Slipform pavers
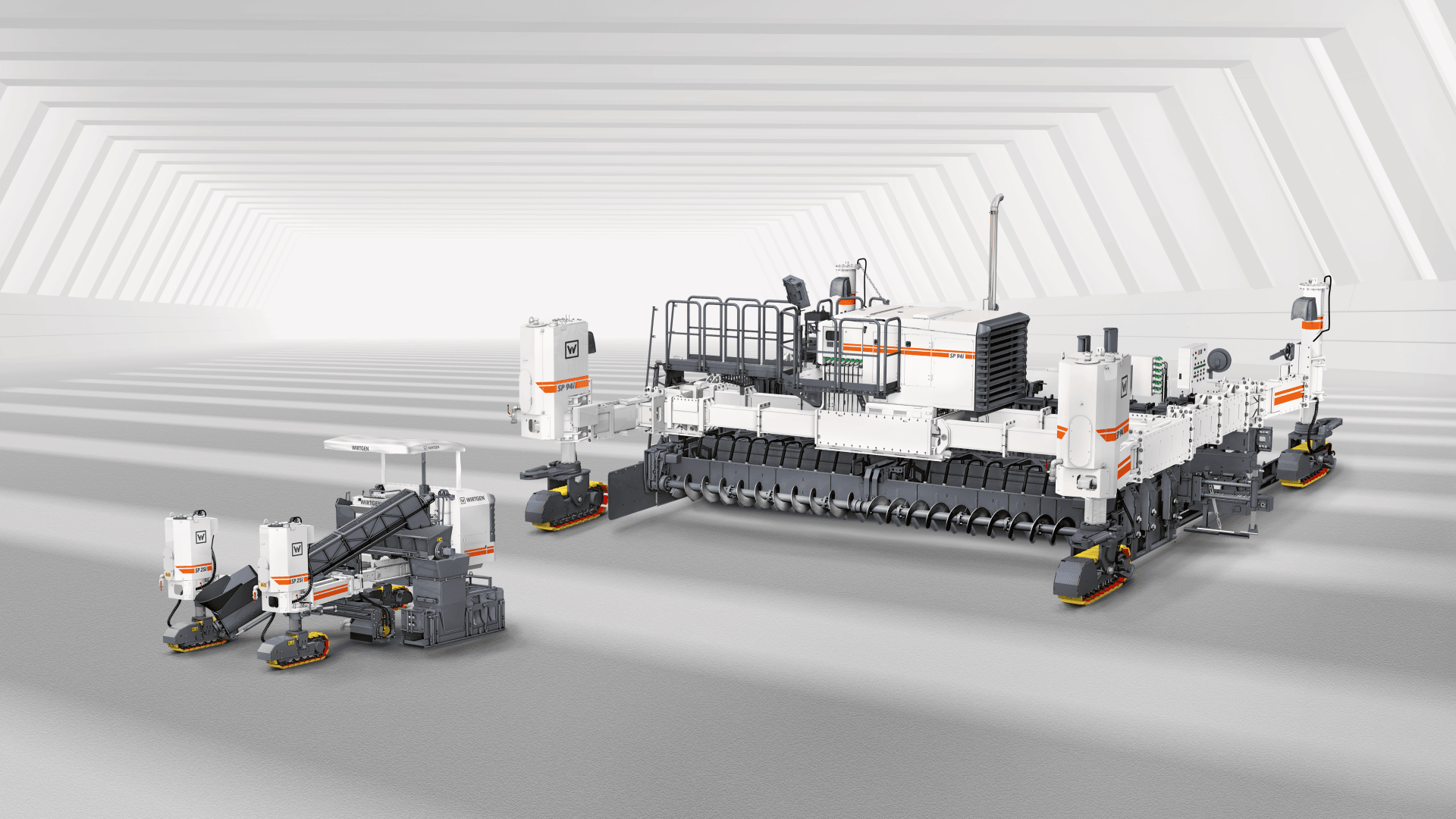
Offset pavers are used to produce monolithic concrete profiles such as protective concrete walls, kerb profiles, gutters or narrow paths. Thanks to numerous options, such as for concrete feeding or slipforming, offset slipform pavers are extremely versatile. Inset pavers cost-effectively produce concrete pavements, such as for motorways, arterial roads, runways or railway lines. In addition to single-layer concrete paving, bottom-layer and top-layer concrete can also be paved synchronously in two layers ‘wet on wet’.
With offset slipform pavers, the concrete is transported into the offset mold via a loading conveyor or a conveyor auger. The offset mold can be mounted on the left or right-hand side of the machine. A number of molds in a wide range of different shapes and sizes are available for individual applications. The offset profiles are continually produced monolithically, with or without reinforcements. Machine features include a top-quality machine control system, a practical steering and drive system and stringline-free concrete paving.
With inset slipform pavers, the concrete is placed directly in front of the machine and distributed by a spreading auger or spreading plough. Vibrators compact the concrete homogeneously and the mold forms it in the specified width and thickness as the slipform paver advances. Integrated dowel bar and tie bar inserters position dowel bars and tie bars as specified. The finishing beam levels the area transverse to the pavement and the super smoother creates a perfect surface. When paving dual-layer concrete, the bottom-layer and top-layer concrete are processed simultaneously and paved wet-in-wet.
Texture curing machines give the concrete pavement the desired surface texture, applying a dispersion which prevents the surface and edges from drying too quickly. The specified surface texture is achieved with a brush. Alternatively, a burlap or synthetic turf can be drawn across the concrete pavement in a longitudinal direction. Automatic crown adjustment and a film unwinder round off the features of the machine.
Texture curing machines
Working width max. | 32 ft |
Working height | 1 ft 8 in |
Rated power | 55.4 kW / 74.3 hp |
Operating weight, CE | 17,196 - 25,574 lbs |
Texture curing machines
Working width max. | 59 ft |
Working height | 1 ft 8 in |
Rated power | 55.4 kW / 74.3 hp |
Operating weight, CE | 20,062 - 40,565 lbs |
If reinforcement needs to be laid in advance during the construction of concrete roadways, the concrete can be fed in laterally using a placer/spreader. The placer/spreader travels in front of the slipform paver over the pre-placed reinforcement, while a truck mixer feeds the belt conveyor with concrete from the side. The concrete is poured evenly over the pre-placed reinforcement, in front of the slipform paver, and distributed across the entire working width. Once the truck mixer is empty, the belt conveyor can be folded away in a very short time to clear the path for the next mixer.
All details, illustrations and texts are non-binding and may include special equipment. We reserve the right to make technical changes without prior notice. Performance data are dependent upon actual operational conditions.