other details in the driver's cab ensure abundant comfort and a healthy working posture for the driver.
Flexible ballasting as standard
Another feature that users have come to expect from HAMM is the flexibility in terms of ballasting: the operating weight is quickly adjustable to suit the asphalt type, layer thickness and application. Here, the HP series offers considerable latitude with its variable ballasting concept. For example, prefabricated ballast bodies made of steel or normal or heavyweight concrete can be inserted into or removed from the large ballast compartments between the wheel sets using a fork-lift truck, for example. This can be carried out in the user's workshop or on the construction site. HAMM offers various ballast body kits for this purpose allowing different weights to be achieved. Because the ballast spaces are located in the center of the machine, the weight is always evenly distributed over both axles – perfect conditions for optimum compaction quality. Additional ballasting of up to 17 t is possible, depending on the basic weight.
Highest possible operational safety included
In addition, the HP series also scores in terms of safety. Drivers can always reach the brake pedal quickly and reliably because it is an integral part of the seat-operating unit on all HP series models. This makes for the maximum possible operational safety because the brake is always easily accessible, irrespective of the seat position. This aspect is especially important particularly for heavy rollers weighing well over 20 t.
Generous tank volumes for high productivity
The new HP series pneumatic tire rollers are visually identifiable by the large, newly designed water tank. Like the diesel tank, it is generously dimensioned so that the machines have sufficient capacity for a full working day without stopping to refill. For this reason alone, the rollers are already extremely productive.
Supplementary water tank: Ballasting and water reserve
HAMM also offers a supplementary water tank with a volume of 1,500 l for all HP series models. It may be used as a water reservoir for the sprinkling system, but also serves as an easily quantifiable, flexible supplementary weight. Operation of the supplementary tank is remarkably easy because it is connected to the basic water tank by means of interconnecting pipes. To facilitate fast refilling, the developers have provided a C-pipe connection to complement conventional filling. It enables the entire tank to be filled in around three minutes. A pump is also fitted to allow complete discharge.
Innovative additive sprinkling system
HAMM has also optimized the additive sprinkler system for the new HP series due to the profusion of special asphalts that tend to be difficult to process. High-quality compaction of these construction materials calls for sprinkling of the pneumatic tires with an additive. Previously, the additive concentrate was mixed with water and then filled into a separate tank on the roller. On the new machines, the additive concentrate is simply filled without premixing. The dosage from the large additive tank with level monitoring can be controlled from the operator's platform in various addition levels. The roller doses and mixes the additive during the compaction in accordance with the specification. This also brings about an increase in quality, because HAMM avoids separation of the additive-water mixture by virtue of the design. And last but not least, swapping from water to additive can easily be done at any time directly from the operator's platform.
Perfect maintenance – with safety assured
When it comes to maintenance, the developers have also attached importance to efficiency and safety. For example, all daily maintenance items are situated on the right-hand side of the engine. Engine access has also been intelligently and safely designed on the HP series: the steps are integrated in the outer contour and are opened outwards in one easy operation. Because they visually protrude in this position, the operator cannot forget to retract the steps on conclusion of the maintenance work.
Pneumatic-tire roller
Drum width | 72 in |
Weight | 20,959 lbs |
Exhaust emissions category | EU Stage V / EPA Tier 4 |
Pneumatic-tire roller
Drum width | 72 in |
Weight | 18,776 lbs |
Exhaust emissions category | EU Stage V / EPA Tier 4 |